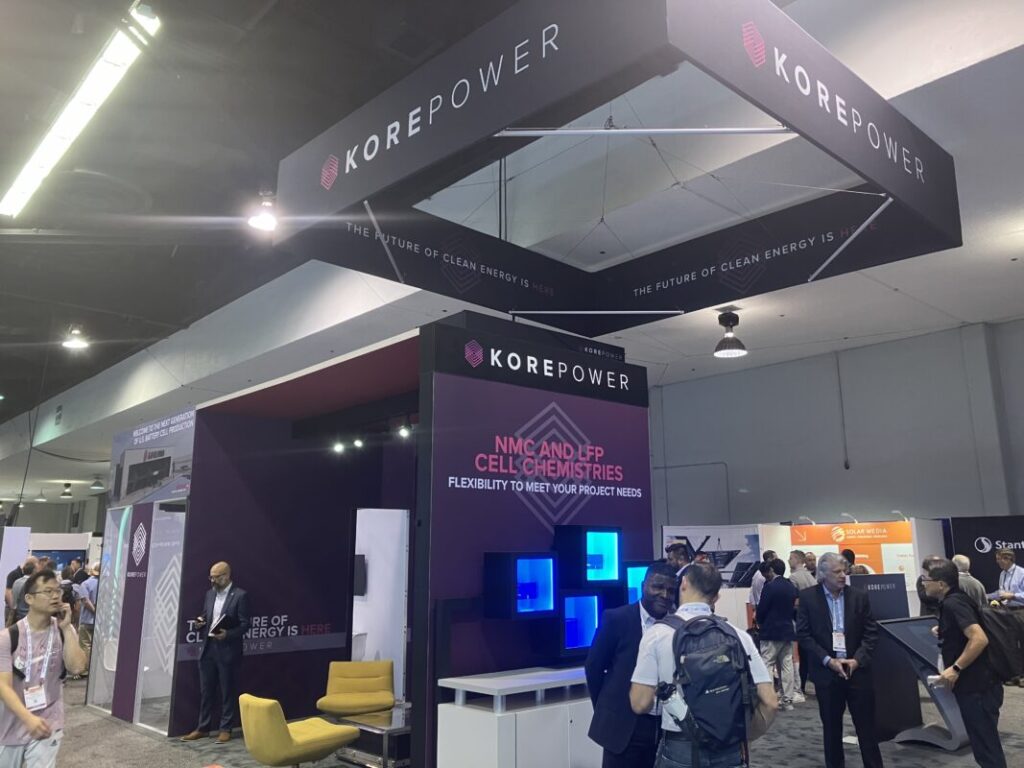
KORE Power CEO Lindsay Gorrill speaks with ESN Premium about the US startup’s manufacturing plans, why NMC won’t go away anytime soon, and where he thinks the BESS market is going.
Back in 2018, KORE Power attracted attention to its exhibition stand at what is now the RE+ trade show (then known as Solar Power International and Energy Storage International).
Enjoy 12 months of exclusive analysis
- Regular insight and analysis of the industry’s biggest developments
- In-depth interviews with the industry’s leading figures
- Annual digital subscription to the PV Tech Power journal
- Discounts on Solar Media’s portfolio of events, in-person and virtual
Despite being a little tucked away and quite small, the booth prominently displayed messages to the effect that here was a US-headquartered manufacturer of battery cells aimed at the stationary battery energy storage system (BESS) market.
The desire for domestic manufacturing of everything from cells to enclosures and complete systems is a hot topic in the US today, but six years ago, it sounded to many like an aspirational goal somewhere in the far distance.
As with the solar PV industry, supply chains for battery storage were nearly all overseas and based in or owned by China and Chinese companies.
“Way back then, in 2018, we saw a need for some manufacturing in the United States before the pandemic, and then in the pandemic, everybody else saw what the issues are,” Gorrill, who founded KORE Power after a background of working in battery supply chains in the US and China, says.
KORE Power is inching towards the start of construction at its factory, the KORE Plex, in Buckeye, Arizona, as regular readers of the site will know.
While Gorrill has in the past passionately stated that the battery cell is the fundamental building block of the energy transition, including during a mid-pandemic online roundtable chaired by US Secretary of Energy Jennifer Granholm, his company is vertically integrating the design, integration, and production of BESS technology through cells, modules, racks, enclosures, and systems.
