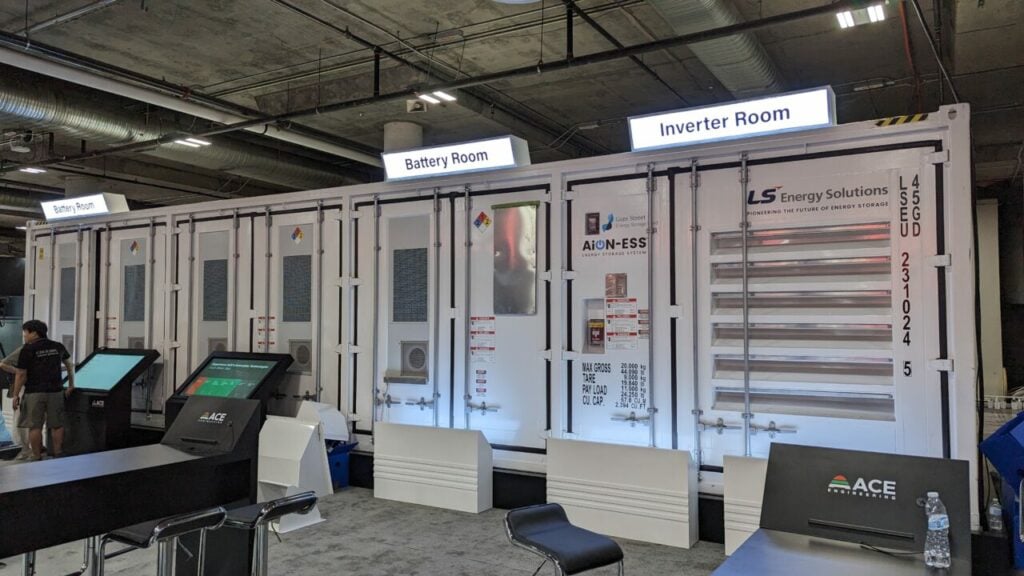
Battery storage system integrator LS Energy Solutions brought the first container, which will be deployed at a 200MW project in California, to this year’s RE+ 2023 trade show.
Housed in the basement of the Venetian Expo centre in Las Vegas, as the busy show went on overhead, many of the 40,000-plus people in attendance were likely unaware that a facility that is close to a real-life example of a grid-scale battery energy storage system (BESS) container was beneath their feet.
Enjoy 12 months of exclusive analysis
- Regular insight and analysis of the industry’s biggest developments
- In-depth interviews with the industry’s leading figures
- Annual digital subscription to the PV Tech Power journal
- Discounts on Solar Media’s portfolio of events, in-person and virtual
The only thing missing was the actual battery modules, for obvious reasons.
“For us, this is the largest project that we’ve done to date,” says Steve Fludder, LS Energy Solutions CEO, of the Big Rock project, on which it is partnering with UK-based BESS investor-developer Gore Street Energy Storage Fund and developer Avantus, formerly 8minute Solar Energy, from which Gore Street bought the project.
From its temporary home in Nevada, the LS Energy Solutions container was heading on to the project site, in California’s Imperial Valley, where it will be one of 137 units adding up to 400MWh of energy storage capacity.
Each unit of LS’ all-in-one solutions, AiON-ESS, will be of 1.5MW output and 3.5MWh capacity, including integrated DC and AC components. Key to that, and key to the whole project’s technology, is LS Energy Solutions’ modular 140 kVA string inverter AiON-SIS.
Complete system integration
“We’ve done over a gigawatt worth of projects over the years. Many of those projects, we provided only the inverter component,” Fludder says.
“And two and a half years ago, we pivoted our strategy to in addition to still selling inverters, we decided to basically do the complete system.”
Having only delivered its first system in 2022, a 14.6MW/13.7MWh project in New Jersey for the PJM market, Big Rock is a big scale-up for the company in terms of sizing and duration, as well as being Gore Street’s first California project and the biggest US project so far for the investor, which has been prolific in the UK market and embarked on an internationalisation strategy, also last year.
