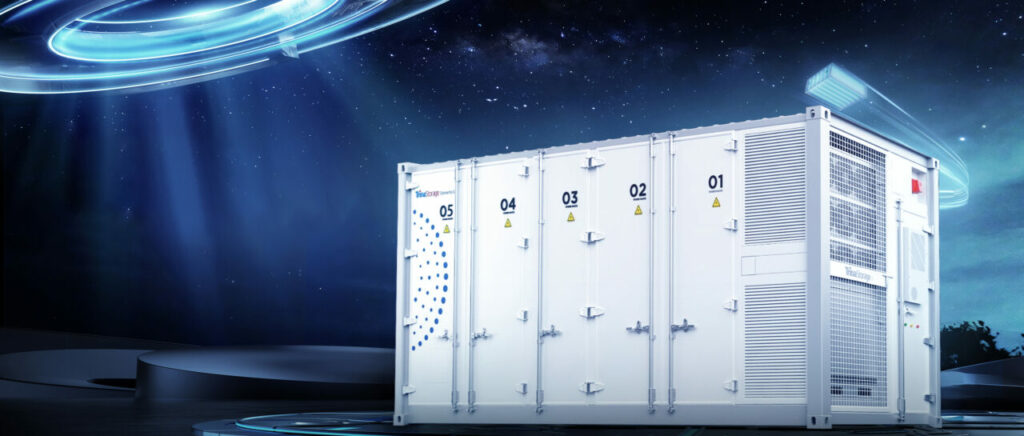
In a new series, ESN Premium looks at measures being taken to reduce fire safety risks associated with battery storage systems.
Battery storage safety continues to be a number one priority for the industry but considering media reports around community opposition to new-build projects, that message is perhaps not filtering down to the public.
Enjoy 12 months of exclusive analysis
- Regular insight and analysis of the industry’s biggest developments
- In-depth interviews with the industry’s leading figures
- Annual digital subscription to the PV Tech Power journal
- Discounts on Solar Media’s portfolio of events, in-person and virtual
As we have seen in numerous territories in the US and UK in particular, battery energy storage system (BESS) is sometimes perceived by local communities as a potential fire and even explosion hazard.
Several jurisdictions in the US have passed moratoria on new developments, with a noted concentration of such rulings in New York State, which follows both a spate of fire incidents at battery storage systems there, and fires caused by faulty or misused micromobility devices. New York’s Governor Kathy Hochul has convened a working group across different state agencies to ensure the rollout of storage can continue, or in some cases, resume.
Meanwhile in one high-profile case from the UK, a solar-plus-storage project deemed a Nationally Significant Infrastructure Project (NSIP) has had its fire safety management plan rejected.
Not all local opposition to battery storage is around this safety aspect, there are other cases where changes to the landscape or to wildlife habitats are cited, among other reasons, but these other reasons are often very specific to individual projects.
In contrast, fire safety is a concern that spans a whole range of projects in different regions due to the lithium battery technologies used that most BESS projects have in common.
In this series, we will look at some of the things that companies in the industries are doing to mitigate fire and explosion risk, starting with manufacturing and product design.
Embedded layers of protection
“Quality control of everything,” is critical in designing and making products for the stationary energy storage sector, says Helena Li, executive president at Trina Solar, one of the world’s biggest and most vertically integrated solar PV manufacturers.
Trina Solar has of course launched Trina Storage, a BESS subsidiary which has designed and produces complete energy storage systems as well as components that include cabinets and containerised enclosures.
Trina also makes its own lithium iron phosphate (LFP) cell in-house which Elementa 2, the company’s latest BESS solution for the large industrial and grid-scale markets, is equipped with.
To best meet customers’ needs, Trina wants to control every step of the manufacturing process that it can, Li says. This need is probably more acute in the storage industry than it is even for solar because the precision required for making batteries and related equipment is “critical” and very closely related to safety and performance of finished products.
Beyond manufacturing quality, which is an essential but often overlooked aspect of safety and not just of performance or bankability, lies product design.
Elementa 2 has multiple levels of safety features in its design. It has four detection systems, including the Li-ion Tamer flammable gas detection hardware from Honeywell subsidiary Xtralis, and smoke and temperature change detection built into the cabinet.
There are also what the company calls a full range of embedded protection layers inside. There are three layers of battery management system (BMS) and electrical protection systems. For example, there are three levels of fuse protection, one installed on the HV cabinet or rack side, and a combined fuse where multiple racks are connected in parallel. Meanwhile, the fuse installed on the DC side of the power conversion system (PCS) is integrated into the protection system.
The company claims that having those fuses at three levels means protection from any short circuit current. In addition, the storage solution comes equipped with a container-level switch breaker and relays on the HV cabinet.
Planning for every safety scenario from daily operation to worst-case
Planning for safety also means planning for worst-case scenarios, and as well as those above components and features for detection or preventative measures, Elementa 2 features an aerosol-based fire extinguisher system.
With certification and standards an evolving piece for BESS, the solution is compliant with NFPA 68, which refers to devices and systems that vent combustion gases and pressures resulting from deflagration events and NFPA 69, which pertains to explosion prevention systems for enclosures.
In those worst-case scenarios, flammable gases can concentrate inside the container, and it becomes necessary to have venting to direct gases out of the container to prevent them building up to cause explosions. Elementa 2 is equipped with deflagration venting on the ceiling of the container, which can release or lower internal pressure.
As an optional add-on, there is also a water-based extinguishing system, for contingencies where there is a possibility of flames reigniting.
Prevention is also part of the regular operation and maintenance (O&M) of the BESS. Increasingly, manufacturers, including Trina Storage and their customers, are turning to liquid cooling systems for thermal management.
Helena Li says the product’s thermal management system keeps the internal temperature within a 2.5°C delta. The liquid flow duct is designed to control the volume and flow rate of the liquid coolant. This makes sure that when the coolant goes to the very bottom of the pack it can still make an impact on the temperature, with the design based on modelling from repeated simulations.