‘Full production’ at KORE Plex Phase 1 by end of 2026
Speaking with ESN Premium at the 2024 edition of RE+ in California last month, Gorrill says that proving out those products, starting with cells, is central KORE’s go-to-market strategy: making batteries at scale is difficult, but without customers to sell them to, making any money out of them is nigh-on impossible, he says.
“The idea was to get product in the market early, to prove the product that we’re going to produce out of the KORE Plex. We’ve been doing that for the last four, almost five years now, so we have a lot of contract interest in supply out of the KORE Plex.”
So, while KORE’s nickel manganese cobalt (NMC) and lithium iron phosphate (LFP) cells, its KORE Mark One module and containerised systems are produced by partner factories in China today, they are identical to what will be produced domestically in a couple of years out of Buckeye, he claims.
With “quite a bit of money spent” already on the KORE Plex, and conditional loan commitment from the US Department of Energy’s Loan Programs Office for up to US$850 million towards it pledged in mid-2023, Gorrill says construction will be ready to begin once the last pieces of financing are in place.
“If it goes according to plan, we’ll start producing modules at the end of 2025 and cells end of 2026, so we’ll be in full production by the end of 2026 on Phase 1, which is 7GWh of [annual production] capacity, 2GWh NMC and 5GWh LFP.”
NMC still has its place
To the casual observer, it might have seemed that LFP has almost completely replaced NMC as the battery chemistry of choice for stationary energy storage system (ESS) applications for the last couple of years.
It was an interesting debate for a while around the different chemistries’ strengths and weaknesses: NMC being more energy-dense, LFP having a higher tolerance to mechanical abuse and temperature range, NMC being more commonly used in electric vehicles (EVs), LFP being cheaper for stationary applications, and so on.
“LFP kind of came to the market at the right time when NMC was having problems with some of the thermal runaways that were going on [in the industry],” Gorrill says.
Yet the perception that LFP is inherently safe and NMC is not is a false one, he argues, with some recent thermal events at LFP systems showing LFP is only a safer chemistry if the system around it is safe.
KORE Power supplies to the EV market as well as ESS, and Gorrill says some EV customers still want NMC batteries, while ESS customers that need high C-rates, for example, will also choose NMC. KORE Power’s DC block comes with either option.
“When we first talked about the KORE Plex years ago, it was pretty well all NMC. That was the original plan, and then obviously that progressed based on what the market demands,” Gorrill says.
“A customer came in the door [recently], talking LFP. They left with an NMC product. We sat down with them, and they said, ‘these are the things we want to use the battery for.’ We said, we can provide the LFP if you want, but we think our NMC product [fits] better and went through the economics of all that, and they went with the NMC.
“The interesting thing about being both a battery and solution provider and having both technologies is that we can talk to the customer and find out what it is they’re actually wanting to do. A lot of BESS developers know what they want to do, but they don’t know which the best way is to go; and some take the LFP, and some take the NMC.”
US can’t do it all alone, but it needs to put infrastructure in place
Zooming back out to the bigger picture, and what Lindsay Gorrill has long described as the motivation for KORE Power’s existence is, of course, in alignment with US government goals on fostering a homegrown battery value chain.
We’ve heard about the challenges inherent in going from zero when it comes to cell production, notably and most recently from Andy Tang at Wärtsilä ES&O, and how Fluence and Saft representatives feel their respective companies have made a strong start in the battery storage space for making and assembling modules, rack and containers—if not cells—in the US.
But with KORE Power currently sourcing cells from its Chinese factory, and despite tariffs on Chinese imported batteries set to go up from 7.5% to 25% in 2026 and Inflation Reduction Act incentives for using domestic content, it seems likely that demand for imports will continue to outstrip what’s available from sources in North America even after the KORE Plex is up and running by the end of 2026.
Gorrill agrees, and notes that while there’s a lull in EV demand at present leading to better availability of cells for stationary applications than say, mid-pandemic, EVs will come back, and new low-cost EVs could fuel increasing demand thereafter.
“I don’t think that by the end of 2026 or even 2027 that all the production is in the United States by then,” Gorrill says.
