Standards, guidance and best practice relating to the installation and deployment of battery storage are often talked about in the industry, and rightly so. What is perhaps less often focused upon, is evaluation of the battery equipment itself before it even leaves the factory.
Well known in the solar industry as a provider of quality assurance and independent evaluation, Photovoltaik Institute Berlin (PI Berlin) is also now focusing on lithium-ion batteries. The group saw an opportunity after increasing demand from clients on the PV side, where PI Berlin has assessed over 90GW of modules from around 125 different manufacturers.
Enjoy 12 months of exclusive analysis
- Regular insight and analysis of the industry’s biggest developments
- In-depth interviews with the industry’s leading figures
- Annual digital subscription to the PV Tech Power journal
- Discounts on Solar Media’s portfolio of events, in-person and virtual
The premise of its new lithium cell assessment service is that when it comes to battery storage devices, it’s as important to assess the manufacturing process and the quality of that process as it is the quality of design, the chemistries used and the technologies of the cells themselves.
PI Berlin’s energy storage specialist Benjamin Sternkopf and PI Berlin North Americas managing director Ian Gregory spoke with Energy-Storage.news’ Andy Colthorpe about some of the different things their team will be looking out for when evaluating battery manufacturers, why Tier 1 doesn’t necessarily mean better than Tier 2; and why sometimes, “energy storage is not about energy storage”.
We always hear about why storage is needed for ‘when the sun doesn’t shine and the wind doesn’t blow”, but in reality the business of energy storage can be a little more complicated than that and is geared towards the services batteries can provide on a market basis. So what are the main applications you’re seeing batteries used for right now by the renewable energy industry?
Benjamin Sternkopf: If we look at it from a technical perspective, you’re right, energy storage, especially lithium-ion energy storage, is not necessarily primarily used for typical energy shifting applications such as renewable or per diem energy storage.
On a techno-economic perspective, lithium-ion batteries are most competitive if you compare them on a power basis: if you look into what it costs to reserve 1MW or 10MW of active power over a given period to provide some fast-responding services.
That’s really what they excel at. It’s the bi-directional operation, reaction speed and the accuracy which is unmatched by any other technology, both on the generation or load side. So, often I like to say: ‘energy storage is not about energy storage!’
As we’ve seen in the US and other markets, the most attractive applications are in these power-based markets – although what we also see [now] is a shift towards those so-called energy-based applications where storage is being used as a reservoir to store energy nowadays, typically over a period of four hours.
These are typically tendered together with PV power plants in some kind of hybrid power purchase agreement (PPA), where the tender is requesting that power should be provided over a certain time, for example peak hours in the evening and this is practically only feasible using battery energy storage systems.
Power-based applications are the most attractive from a technical perspective but energy-based applications are becoming more and more viable, because tenders do not only include generation when power is available, but also include requirements for peak hour delivery.
