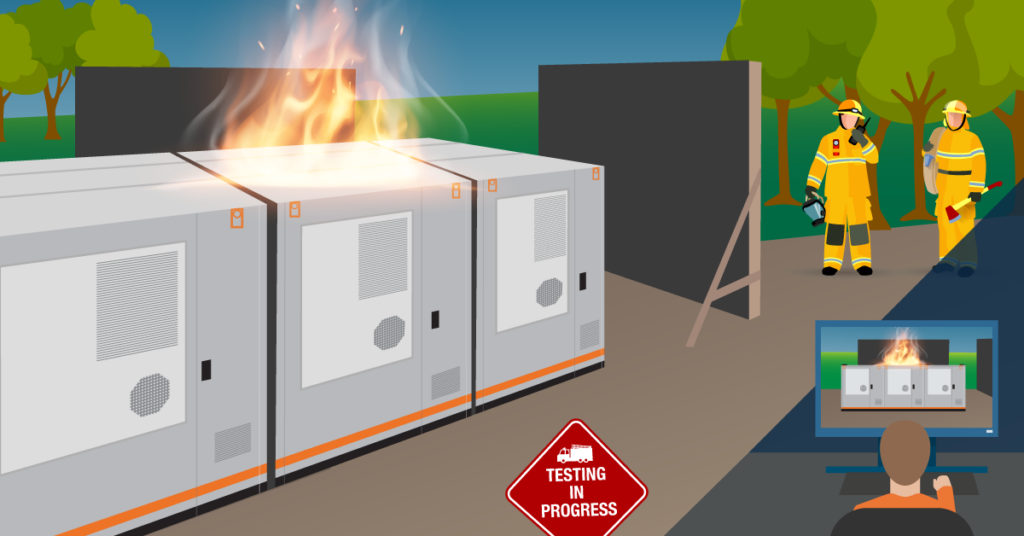
Energy-Storage.news Premium’s mini-series on fire safety and industry practices concludes with a discussion of strategies for testing and the development of codes and standards.
Safety continues to be a number one priority for the battery storage industry but considering media reports around community opposition to new-build projects, that message is perhaps not filtering down to the public.
Enjoy 12 months of exclusive analysis
- Regular insight and analysis of the industry’s biggest developments
- In-depth interviews with the industry’s leading figures
- Annual digital subscription to the PV Tech Power journal
- Discounts on Solar Media’s portfolio of events, in-person and virtual
As we have seen in numerous territories in the US and UK in particular, battery energy storage system (BESS) technology is sometimes perceived by local communities as a potential fire and even explosion hazard.
In this series, we have examined some of the things companies in the industry are doing to mitigate fire and explosion risk.
In the previous two instalments, we have spoken with Trina Solar executive president Helena Li about the role product design plays in ensuring safe operation, and with Accure CEO Kai-Philipp Kairies about the implementation of battery data analytics.
This time out, we speak with Wärtsilä senior development manager Mats Östman and product manager Chris Groves, who focus on the safety aspects of the company’s solutions.
‘Industry megatrends’: Bigger projects, higher energy densities
Even as recently as four years ago, a really big project might be in the ballpark of 100MWh, whereas today, it is fairly common in advanced markets to see projects that push the 1GWh threshold at a single site, Östman says.
Looking further back, “there was no real standardisation,” he says, with portfolios engineered on a project-by-project basis.
From around 2020, modular designs began to emerge on the market, arguably led by Tesla’s Megapack, but with others such as Wärtsilä’s own Gridsolv Quantum series representing more standard solutions delivered to sites with pre-installed batteries.
Since then, one of the other elements that has moved the industry along is the adoption of higher energy density solutions, with cells’ physical formats remaining largely the same but capacities moving from around 280Ah to more typically exceed 300Ah. Meanwhile 20-foot standard containers are coming in at 5MWh capacity or more.
These “industry megatrends,” as Östman describes them, mean that the products used have to be more reliable than ever before.
Testing for worst-case scenarios and the safety needs of AHJs
For example, one of Wärtsilä’s current product lineup, the Quantum High Energy (Quantum HE), uses 306Ah cells, and, like the other two Quantum products, Quantum and Quantum 2, a lot of safety testing has been done to bring them to market, Chris Groves says.
The company has long been vocal about the critical need for fire safety to be treated with the utmost seriousness for the energy storage market to grow, and more specifically, the need for fire testing to not just meet required standards but also to consider worst-case scenarios.
Groves says the company “took a lot of lessons” from large-scale fire tests, including adopting NFPA 69, the US National Fire Protection Association (NFPA) standard on explosion prevention systems by venting of gases. Wärtsilä decided to also add NFPA 68 (standard on explosion protection by deflagration venting) partial volume compliance as an option.
Along with other new features, such as prefabricated firewalls that take the system’s fire rating from 60 minutes to 240 minutes, the company improved the door-locking mechanisms to allow easier operation by firefighters.
