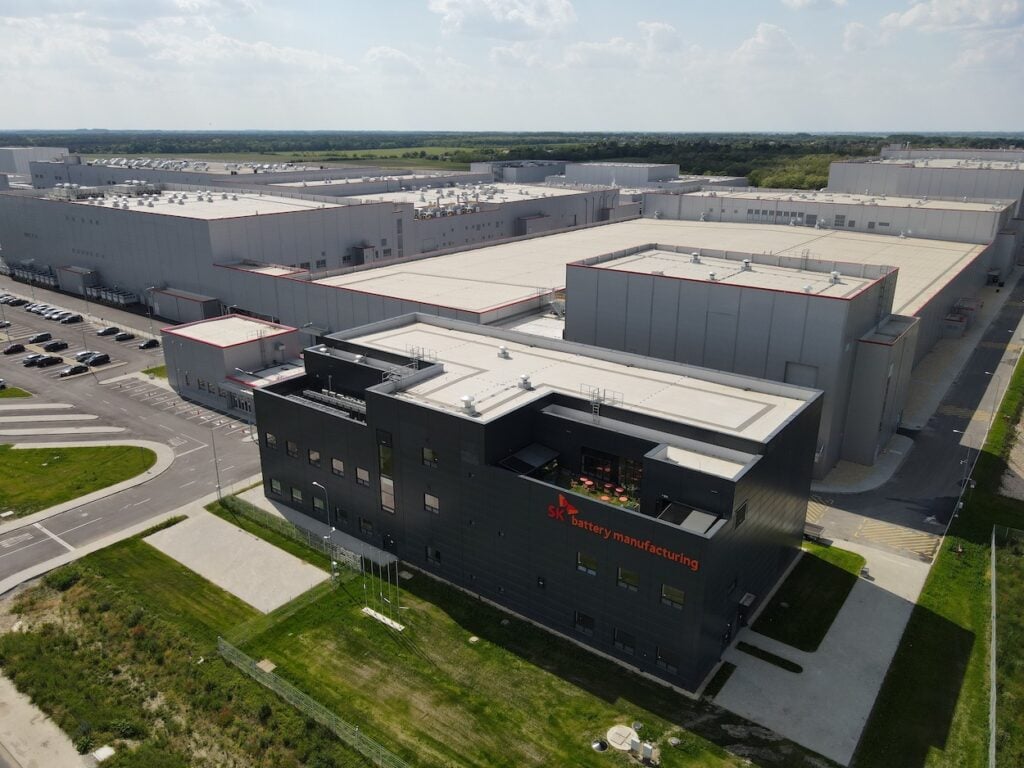
Ascend Elements will recycle manufacturing scrap from SK Innovation’s lithium battery gigafactories in Georgia, US, while chemicals company BASF has bought land in Canada for a cathode active materials factory and recycling plant.
Ascend Elements — formerly known as Battery Resourcers — announced this morning that it will recycle lithium-ion battery cell and module manufacturing scrap from the Korean maker’s production lines in Commerce Business Park.
Enjoy 12 months of exclusive analysis
- Regular insight and analysis of the industry’s biggest developments
- In-depth interviews with the industry’s leading figures
- Annual digital subscription to the PV Tech Power journal
- Discounts on Solar Media’s portfolio of events, in-person and virtual
Currently under construction, the battery company’s SK Battery Americas division is building more than 20GWh of annual production capacity at the two sites, investing a reported US$2.6 billion to get them up and running by the end of 2023.
As reported by Energy-Storage.news in January, Ascend Elements is building the largest single site lithium battery recycling plant in North America, in Covington, Georgia, close to the SK Innovation factories. Ascend claimed its recycling processes can recover 98% of battery materials and return them to the supply chain from the facility, which will open in August.
“People often think lithium-ion battery recycling is just for end-of-life batteries, but waste from the battery cell manufacturing process is the biggest segment of the battery recycling market right now,” Ascend Elements CEO Michael O’Kronley said.
“SKBA is embracing sustainability and reducing its impact on the environment by recycling every bit of scrap battery material it produces.”
The recycling company also touted that active cathode materials produced by its proprietary “Hydro-to-Cathode’ process was found to outperform new cathode materials, as referenced in a study published in scientific journal Joule.
Ascend further claimed the process could be 93% cleaner than mining and producing from raw materials, and at much lower cost.
While the initial focus is largely going to be on electric vehicle (EV) batteries, Ascend Elements told the site that it also wanted to process as much material from the stationary energy storage system (ESS) sector as it can. Materials produced from recycling will likely find their way into ESS projects too, through the company selling them back to cell manufacturers.
It is a similar story for the SK Innovation deal, an Ascend spokesperson told Energy-Storage.news.
“While we are recycling EV battery manufacturing scrap for SK Battery America, our innovative Hydro-to-Cathode recycling process works well with ESS batteries too,” the spokesperson commented.
“We are currently recycling ESS batteries for several organisations. Additionally, the customised cathode material that we produce from the Hydro-to-Cathode process can be used by battery manufacturers making ESS solutions.”
SK Innovation also has a partnership in place with energy storage system integrator and manufacturer IHI Terrasun which could see the maker’s battery cells used in IHI projects in the US starting this year.
‘US needs recycling policy’
Yesterday, at an event hosted online by Lawrence Berkeley National Laboratory (Berkeley Lab), US Department of Energy director of the vehicle technologies office David Howell said that “significant effort” must be put into developing recycling capabilities.
“The supply chain is more than gigafactories. You need to look at the entire supply chain from upstream material supply, refined materials all the way through battery component manufacturing, like cathode, anode to electrolytes, and key components like that — cell production, pack production,” Howell said.
“If we want to realise a sustainable ecosystem, we definitely need to put significant effort in recycling spent lithium batteries, getting those spent lithium batteries back into the supply chain. And those materials particularly represent a key domestic supply of materials going forward.”
Howell said he “could not stress enough,” the importance of recycling, especially for materials for which the US did not have access to adequate natural resources domestically.
“We really need a national recycling policy,” he said, highlighting that the DoE’s goal is to establish a recycling ecosystem that collects 90% of the spent lithium batteries. Efforts could begin with consumer electronics and be mapped to EVs and grid storage, Howell suggested.
BASF maps supply chain integration at Canada site
European chemicals company BASF is targeting having its cathode active materials (CAM) and recycling plant in Bécancour, Quebec, Canada up and running in 2025.
BASF already manufactures CAM in North America and said last week that it has signed agreements to secure land at a site between Montreal and Quebec City on the Saint Lawrence River for its expansion plan.
The selected site will allow it to use hydropower to help power operations and can be well-connected with the company’s global metal sourcing network, BASF claimed. Provisional plans are in place to add an intermediates base metal refinery for nickel and cobalt, as well as recycling facilities for all battery metals.
The site will have space to expand up to 100kt CAM production capacity per year, including supply of precursor cathode active materials (PCAM). Plans remain subject to necessary regulatory approvals, BASF said.
“With new investments in electric vehicles and supporting infrastructure being announced continuously in North America, we are pleased to pursue our own investment in the region,” BASF Catalysts division president Dr Peter Schuhmacher said.