The relationships involved go back several years, according to Fludder, who worked with Gore Street on a number of projects in the UK in his previous corporate position as CEO of NEC Energy Solutions, as well as with 8minute in the US.
But the story of the technology goes back much, much further and is perhaps an interesting illustration of how the BESS industry has evolved.
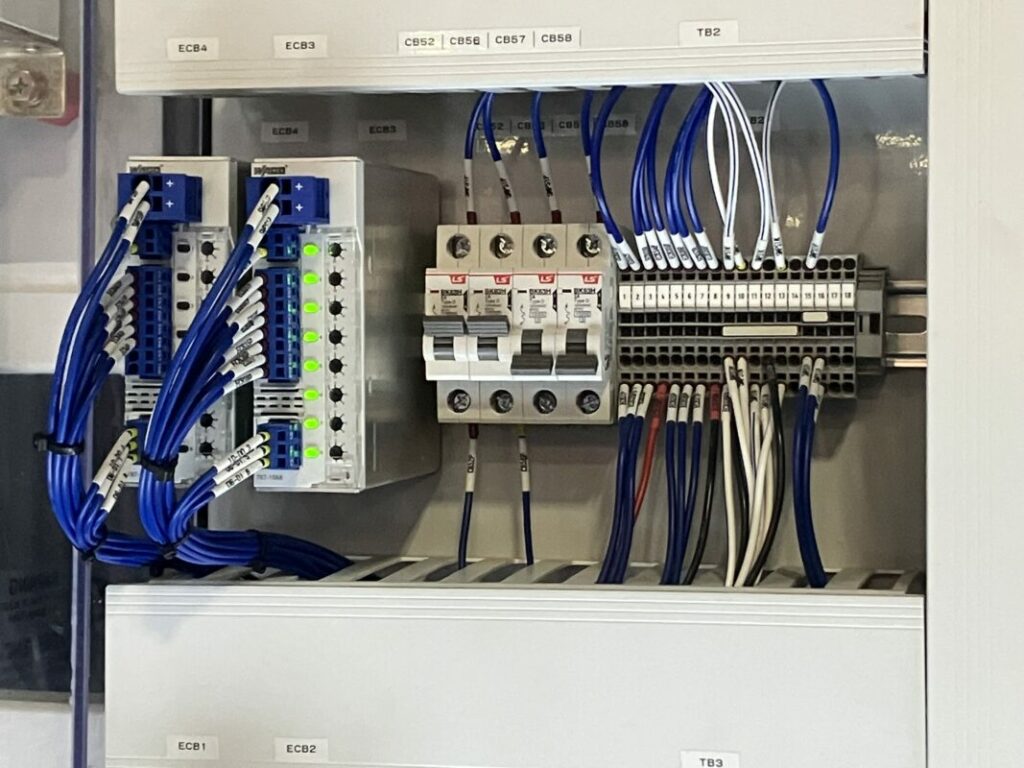
