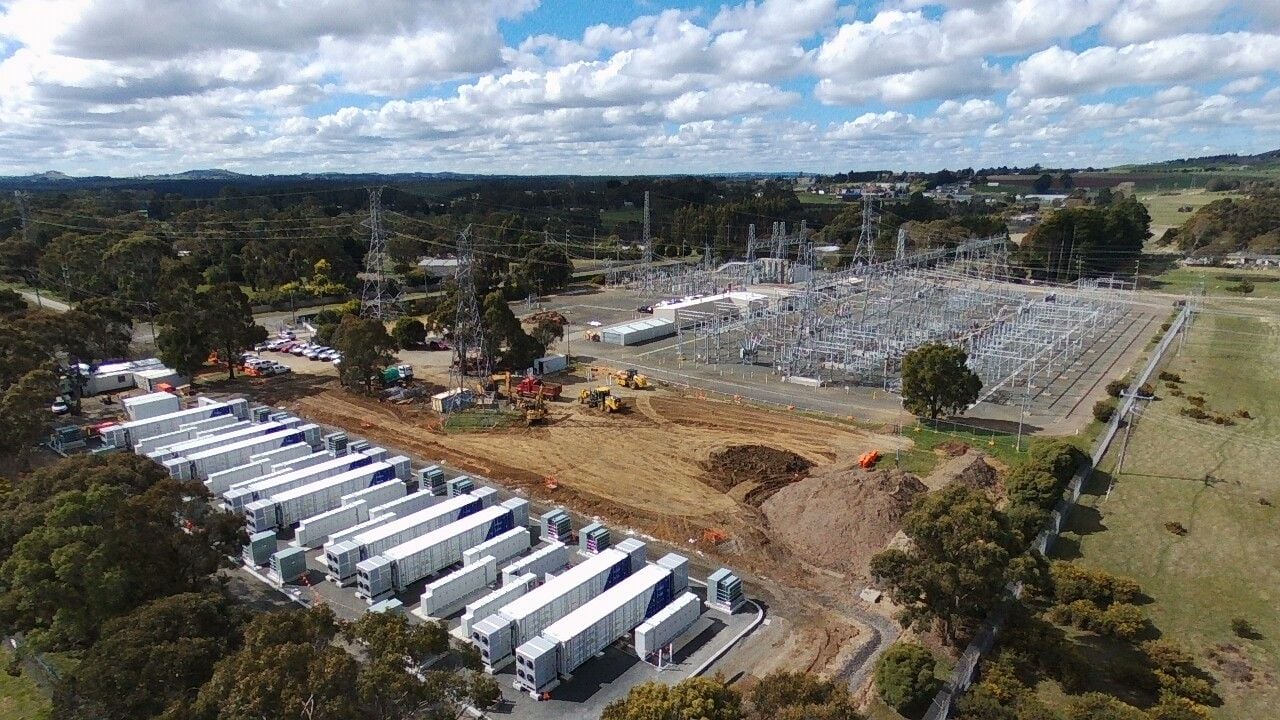
Fluence has been able to keep working on “all but two or three” of 73 utility-scale battery projects, with battery energy storage increasingly considered an essential part of grid infrastructure in many parts of the world.
Energy-Storage.news spoke to John Zahurancik, chief operating officer (COO) at the technology provider formed in a joint venture (JV) between power project developer AES Corporation and engineering giant Siemens.
Enjoy 12 months of exclusive analysis
- Regular insight and analysis of the industry’s biggest developments
- In-depth interviews with the industry’s leading figures
- Annual digital subscription to the PV Tech Power journal
- Discounts on Solar Media’s portfolio of events, in-person and virtual
Zahurancik said that while there have been some necessary delays and adjustments to working practises to minimise the possibility of COVID-19 transmissions, nearly all of the company’s project pipeline is “moving ahead in one form or another”.
“We’re very actively out and doing installations of equipment in most cases these are utility-scale energy storage installations that the construction of those has in most spots been exempted from restrictions on shutting a business down or it’s considered to be part of critical infrastructure development,” the Fluence COO said.
A ‘bigger and bigger part of the conversation’: Energy transition and economic recovery
Longer term, John Zahurancik said that energy storage will be “part of the conversation” in how economies move to restart and move forwards once the pandemic is finally under control. Energy storage has been an “increasing part of the conversation in terms of infrastructure,” in replacing ageing infrastructure as well as in terms of the transition to a cleaner and more efficient electrical grid already, he said.
“We see more of the infrastructure planners, whether those are utilities or regulatory bodies, or other people that are dealing with long-term infrastructure, include energy storage as part of their long-term planning cycles. We’re seeing people conduct solicitations, procurements for energy storage all around the world in different forms.
In some places it’s aimed at strengthening the generation side, in complement to renewables, in other cases it’s aimed at strengthening the transmission and distribution side, you even see energy storage at the customer-sited level for resiliency and cost reduction,” Zahurancik said.
“It’s been a kind of growing general part of all of the investment, so as people begin to look at ways to move things forward, it’ll be part of that conversation. It’s largely been something that’s grown on its own without a lot of incentives or subsidies, it’s really been the economic and other benefits of adding storage that have really been what’s driven it around the world.”
Short-term supply chain delays and the productivity costs of social distancing
As Fluence’s CEO Stephen Coughlin pointed out in a letter to partners published by the company in early April, Fluence is working on a pipeline of 73 projects in 13 different countries, with both parent companies continuing to “provide their full backing and support” over the lifecycle of those projects.
Coughlin himself has since stepped down as CEO, but the situation around the pandemic response appears to have not changed too much as far as the company is concerned. John Zahurancik elaborated on that response effort for Energy-Storage.news, explaining that “out of that whole portfolio of projects we only have two or three sites where for various reasons the owner of the project has decided to completely shut the site down”. Office staff meanwhile have gone to working remotely, while as much maintenance as possible is also done remotely via videoconferencing and so on.
On-site, Fluence has had to add some “steps and procedures to follow,” although the COO did say that there is a “natural advantage in that most of our projects are outside,” making physical distancing feasible. It has cost the company some productivity and “added some steps to the day,” while there have been some delays in getting equipment and parts shipped through the supply chain.
“I think we often have the ability to spread people out across a job, there’s not a lot of work where you have to keep people very, very close. There are certain jobs like that that we’ve had to rethink but in a lot of cases we can take advantage of space and put people in different locations and keep people moving.
“Where there’s delays in getting parts, where there’s delays in shipping and other aspects, those tend to accumulate also. Fortunately, those have typically been on the order of days and weeks for projects rather than longer… In this environment one of the biggest things has been remaining agile, remaining flexible to be able to adapt to the conditions that emerge”.