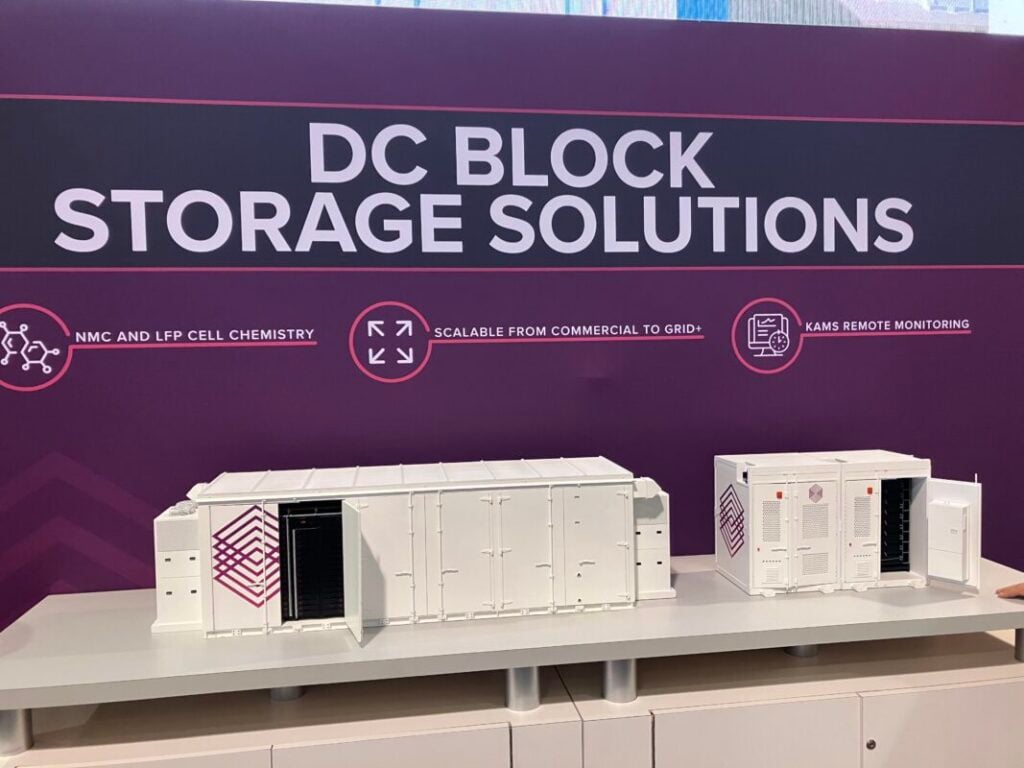
“You’re still going to have Chinese batteries coming in the United States; there has to be because you can’t build the capacity that quickly.”
Nonetheless, he says, “infrastructure has to be built in the US, manufacturing has to happen in the US,” creating a full ecosystem for making batteries.
For example, two publicly-announced partnerships KORE Power is in are with NOVONIX for the supply of synthetic graphite anodes, and with ENTEK, which makes lithium separators, both manufactured out of US facilities. That’s in addition to as-yet-undisclosed partnerships on other components like electrolytes and cathodes.
“Having a US cell manufacturer is important, because in reality, a non-US cell manufacturer doesn’t really care if you develop supply chain in North America, they have no interest,” the CEO says.
“For someone who’s doing an anode or cathode or whatever they’re doing, to get to market quicker, they have to be able to test it with a commercial cell, which is us (KORE Power).
“Even before the Bipartisan Infrastructure Law or the Inflation Reduction Act (IRA), I was already focused on figuring out how to get manufacturing into the United States, or the electrification [of the grid and transport] will never be sustainable. It’s a lot [of work], it’s a long time to get there, but you can get there, and at the end of day, you can have an amazing, huge, sustainable manufacturing base in the United States.”
The lost ‘D’ of the energy transition
Finally, the conversation moves to the downstream end of the industry and Gorrill’s take on the direction of the BESS market.
A few years ago, you would often hear about the fabled ‘Three Ds’ of the energy transition: decarbonisation, digitisation and decentralisation.
These days, the place of decarbonisation and digitisation are well-established at the heart of the energy storage industry. Conversely, in the world’s major BESS markets, projects are getting bigger and bigger, with hundreds of megawatt-hours and even gigawatt-hour scale facilities announced on a near-weekly basis in leading markets like California or Australia.
Gorrill says that he expects to see much more growth in commercial and industrial (C&I), distributed front-of-meter (think smaller-scale utility projects) and even residential batteries in the US in the coming years.
“We think that’s where it’s going: you’re not going to have these monster 1GWh or 2GWh projects. Say you build a 3GWh project in California; that’s a single point of failure. If you take that massive project and you distribute it into ten different projects, in different spots [on the grid], of 100MWh each, you’ve got 10 points of failure. So if something goes wrong, it shouldn’t go wrong in all ten at one time,” Gorrill says, adding that he thinks the decarbonisation goals of large corporates and manufacturing industries will further require a decentralised electricity distribution system.