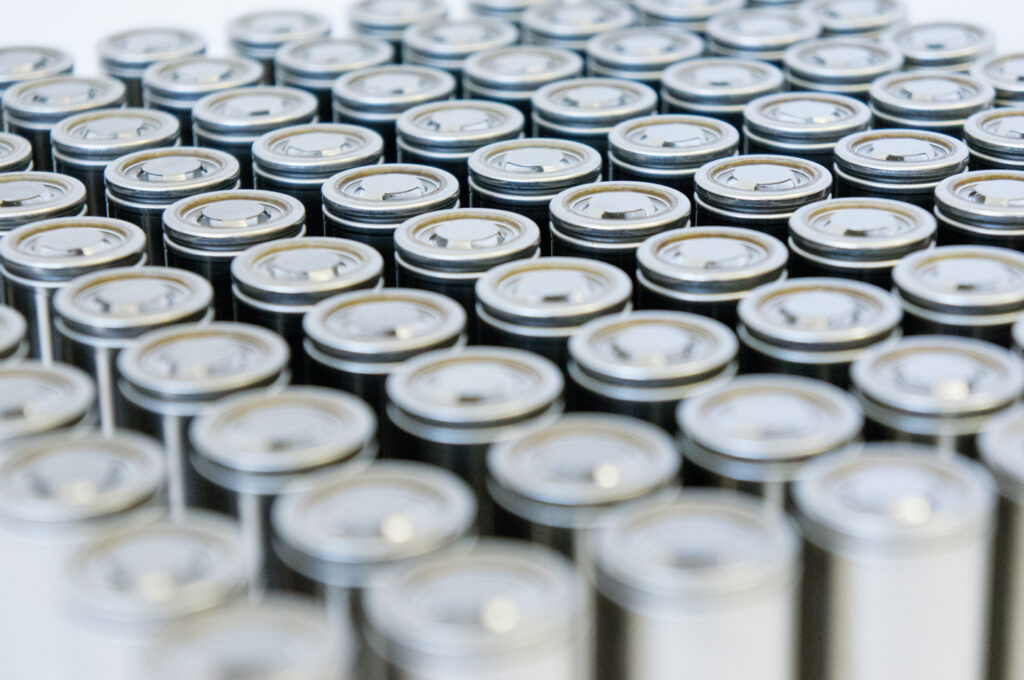
India will not be able to meet its aim of becoming a global leader in battery manufacturing unless it establishes a value chain that embraces recycling and proper end-of-life treatment as well.
A new report from environmental think tank Rocky Mountain Institute India (RMI India) highlights the need, opportunities and challenges for creating a sustainable battery manufacturing industry in the country.
Enjoy 12 months of exclusive analysis
- Regular insight and analysis of the industry’s biggest developments
- In-depth interviews with the industry’s leading figures
- Annual digital subscription to the PV Tech Power journal
- Discounts on Solar Media’s portfolio of events, in-person and virtual
It has been published a few days after India’s government announced the award of funding under its Production Linked Incentive scheme (PLI) for manufacturers of advanced chemistry cell (ACC) batteries to build 50GWh of annual production capacity in the country. Four different manufacturers’ gigafactory proposals were selected, including renewable energy company Reliance New Energy Solar, of Reliance Industries.
RMI India, together with Indian government technology and innovation think tank NITI Aayog published a previous report together in the same series, which explained the drivers for creation of a domestic battery making industry.
That report, out in February, identified demand for batteries across India could reach between 106GWh and 260GWh by 2030 from all sectors including transport, energy and consumer electronics.
With India targeting 500GW new renewable energy capacity additions by that date, the need for stationary energy storage is likely to be a significant source of demand, albeit the majority will be accounted for by electric vehicles (EVs). India’s Central Electricity Authority has modelled the need for about 27GW/108GWh of stationary storage to integrate that mostly wind and solar capacity.
India could see fastest growth in demand
The sustainability report highlights that as well as ethical and environmental concerns over battery supply chains, there will also be scarcity issues for materials like lithium, cobalt and nickel.
This is already happening worldwide, with one US-based expert having told Energy-Storage.news that supply chain issues are reaching a “crisis point” today, largely based on soaring lithium carbonate prices.
