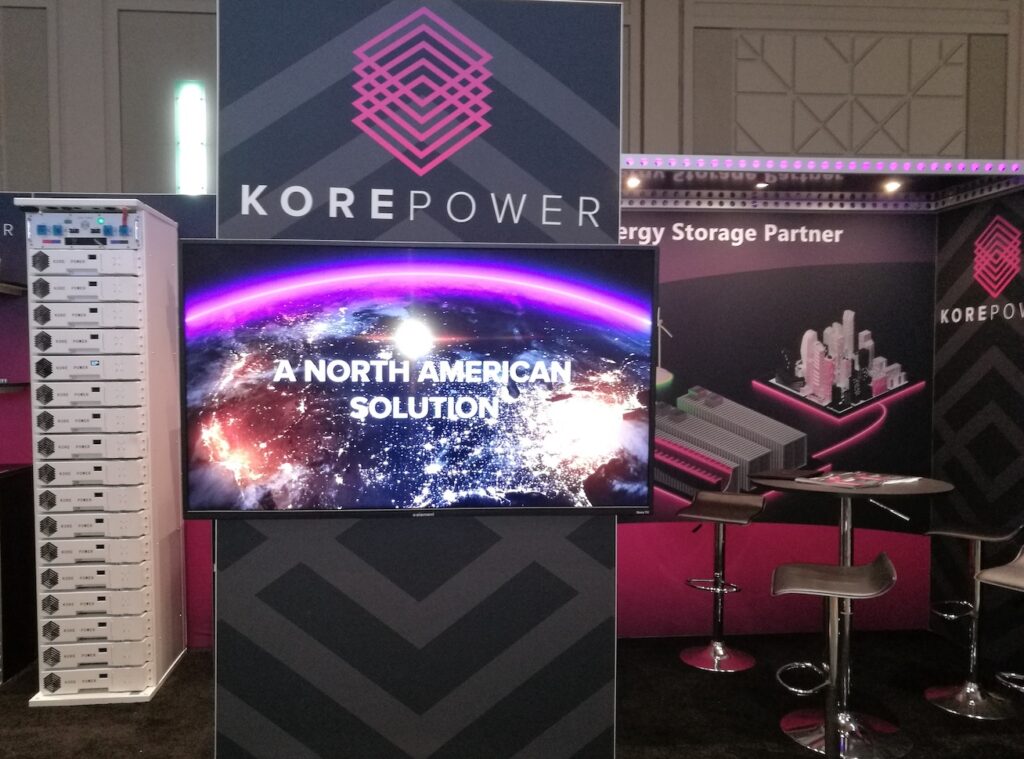
Cost and availability of raw materials is the biggest among a number of challenges that must be addressed if US-made products will be able to meet demand for battery storage in the country.
That’s according to the Solar Energy Industries Association (SEIA), which has produced a new report explaining how the US manufacturing value chain can overcome those challenges. Unchecked, the potential barriers will mean that the domestic lithium-ion (Li-ion) battery industry will fall far short of serving the needs of a market projected to grow to 119GWh annual demand by 2030, SEIA warned.
Enjoy 12 months of exclusive analysis
- Regular insight and analysis of the industry’s biggest developments
- In-depth interviews with the industry’s leading figures
- Annual digital subscription to the PV Tech Power journal
- Discounts on Solar Media’s portfolio of events, in-person and virtual
“America’s ability to lead the global clean energy transition and boost grid reliability depends on how quickly we scale domestic production and deploy battery storage technology,” Abigail Ross Hopper, CEO of the national trade association said.
The new white paper, ‘Energizing American battery storage manufacturing,’ “illustrates the competitive landscape of energy storage manufacturing and articulates the challenges the US must address,” to reduce the county’s reliance on battery imports and enhance its energy security, Hopper said.
This is despite government policy support for domestic manufacturing, seen most prominently in measures to incentivise both demand for, and supply of, batteries made in the US resulting from the Bipartisan Infrastructure Law and Inflation Reduction Act.
Somewhere in the region of US$300 billion investments in clean energy have been announced in the US since the IRA passed into law a year and a significant portion of that has gone towards battery gigafactories – an area in which the US has now overtaken Europe to the extent that the European Union (EU) is moving to introduce its own equivalent, the Net Zero Industry Act, on which negotiations are set to begin between EU member states.
Of course, the major ‘competitor’ for both is China, which is home to around 90% of the global Li-ion manufacturing industry and owns nearly all the materials processing value chain.
Today, there is only about 60GWh of annual Li-ion production capacity in the US, which is nowhere near enough to have served the roughly 670GWh of demand for electric vehicle (EV) batteries and 18GWh of battery energy storage system (BESS) demand that was recorded in 2022.
By 2030, SEIA said, EV battery demand could rise to as much as 4,000GWh and BESS battery demand to 119GWh.
New factories are forecasted to increase annual domestic production capacity to about 630GWh within the next five years, and Free-Trade Agreement (FTA) countries will add about 810GWh for a total of 1,400GWh of supply to the US.
However, not all of those forecasted new facilities are guaranteed to materialise, and perhaps more importantly, EVs will remain the main target market for battery makers. Around 90% of new announced capacity will be dedicated to vehicles and the remaining 10% will be split between BESS and other applications, although SEIA noted that some EV battery makers have yet to specify whether they will also produce cells to meet demand from the stationary storage market.
Graphite supply ‘a potential chokepoint’
While finding US or FTA-sourced lithium and phosphorous should not be too difficult by 2030, the US market will still need to compete with other countries for supply, with China the most common destination for lithium from FTA countries.
However, graphite, one of the other main raw materials, will be a different story and represents a “potential chokepoint”. Without any current natural graphite production sites existing in the US, and 60% of graphite mined in the past five years coming out of China, the US will likely depend on sourcing it from Canada or Australia. Yet neither of these countries will be capable of producing on the scale needed to meet demand from the US, according to SEIA’s report.
Production yields
Elsewhere, the head start of China and other battery producing countries like South Korea or Japan may also count against the US, at least in the short term.
New entrants to the industry are only typically able to achieve production yields at about 50%, whereas for more established players, the figure is closer to 90% and for Chinese cell producers, it is closer to 98%.
Raising production yields will be vital to the cost-competitiveness of US-made batteries, and SEIA recommended that partnerships with established players will be needed to overcome this barrier.
Other challenges include the need to hire or train up large numbers of workers, which again, will most likely require collaboration with more experienced foreign partners.
IRA incentives to reduce cost of US production by 40%
The policy support from the government, particularly via the IRA, will have a positive impact on US cost-competitiveness, with SEIA predicting IRA measures to reduce the cost of domestic production by more than 40%.
SEIA said that state-level policy can also make a difference, noting that different types of incentives like tax breaks, workforce development support and support for siting and permitting factories provide “critical early-stage support for the supply chain buildout from mining and refining to factories and R&D activities”.
“Smart and strategic investments across the supply chain are needed because building a domestic energy storage base is a strategic imperative for US energy security,” SEIA chief Hopper said.
Read the SEIA report, ‘Energizing American battery storage manufacturing’, here (PDF).