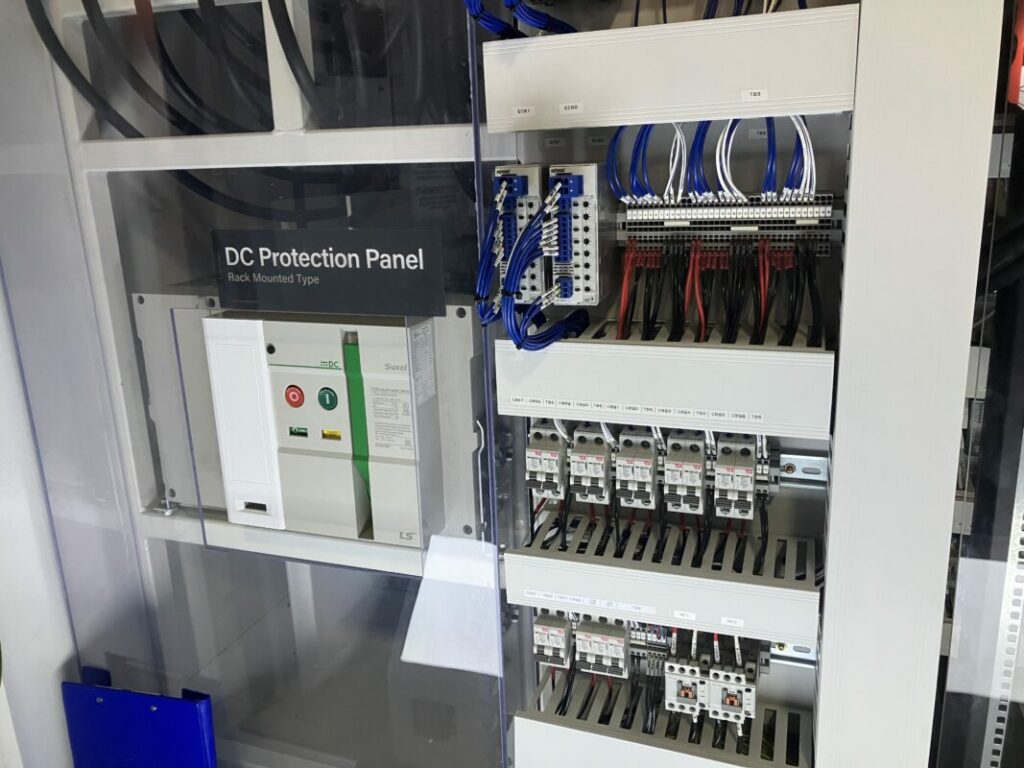
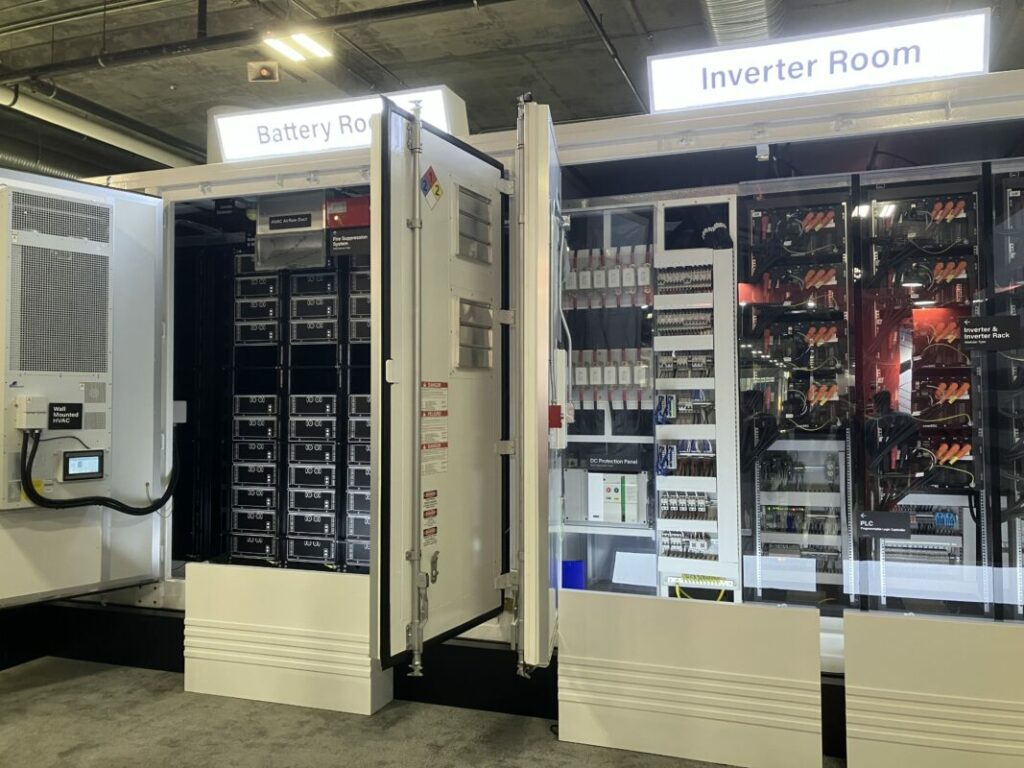
Inverter evolution
LS Energy Solutions was formed by the acquisition of the grid-tied division of Parker-Hannifin by Korea’s LS Group in 2018. Back in 2008 – then known as A123 Solutions, prior to its acquisition by NEC – Fludder’s former company worked with Parker-Hannifin on the first grid-connected lithium-ion project in the US, in West Virginia.
