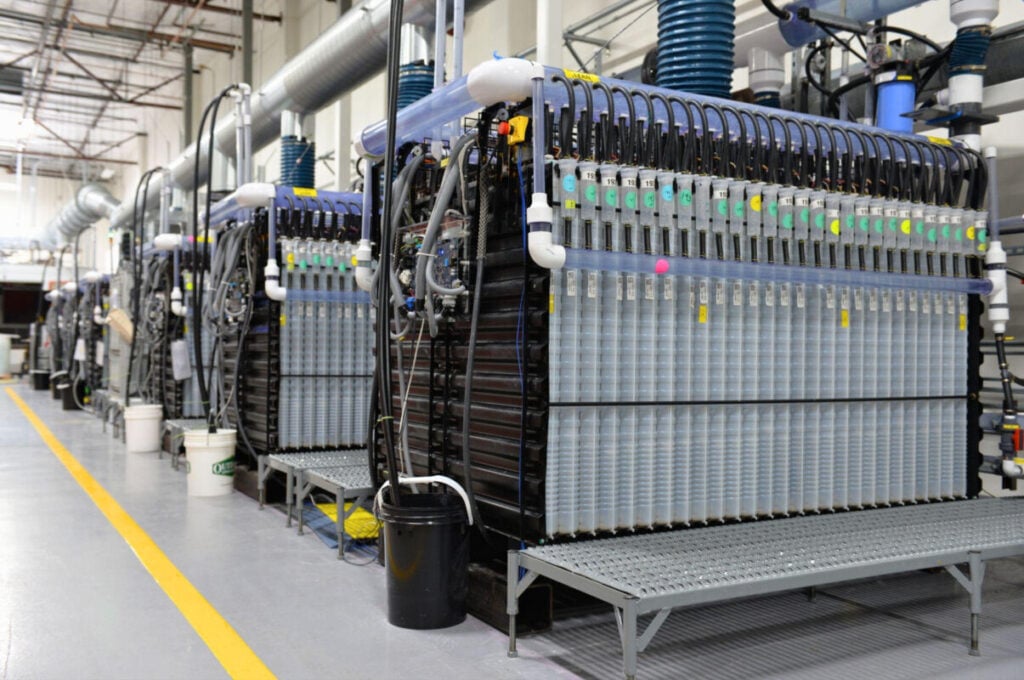
Lithium-ion battery storage system integrator Fluence and iron-air battery startup Form Energy have completed fire safety and explosion testing of energy storage technologies.
Fluence’s GridStack Pro 2000 battery storage solution has undergone ‘rigorous’ safety testing, including a large-scale fire test, while Form Energy’s iron-air has completed UL9540A thermal runaway testing at the cell level.
Enjoy 12 months of exclusive analysis
- Regular insight and analysis of the industry’s biggest developments
- In-depth interviews with the industry’s leading figures
- Annual digital subscription to the PV Tech Power journal
- Discounts on Solar Media’s portfolio of events, in-person and virtual
The two US-headquartered companies announced the outcome of tests toward the end of last week, each claiming the results achieved through third-party tests validate their technological approaches.
Fluence: Dispersion, deflagration and large-scale fire testing
Energy storage system integrator and services provider Fluence said on Thursday (12 December) that its GridStack Pro 2000 battery energy storage system (BESS) units are the first products that meet US domestic content requirements to ‘exceed top safety standards’ in the industry.
The technology provider recently began producing its own battery modules out of a factory in Utah, US, paired with battery cells also manufactured in the US, by AESC. The module itself recently completed certification to the UL1973 safety standard for batteries used in stationary applications.
GridStack Pro underwent deflagration testing conducted by the company with experts at DNV, while Fluence carried out large-scale fire testing alongside UL9540A tests with CSA Group.
The deflagration and dispersion tests aimed to assess the explosion mitigation features of GridStack Pro, in other words, how the unit responds to the buildup of gases and how well equipment, such as deflagration vents, deals with the gases’ ignition.