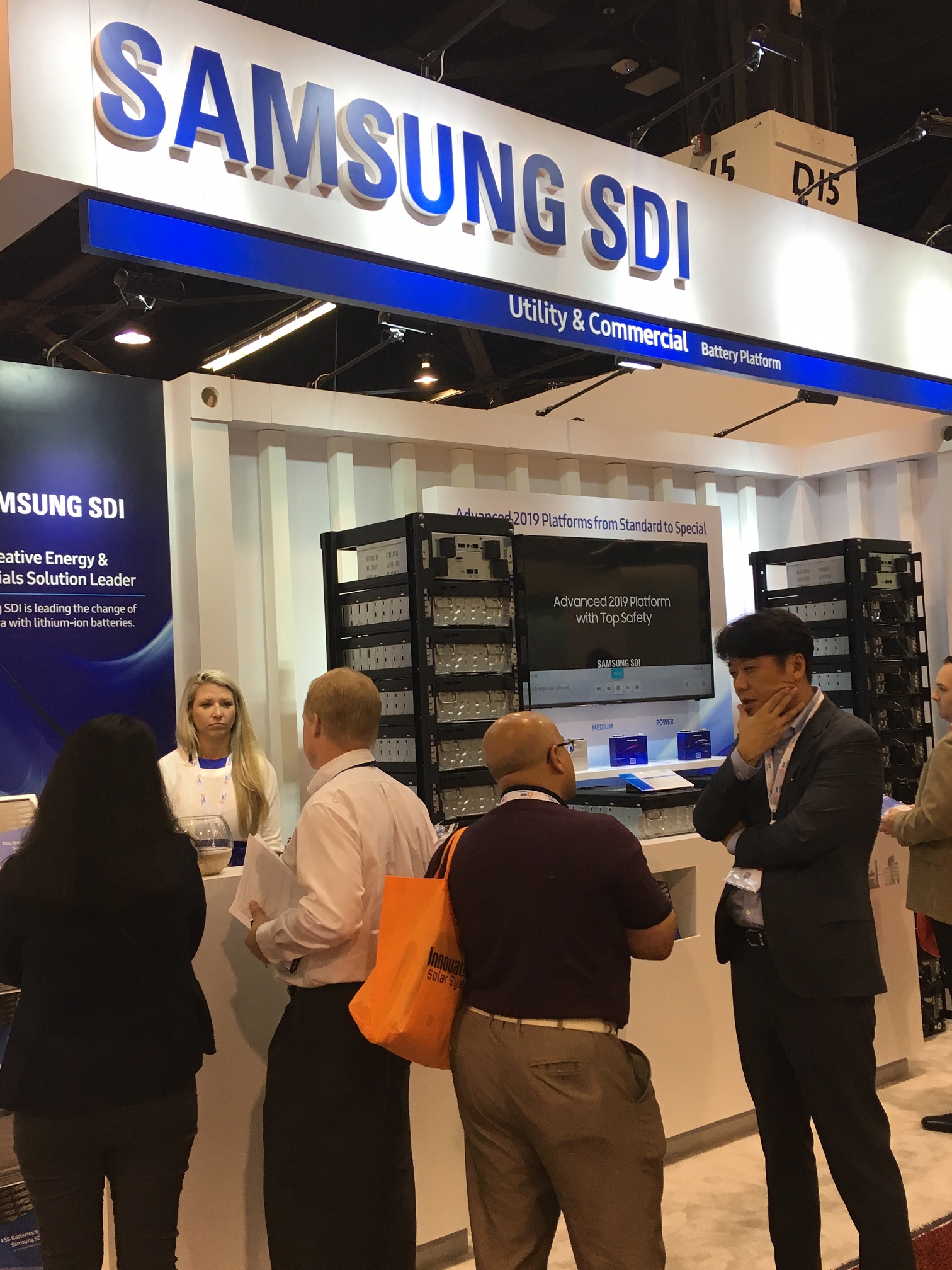
So where does battery assessment service from PI Berlin fit into that? What are some of the things you’ll be assessing, what sort of assurances will you be able to provide?
Ian Gregory: The service has developed organically for us and demand has come from a wide range of our existing clients.
We’ve learned the importance of quality and we’ve split it into two: on one side is the quality of the material that goes into the equipment and that’s often validated by testing – stress testing in a lab or other facilities.
Then there’s the quality of the manufacturing process. Both need to be there – good quality materials and good quality manufacturing. If either of those isn’t right the product may not be reliable, it may not be safe, it may not perform the way you expect.
As we see the number of lithium-ion manufacturers proliferating, and bringing lower cost batteries to market, the question naturally comes up: can we trust these batteries, are they going to perform in the long run, are they going to be safe? Not just from a battery design perspective, but also from a manufacturing quality perspective.
We are flushing out and finding things that directly relate to a manufacturing process or a quality of raw material going into a battery that is very likely to have an impact on performance and reliability down the road.
Doing the diligence at this level – literally going through the assembly process of a battery step by step and looking at risk is becoming a very important process. Just like on the PV module side, there really is no good manufacturing quality standard for batteries used in PV applications that customers can rely on. That’s a key reason to develop this kind of protocol and the quality ratings that come out of our assessments help our customers benchmark one battery against another.
What sort of bad practices might you be looking out for, conversely, what constitute good practices?
Ian Gregory: What we learned on the PV module side is that Tier 1, Tier 2 even Tier 3 is not a good correlation to quality. The Tier system was originally developed as a way to distinguish between Asian manufacturers by size – large, medium and small. However over time it became synonymous with quality. The results of our work on the module side show very clearly that it’s by no means a guaranteed correlation.
We see Tier 2 manufacturers producing excellent quality modules, and Tier 1 manufacturers producing poor quality modules. Just because a manufacturer is bigger and regarded as more bankable, [it] doesn’t mean the quality of the product is equivalent.
Benjamin Sternkopf: What you would generally be looking at with batteries are things that are surprisingly similar to PV modules or inverters. However it’s even more necessary to look into it during the production process itself.
The inner workings of a PV module are much more exposed (visible). Very little of a battery cell is exposed. With a PV module there are some obvious defects you can just visually see, whereas initial defects with a closed battery cell are really hard to detect. So it makes a lot of sense to look into quality during the manufacturing process.
Ian Gregory: What we are look at during our audits is specifically for two factors: firstly is where manufacturers are intentionally trying to skip through some processes or quality control management assurances to save costs and secondly, where they might accidentally be doing the same.