“From then until today, including post-acquisition by LS, we’ve stalled over 1,000MW of projects, many of which we only supplied with the power conversion system (PCS) or the inverter.”
From there, the new product offerings integrate power conversion and batteries into one unit, creating what Fludder describes as an AC battery.
Enclosures are being made by ACE Engineering, another Korean company that is also working with rival system integrator Powin Energy on its Waratah Super Battery in Australia. Meanwhile, inverters are coming from a contract manufacturer based in Alabama, although LS was not yet able to reveal the name due to commercial confidentiality.
“We historically have manufactured them ourselves in our facility in Charlotte, North Carolina, but now we’re getting to volumes where we need somebody with the ability to manufacture thousands of units per year.”
Despite it being a third-party manufacturer, however, Fludder says quality control will be as tight as it would be for components made by the company itself, repeating a theme we often heard at the 2022 edition of the RE+ show: PCS comprises perhaps a small proportion of the cost of energy storage systems, but represents one of their most vital components.
Standalone inverters, connected in parallel
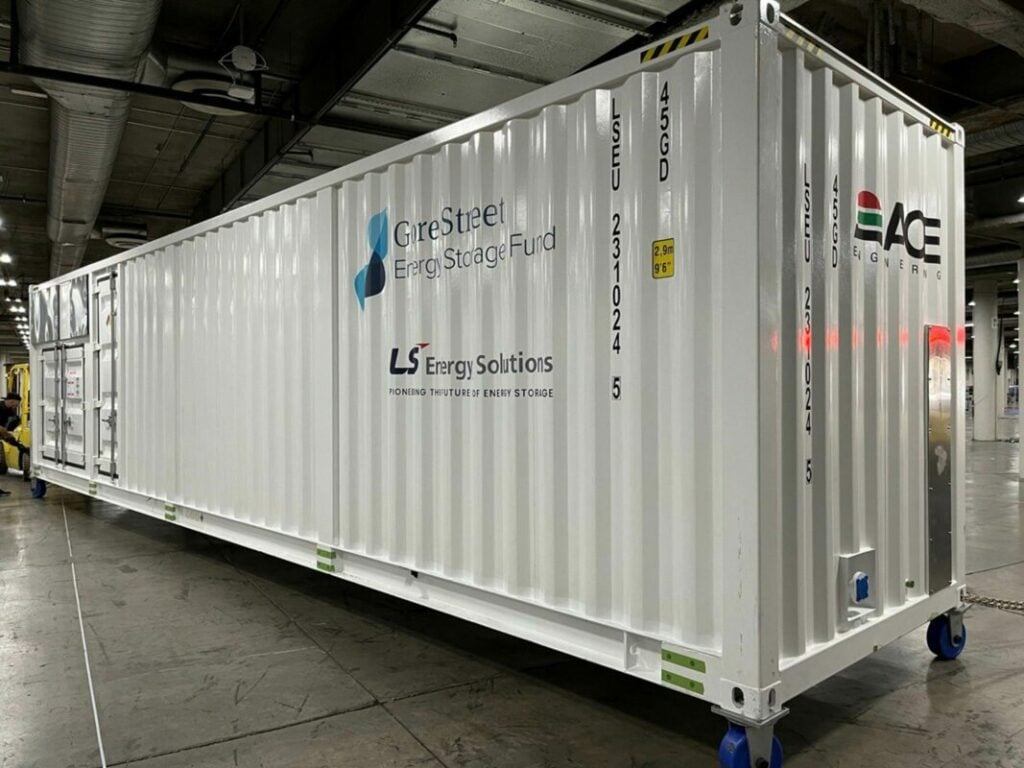
The cost of PCS failure in a BESS can be high, especially with average project sizes continuing to go up, both from a financial perspective, and in terms of time lost working onsite to repair or replace.
