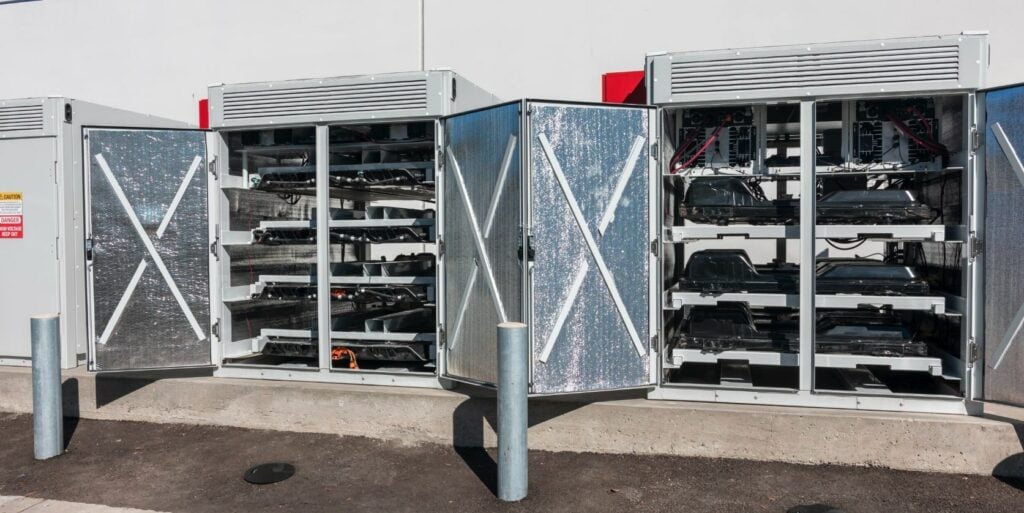
We caught up with Mike Ferry, president of California-based second life energy storage firm Smartville Inc.
Second life energy storage, the repurposing of EV batteries into stationary systems, has taken off this year. As readers of Energy-Storage.news’ coverage of the space will know, this year has seen several new companies appear and raise tens of millions of dollars, procurement deals with vehicle OEMs in the hundreds of MWh and even now GWh-scale, and even systems using multiple battery chemistries.
Enjoy 12 months of exclusive analysis
- Regular insight and analysis of the industry’s biggest developments
- In-depth interviews with the industry’s leading figures
- Annual digital subscription to the PV Tech Power journal
- Discounts on Solar Media’s portfolio of events, in-person and virtual
California-based Smartville is one of those looking to capitalise on the opportunity in North America, along with its main competitors Moment Energy, Element Energy and B2U. Ferry discussed the company’s product and value proposition, its existing and future deployments and plans, growing its manufacturing capacity and its project using Tesla batteries, reported on separately here.
Energy-Storage.news: Tell us about Smartville Inc, why it was founded and what you do today?
Mike Ferry: CEO Antoni Tong and I founded the company three years ago in San Diego, California. As researchers at the University of California, San Diego, our advanced energy storage lab received US$2 million grant from the US Department of Energy (DOE) through the ARPA-E programme. Our technology was really focused on how to safely and reliably repurpose used lithium-ion electric vehicle batteries for grid storage, and being able to both predict and extend their useful life.
We realised early on that the only way to grow a real market for this type of technology is to be able to absolutely warranty or guarantee the performance of these batteries in a repurposing application and a second life.
We validated our technology using battery modules obtained by disassembling EV battery packs, and we cycled modules of different chemistries from different automakers. As a result, we now have software and hardware that can use batteries of different states of health within the same system and we’re able to improve total system state of health over time, and then we’re able to warranty the performance of those batteries in that second life. At that point, we decided to shift from repurposing simple modules and to design our system to repurpose entire battery packs.
We believe focusing on battery packs rather than disassembly and modules allows us to scale. For this market to reach the MWh and even GWh projects it does not make sense from a labour or financial perspective to disassemble.
So what is your main physical product?
Our main product is an energy enclosure called MOAB, which can hold between six to 10 battery packs with a nominal rating of anywhere between 200-500kWh depending on the type of battery packs we’re using and the state of health of those battery packs.
We have a number of systems that I would characterise as laboratory type systems but our first system that is out in the field is one that we commissioned last month (at UC San Diego).
It has one enclosure with Tesla batteries, and the other enclosure contains Nissan LEAF battery packs. And then we operate those two MOAB enclosures as a single energy storage system, which provides energy services to the buildings that the system’s adjacent to.
So we consume solar power during the day, and discharge the battery after the sun goes down. And then we also provide backup power to critical facility loads within the warehouse that the batteries service.
What are the advantages and challenges of using entire battery packs instead of individual modules?
We see mostly advantages and not challenges. But the main challenge is that we have to be able to speak to each battery pack. Each battery pack speaks a slightly different language and has variation in how the battery management system is engineered.
So we need to speak to each battery pack and then have that all those battery packs roll up into our universal battery management system (BMS). We spent quite a bit of time developing that communication technology and that software.
And even within battery packs, different generations of battery packs will have slightly different communication and data protocols. And in speaking to battery packs, we’re not just able to tell the battery: “turn on turn off, open a contacter or close a contacter, charge discharge,” etc.
We’re also gathering critical data from each battery pack on cell voltages and on cell temperatures on internal resistance.
And we’re using all of that data, not just to control the battery pack – so that we can operate an energy storage system consisting of all different kinds of battery packs – but we’re also feeding all of that data into our database, so that we’re able to monitor the state of health of all those batteries and then feed that into our lifecycle modelling software.
We’re then able to predict how those batteries are going to perform over time. So not just in terms of their overall energy storage capacity, but in terms of their power-to-energy ratio, their efficiency, their internal resistance.