Regarding specific processes in making batteries that can be of concern, we really have to look at the drying processes. That’s really critical with lithium-ion batteries because any moisture and humidity that’s kept inside the batteries is going to increase degradation.
You want to make sure humidity and moisture removal is as good as required. You’d like to go as low as possible but it’s not cost-effective so it’s about finding the right balance and asking if enough measures are being taken in any production where moisture and humidity can enter – or is it just too much of a shortcut that’s being taken?
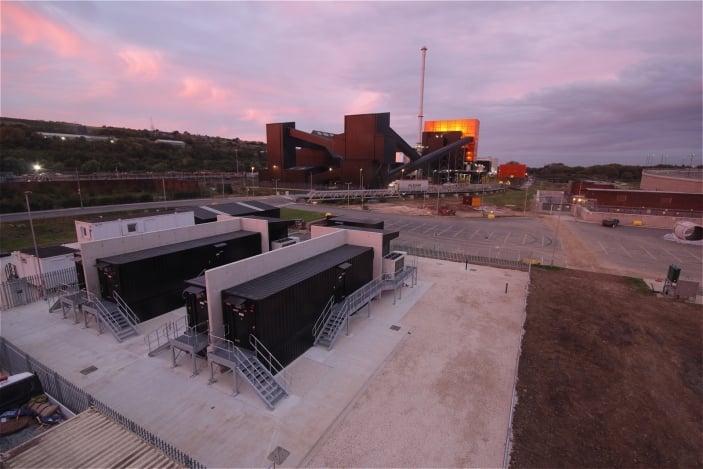
There’s obviously a close link and even comparisons to be made with the solar industry, but of course the symbiotic relationship to electric vehicles (EVs) is perhaps even stronger. Are there pitfalls in going from one industry to the other, or is it a solid strategy to pivot from one to another? For example, One of the world’s most prolific EV battery makers CATL is now producing battery cells and packs specifically for stationary energy storage.
Benjamin Sternkopf: Historically, most of the battery cells supplied for stationary energy storage applications have just been the same type as cells used in automotive production. That has specific advantages and disadvantages.
The advantage is that the stationary energy storage industry has benefited a lot from the synergies with automotive applications. Both from a research perspective – because we have the same improvements in lifetime, for example – and in quality assurance. But on the downside, the disadvantage is that we’ve got cells that are optimised for an application that’s not ours.
Automotive suppliers have a focus on energy density, because you want to have a long range with your vehicle, but energy density is really not a decisive factor for stationary applications, and so there’s a kind of imbalance in optimisation that every battery cell is.
There is no perfect battery cell, but there are battery cells optimised towards specific characteristics. Some of those optimisation characteristics are cost, energy density, power density, lifetime and every cell design is a compromise between those. You cannot make or buy a cell that excels in all characteristics.
This optimisation towards automotive applications is something that is remedied a bit with suppliers switching to specific cell models for stationary applications. Now we can get battery cells that are optimised to a very narrow range of temperature, for example, that we can easily fulfil in stationary applications. We can get battery cells that are optimised towards lower cost rather than high energy density so this gives us a cost-saving potential for stationary energy storage. However the downside is that we don’t benefit from the quality management that the automotive industry has provided previously, we don’t have large automotive manufacturers going to factories and doing their audit, we have to go there ourselves and check it out.
We are getting an advantage which is most notably lower cost, but we also have to put some work into this because now the quality assurance is entirely left to the stationary energy storage industry. That’s something that you have to take care of.
At the start of this interview we mentioned the diversity of applications for batteries for the grid. Some of the bigger players in the grid-storage industry now tout a very wide number of very different use cases for batteries. Are you able to assess application-specific battery cells and is it a challenge to keep up with those?
Ian Gregory: You can do a lot to validate the performance of the battery in a particular use case, through testing, that’s one important piece.
We’re not a big lab testing batteries but on the manufacturing level we are doing a complete assessment – everything from the incoming raw materials focused on the quality, the homogeneity and purity of key chemical components of the chemistry in a battery, right through to the testing of the whole battery as a finished product. That might solicit an array of risks.
That provides us with a baseline for battery quality independent of the ultimate use-case in any particular project. When a customer comes to us and says a battery will be used in a particular use case, we can review our audit findings and assess what risks will be relevant.
We’d do a very generic assessment that covers all bases and then working with the customer establish what their use case is – which itself may change over time.
We’ve certainly had clients that have installed batteries three years ago thinking they will be operating in use case and now finding that they’re actually operating in another.
Cover Image: A range of different lithium-ion batteries. Credit: PI Berlin.