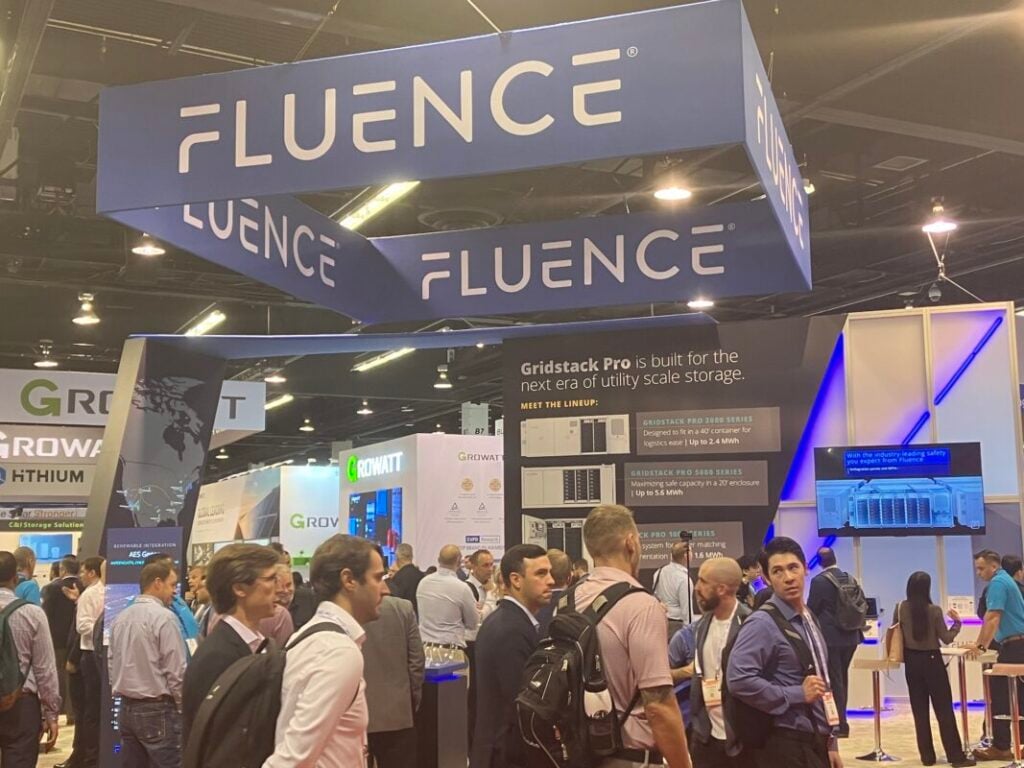
Global energy storage players Fluence and Saft speak to ESN Premium about moves to onshore production for the US market.
“We saw, even going back three or four years, that there was so much concentration of materials coming out of Asia that when we went into the pandemic, there were times when we saw the cost of transportation exceeding the cost of the goods,” says John Zahurancik, Americas president for Fluence.
Enjoy 12 months of exclusive analysis
- Regular insight and analysis of the industry’s biggest developments
- In-depth interviews with the industry’s leading figures
- Annual digital subscription to the PV Tech Power journal
- Discounts on Solar Media’s portfolio of events, in-person and virtual
Battery energy storage system (BESS) integrator and technology provider Fluence announced last week that it started producing battery modules for its grid-scale solutions at a factory in Utah, as reported by Energy-Storage.news.
It will also be among the few to be able to source cells for its modules from a factory in the US, which Zahurancik confirms in an interview at the RE+ event in California last week is the facility in Tennessee owned and operated by Envision AESC.
While that means its products will qualify for domestic content adders to tax credit incentives unlocked by the Biden-Harris administration’s pro-manufacturing policies, onshoring to the US has always been the goal.
Delivering projects during the COVID-19 pandemic wasn’t just costly in financial terms; it also meant long delays. Sometimes products would make it to the US and remain held up in ports a few hundred miles from their destination for weeks.
This was a major issue in an industry dependent on getting projects up and running according to strict timelines. Zahurancik says it will only become more acute as the industry rapidly grows.
“We started to see we need to diversify from just having a few places in the world where we can get these goods, and that started us down the path of US integration,” he says.
“We do a lot of our work in Vietnam and ship things around the world, but we opened a facility in Utah a few years ago, where we started to do some of the systems integration there.”
From there, Fluence wanted “more control over the unit,” and module production was the logical next step.
It means customers can buy a solution made by a company specialised in hardware and software aimed at the BESS space, rather than adapted from other applications.
Onshore advantages go beyond politics
“Even ahead of the inflation Reduction Act, we were working with several players to say: ‘We like the players we work with that produce in China, Korea and other places in the world, but we’re seeing a need to have some production in Europe, some production in the United States.’ Those are big regional hubs, and big markets overall,” Zahurancik says.
“It made sense to us that you did not necessarily need to have all of the production coming in those places, but having some ability to load balance across different regional production schemes and balance out when you run into these [challenges], whether it’s terrorism stopping ships from going through certain areas of the world, or weather disruption, or the Ukrainian war, these are all things that have had big impacts on time and cost that ultimately goes through to the customer.”
The motivation for France-headquartered Saft, owned by TotalEnergies, was similar, although the circumstances behind its ability to act relatively early are different.
Saft’s factory in Jacksonville, Florida, started making products to serve the BESS market in 2011. It made everything from cells to enclosures and complete systems until 2018.