These are all elements that you need in order to make a real product out of these batteries. You need to understand exactly how the batteries are going to perform, and exactly how long they’re going to be able to perform at those different performance metrics.
And to what extent are the battery packs you use true ‘second life’ packs which have been in a vehicle out on the road, versus off-the-factory-floor, discarded, or test vehicle ones?
We’re working with automakers that want to see how battery packs throughout the different parts of their lifetime can operate in an energy storage system. Battery packs that are on the one end of the spectrum have completely gone through their useful life in a vehicle and might be at less than half of their original state of health, and the automakers want to see how those packs behave in an energy storage system.
We also have incorporated battery packs that are almost brand new. There are a large number of what I call ‘orphaned’ battery packs coming out of the salvage market. So you’ll have a vehicle that’s in an accident, where the front end and back end will be smashed and the insurance company will write off the whole car and sell the vehicle into the salvage market. But even though the vehicle is no longer useful, the battery, being tucked between the wheels and engineered to withstand collisions, is still very usable and undamaged.
So we’ve repurposed new battery packs and mixed them with old battery packs and shown how we can operate battery packs of different states of health within a single system.
Our technology allows us to be incredibly flexible in what type of batteries that we’re able to repurpose. And we think that is pretty critical for growing this market at this stage where the numbers of electric vehicles in the market and the number of batteries that are being produced is really starting to grow and build, and I think it’s hard to predict where the next big volumes of battery supplies are going to come from.
So let’s say an OEM whose battery packs you’ve never worked with before tells you they have 100 packs they want you to put into a system – how quickly could you incorporate that into your BMS and enclosure into a usable product?
If it uses standard CANbus data protocols we could incorporate it into our BMS in a few weeks. Fitting the battery packs into our physical enclosure would be in the order of a few months.
Did you work directly with Tesla and Nissan or through third-party sellers?
For Tesla we work through third parties, for Nissan and other automakers we work directly with them.
So Tesla is the exception – why is that?
Our experience in the US is that Tesla does not seem to be interested in working with outside partners. They’ve also publicly stated that they’re not focused on battery repurposing, not in their current business model at least, which I think might change over time. But that’s their public stance at the moment. We’re absolutely open to working directly with them but the opportunity hasn’t presented itself.
To what extent do you do your own manufacturing and system integration and how are you approaching UL 1974 certification, which competitor Moment Energy told us is needed to manufacture second life storage systems in the US?
We’re currently working with national testing laboratory Intertek to qualify our facility here in Carlsbad, San Diego, as a UL 1974 manufacturing facility. We see UL 1974 and UL 1973 as critical to certify in our system as well as another regulation called UL 9540. Our intention is to achieve those certifications by the first quarter of 2024.
We’re working with outside manufacturers at the moment but all of the final assembly and testing and commissioning will be done at our Carlsbad facility. In August we received US$2 million from the California Energy Commission (CEC) to ramp up that facility.
We’ll carry on working with a third-party manufacturer to build the physical enclosure and racking systems but that Carlsbad facility will be doing the assembly, putting together the batteries, power electronics, high voltage cabling, communications, thermal management systems and the final testing and commissioning.
It’s not currently a hard requirement for a system to be built in a UL 1974-certified facility. Our first operational system isn’t. A great deal depends on the local permitting agency that you’re working with which is responsible for ensuring the safety of individual installations, and most of their staff want to see certified equipment, which make sit far easier to permit on-the-ground projects.
But permitting agencies can permit individual projects without UL certifications if they feel that the project is safe and meets certain requirements. So in our first project we worked very closely with the permitting agency so that we could get the system installed and operational.
But that strategy is not something that is scalable, because you’re spending a lot of money and time to permit a single project. To achieve scale, you really need to have the certifications so that permitting agencies can easily permit your equipment and a construction project that utilises your equipment.
Give us an idea of the scale of your manufacturing capacity in the coming years?
For next year we’ll be fairly low scale. We’ll manufacture 20-30 of our 250kWh enclosures. By early 2024 we want to have a certified product and want to deploy 50-100MWh of product that year.
Do you have your own energy management system (EMS) platform and how big a focus is that for you?
We do have our own proprietary EMS platform that’s currently operating at our deployed system in here in San Diego, at another system operating in Irvine, and in all of the test systems working at our facility in Carlsbad. The interface between our master battery management software and EMS platform is really the focus for us, and moving forward we see this interface as one of our many long-term areas of competitiveness and value.
Tell us about how you’ll use the US$6 million you recently received from the DOE and second life projects you’ve got coming up?
Much of that money will be helping us to productise our enclosure system at a much faster pace than we could otherwise. We have operating prototypes but we’re iterating on our product and developing our second and even third versions. The money will also help us to certify our product to UL 9540 and our manufacturing facility to UL 1974.
Beyond our product, a significant portion of the funding is allocated to a large demonstration project which will be a 4MWh system in central California that will be co-located with an existing power plant. That will probably be deployed in 2024 as well and is in partnership with California’s largest privately-owned independent power producer (IPP).
At the end of Q2 next year we’ll be installing another prototype system with utility Southern Power to install one of our enclosures in Georgia. Additionally, we have several other early-stage projects in the pipeline for 2023, but our company’s primary focus is on certification, commercialisation, and scaling our ability to manufacture and deploy systems at large scales, which we really see ramping up in 2024.
Energy-Storage.news’ publisher Solar Media will host the 5th Energy Storage Summit USA, 28-29 March 2023 in Austin, Texas. Featuring a packed programme of panels, presentations and fireside chats from industry leaders focusing on accelerating the market for energy storage across the country. For more information, go to the website.