Fluence said the results of tests carried out at DNV’s testing centre in northern England, UK, validate the unit’s deflagration vents in prevention of explosions.
GridStack Pro met the requirements of the standards NFPA 68 Standard on Explosion Prevention by Deflagration Venting and the more all-encompassing NFPA 855 Standard for the Installation of Energy Storage Systems. Both are from the National Fire Protection Association (NFPA), which is a US-based organisation, but its codes and standards are often either widely adopted or used as best practice benchmarks internationally.
LSFT to be included in forthcoming industry-wide standard
Meanwhile, the large-scale fire test GridStack Pro underwent saw the complete unit set on fire at a CSA Group facility in North Carolina, US. CSA Group experts set the fire under controlled conditions and the unit burns without fire suppression systems or external firefighting equipment applied.
The test condition has been designed by CSA Group as a comprehensive means of assessing how BESS equipment responds in worst-case-scenario fire situations. Currently, the industry standard is only for the UL9540A test to be carried out, which sees individual cells put into thermal runaway and the propensity for heat and flames to propagate to neighbouring equipment assessed.
The forthcoming 2026 edition of NFPA 855 will include large-scale fire testing (LSFT) requirements. LSFT was the subject of a recent Energy-Storage.news webinar sponsored by CSA Group.
CSA Group compliance and technical expert Michael Becker discussed how the tests are carried out and how the group’s new LSFT procedure, CSA TS-800:24, is designed to be in line with principles of the expected requirements in NFPA 855.
Also taking part in that webinar was Chris Groves, product manager for safety at Wärtsilä Energy Storage & Optimisation (Wärtsilä ES&O).
Rival system integrators Wärtsilä ES&O, Fluence and Sungrow have conducted recent large-scale fire testing on their systems. Wärtsilä announced the results of its tests carried out under CSA Group’s procedure in early November. Sungrow announced two tests in China this year: the first on 10MWh of storage capacity across two containerised units in June, before another test, this time on 20MWh split across four BESS containers, again in early November.
UL9540A testing for ‘multi-day battery’ went beyond standard Li-ion approach
Meanwhile, Form Energy has become the latest non-lithium battery storage technology provider to put its equipment through the paces of UL9540A testing.
The company has developed a novel iron-air battery, which charges and discharges based on oxidisation (rusting) and de-oxidisation of iron in the cathode. Form Energy claims that this enables many hours, even multiple days, of cost-effective energy storage, using abundant raw materials that can be sourced almost anywhere.
The battery underwent UL9540A testing recently, including how it responded to multiple short-circuit failure modes in charging and discharging. With Form Energy claiming the device to be suitable for multi-day long-duration energy storage (LDES) projects of about 100-hours as a sweet spot, the tests also assessed how it reacted to seven days of overcharging, and other ‘extreme scenarios’.
Form Energy CTO and co-founder William Woodford said it was important that the UL9540A testing “went beyond standard lithium-ion protocols to evaluate potential failure modes,” given the novelty of the technology.
The company said that consistent results were observed across all different scenarios tested, with the battery not experiencing uncontrolled heating or thermal runaway, dendrite formation or fires.
While UL9540A is not a pass/fail test as such, the results are considered significant in informing customer choices around battery and storage system procurement.
“The UL9540A cell-level test is the baseline for a battery’s safety profile. Battery chemistries that demonstrate no thermal runaway at the cell-level represent a significant determination of inherent safety under extreme abuse conditions and eliminate the need for additional testing at the module or system level,” explained Matthew Paiss, a fire expert and technical advisor for battery materials and systems at Pacific Northwest National Laboratory (PNNL), one of the US Department of Energy’s network of National Laboratories.
The first of several pilot projects of the Form Energy iron-air battery with US utilities is just getting underway and the company is currently building its first factory in West Virginia. Form Energy closed a US$405 million funding round in October.