RMI India quoted BloombergNEF research, which identified India as the region with the most expected demand growth for lithium-ion batteries from 2020 to 2030, even above bigger markets in China, the US and Europe. However, while India has ample reserves of magnesium and iron, it has minimal and insufficient reserves domestically of other key materials like lithium, graphite, cobalt and nickel.
The country’s first lithium deposit was discovered in early 2021 and even with the other resource challenges, RMI India found that India will need to grow its domestic manufacturing capability to meet its storage needs and minimise energy security risks posed by being overly reliant on imported fossil fuels.
Because of this, in order for India’s push to create a domestic battery manufacturing industry to succeed, circular economy principles need to be implemented, RMI India said.
Recycled materials could meet more than 20% of India’s lithium-ion battery needs by 2030, if there is accelerated uptake of electric vehicles in the years leading to then, while even in a base case EV adoption scenario, around 5% of the essential minerals like lithium, nickel and cobalt used in India-made batteries could come from recycled materials.
Efficiencies for commercial recycling of lithium batteries are already very high at around 95% or even more, but the supply chain and circular economy strategies are not widely in place. Obtaining recycled minerals could potentially also be a lower carbon process than extracting them new.
Second life battery storage — BESS made with repurposed electric vehicle batteries — could also be a good way to reduce the cost of batteries, which usually make up about 40% of the total cost of a battery energy storage system.
Reusing larger battery packs from e-buses as well as from passenger and commercial vehicles could provide for about 5% of the required BESS capacity India needs by 2030.
135% annual increase in recycling capacity needed to meet targets
India’s Ministry of Environment, Forest and Climate Change (MOEFCC) introduced draft rules for management of battery waste in 2020, having identified that existing management and handling policy was inadequate for the expected huge volumes of batteries to come by the end of this decade.
The rules would apply to all kinds of batteries and call for collection of 30% of all end-of-life batteries by weight within two years of the policies being introduced, with the target increasing to 70% in the seventh year after implementation.
RMI India said that meant if the 30% target were to be enacted in 2023, that would represent between 20,000 and 102,000 tonnes — or between 2.4GWh and 11.7GWh — of batteries being collected.
India’s annual recycling capacity would need to grow by at least 135% each year from 2021 to 2030 to succeed — a “substantial build out” of capacity — even in the think tank’s base case scenario for EV adoption.
Europe is currently seeking to adopt rules of its own on battery sustainability and supply chain security, mandating a gradual introduction of recycled content and carbon footprint labelling over a number of years. The European Union’s Battery Directive is at the stage of being negotiated with individual Member States to take its final form.
While the EU’s Battery Directive has been broadly welcomed by the industry for its intent, some groups have expressed concern that over-regulation could risk hampering the continent’s international competitiveness.
The MOEFCC rules could reduce upstream battery production emissions by 50,000 to 180,000 tonnes by 2030. RMI India acknowledged the importance of the policy, but made several recommendations for bettering the draft rules:
- Labelling and transport: the draft rules lack clear guidance on labelling for lithium batteries of various kinds, which could result in lithium battery and lead-acid battery waste becoming commingled. This could present a health and safety threat and standardised labels should be decided.
- Battery reuse: the draft rules only contain rules on battery collection, not reuse, and also mandate that collected items should go to designated recyclers. This does not afford room for EV batteries, many of which will often still be usable for stationary storage after a period of use for transport, to be given a second life. Meanwhile there are no standards or certifications for safe use of second life batteries, which should be introduced.
- Performance standards and warranties: similarly, there is a lack of a transparent system for assessing used battery health or warranties ensuring performance standards for second life batteries, as there are for new systems. The industry should be able to make the choice of using second life batteries safety, RMI India said.
- Ways to pay for recycling efforts need to be determined that are fair and do not affect the competitiveness of the EV industry against internal combustion engine (ICE) vehicles by passing on costs.
- Consumers should be incentivised to comply with battery rules: for example, rebates for returned batteries or deposit systems.
- Enforcement: the rules need to be enforced and penalties applied when they are broken, but through a transparent and fair system.