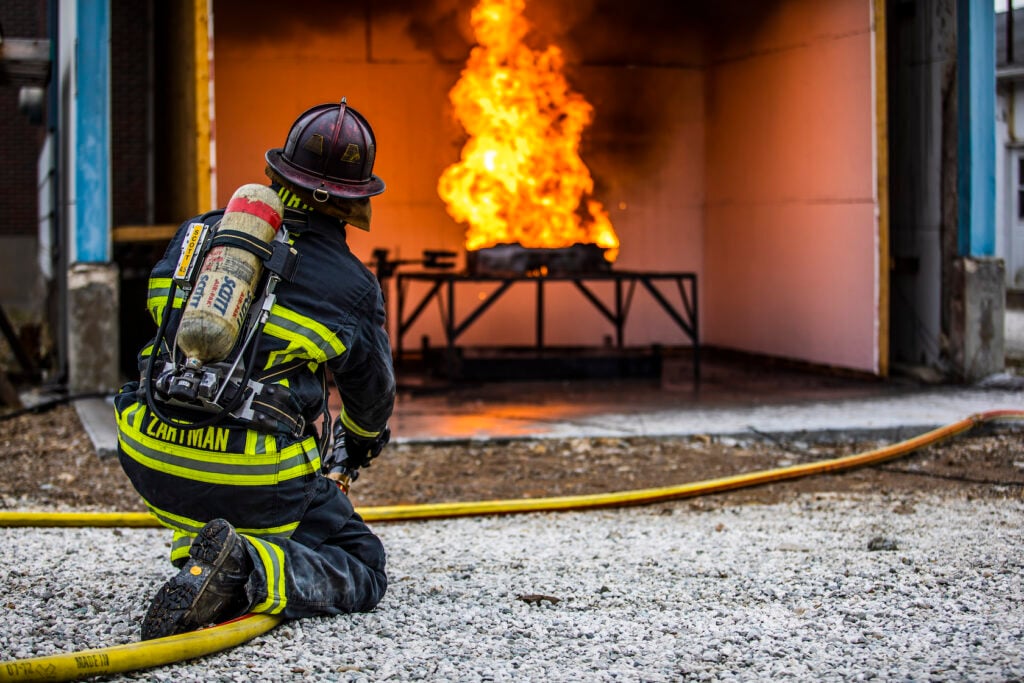
Another industry standard test is UL9540A, which forces a cell into thermal runaway and assesses its risk of catching fire and propagating to other cells, racks and other components of the BESS.
However, while useful, UL9540A has some potential shortcomings, Groves says, which is one of the reasons why Wärtsilä carried out large-scale fire tests, essentially setting entire Quantum BESS units on fire.
“We don’t believe heating a single cell is representative of a worst-case scenario. For example, you had multi-cell failure during the fires that were seen last year and other incidents that happened during commissioning. You could have a forklift hitting a unit, you could have a lightning strike,” Groves says.
Minimal propagation could be seen in a module with a UL9540A test, leading stakeholders to conclude that the whole system would be safe in a thermal runaway event. However, Groves says the company introduced fire to the entire unit, thereby validating that unit-to-unit propagation would not occur.
It is understood that the UL950A test regime will be updated to include, among other things, multi-cell level, module level and unit-to-unit fire testing, along the lines of what Wärtsilä has been implementing already.
Education of stakeholders from public authorities to industry
Wärtsilä is part of a task force in the US examining UL9540A and NFPA 855, the latter being the main standard for the safe installation of energy storage systems.
Comprising certification agencies, authorities having jurisdiction (AHJs) and National Recognised Testing Laboratories (NRTLs) alongside industry players, the coalition of stakeholders will redesign tests and standards “along the lines of what AHJs want to see,” Groves says.
AHJs, which typically include local authorities such as town planning committees and fire departments, are essentially the gatekeepers between local communities and energy storage developers and have the final say on whether projects will proceed.
AHJs are becoming more aware of energy storage technologies and what a project involves, but at the same time, the industry needs to also be aware of what AHJs are looking for.
“A lot of it is around education. Many developers just have a checkbox: ‘What’s UL9540A? Do we have this?’” Groves says.
Developers should understand that project safety needs to be considered in a more “site-specific context,” in addition to having a system compliant with UL9540A.
“Do you have two access roads for the fire department? How wide are your roads? Can your roads support a fire truck? These are all questions that an AHJ wants to understand. When they come to a site, where do they access it? Where can they find the information? Where can they get a copy of the Emergency Response Plan (ERP)?”
Many AHJs are also seeking more training in energy storage system safety. Steps Wärtsilä has taken include creating a generic ERP adaptable for different projects in different markets.
“Fires in the industry are bad for everybody,” Groves says.
“They’re a black eye, and we need to be actively working as an industry to ensure that these developers and these residents near them are safe and comfortable with what’s been deployed.”
This article has been amended from its original form to better reflect accuracy of Chris Groves’ quotes around NFPA 69 and NFPA 68.