For LS Energy Solutions, leaning on its longstanding track record of PCS development meant that it was able to create a BESS product that “takes the risk into the factory,” Fludder explains.
“From my experience, anytime a project schedule got extended out, or the cost of the project delivery increased, it was always the site work that got a project financially and schedule wise sideways. The problem in successfully delivering a project on time, within budget, mainly the risk is in this this area,” Fludder says.
“So we’re taking that into the factory, as opposed to doing it at the project site because in the factory and doing all that work is exactly the same no matter what project we’re delivering the product to. Inside that unit, we are using our own inverters. Each one of these inverters is a standalone PCS and you can connect them in parallel.
“If one of those inverters has some issue that trips it offline, the rest of them keep running. So when there is a failure, a very small amount of power is lost.”
The all-in-one approach, as the name implies, also puts other components like thermal management and safety features into the same box, representing what Fludder calls a “rather dramatic shift” in the bespoke work that is typically done at the project site.
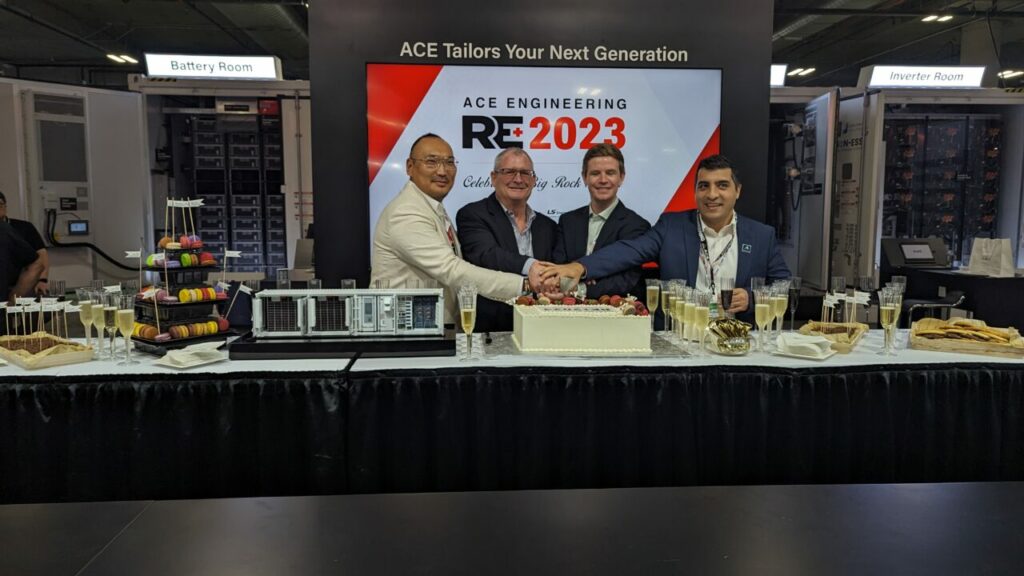
“When all these different components show up from different suppliers at the project site. And then they effectively have to be not only installed, which entails a lot of civil work, and electrical contractors to connect them all. But it also it takes time, it takes money,” he says.
“We’re moving that from the project site into a controlled factory environment, and we test [the systems].”
The battery supplier to Big Rock will be Samsung SDI, using its nickel manganese cobalt (NMC) cells. Although LS Energy Solutions’ current and contracted projects are based on NMC technology, the technology provider has a roadmap in place for changing over to lithium iron phosphate (LFP) cells in the next generation of its all-in-one BESS.
Again, LS’ chosen partner on that LFP supply arrangement can’t yet be disclosed, but Fludder confirms that it will be producing batteries in the US, with “more than enough US domestic content to qualify for any of the incentives that are currently on the table,” Fludder claims.
Read our recent two-part Guest Blog from LS Energy Solutions’ director of strategy and market analytics, Ravi Manghani, ‘An energy storage system integrator’s perspective on the Inflation Reduction Act’, which includes insights into topics like the competitiveness of US-made battery cells here (part one) and here (part two).