However, says Vincent Le Quintrec, Saft sales & marketing director, it had moved too early and six years ago production at Jacksonville pivoted away from BESS and into other speciality battery market segments.
“Unfortunately, we were really pioneers on that, but the market was not ready, and we were not competitive with China,” Le Quintrec says.
Saft’s US market participation continued but with products made and shipped from its factory in Zhuhai, China.
At last year’s RE+, Saft director of innovation Michael Lippert told this site the company was refocusing on the US market as a key pillar of its global strategy. It had in fact been one of the first global players to deploy in the US, with a grid-tied project in Alaska commissioned in 2003, but had since seen more growth in other markets.
At this year’s show, Lippert says the picture has changed, and Saft has 2GWh of US projects in operation or in construction.
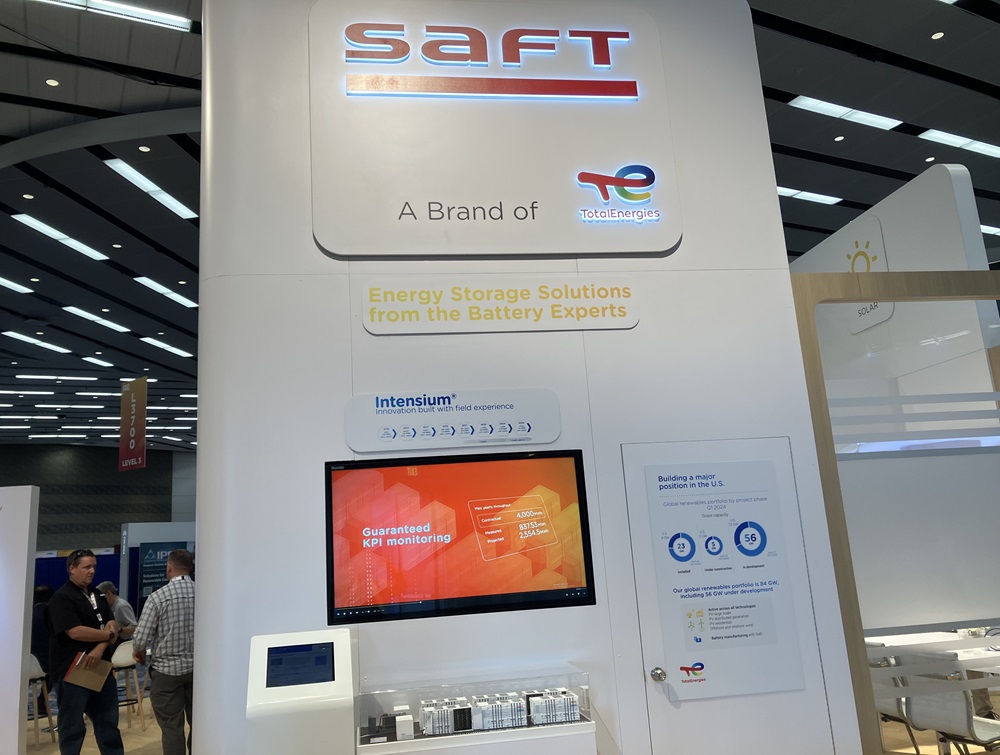
“We have taken market share in the US; we are successful. We have large projects. So, the model of producing everything in Zuhai and shipping it to the US of course, has some disadvantages in terms of timing, logistics, cost of transportation, and environmentally,” he says.
“It’s not a model we would want to pursue forever when we really come to covering the US market.”
On the other hand, the US thirst for locally made products and government incentivisation of onshoring has helped drive the decision to reopen BESS production lines at Jacksonville.
Saft Americas president Gerardo Rebollar says the delivery model from the Florida plant is “very fast,” and the first deliveries are scheduled to begin in November. Under its first ramp-up, which is underway, annual production capacity will be 1.5GWh, but Saft’s roadmap allows for expansion to 5GWh in the coming years.
US-based cell production ‘a challenge’
Both Fluence and Saft are making everything from the module to the system from their respective plants in Utah and Florida. Both are buying in cells to equip their products and solutions.
At RE+, Andy Tang, VP for fellow system integrator and manufacturer Wärtsilä, said that establishing cell production for BESS within the US at the scale demanded by the market will be difficult in the near term, with rising import tariffs for Chinese products looming ahead of implementation in 2026.
“It is a challenge,” to make cells domestically and remain competitive, says Saft’s Gerardo Rebollar. Although the company is considering two possible plans for moving forward on US cell production, it is currently outsourcing cell supply.
“It’s not easy to establish the [cell production] lines, I think it’s going to take longer. Today, there’s no capacity for supplying the American market, it’s going to take a few years. Even the current developments depend on the supply of electrodes coming from China,” Rebollar says.
Yet, he says the “added value ” of producing modules, assembling systems within the US, and providing complete solutions to customers is “already very important,” as a step towards onshoring.
Fluence was able to find a domestic source of cells after weighing up potential suppliers because Envision AESC is “reinvesting” in its factory, which previously made batteries for the Nissan Leaf electric vehicle (EV), Zahurancik says.
“They were looking for something to do with that factory. We were looking for sources of US production and talking to several companies that either have existing battery factories or are planning them,” he says.
“We like the fact that it was an existing battery factory. It’s been operating for many years in Tennessee. The workforce has been doing a good job, and now they’re reinvesting in it to upgrade to the current technology, and we’re happy to be a part of that,”