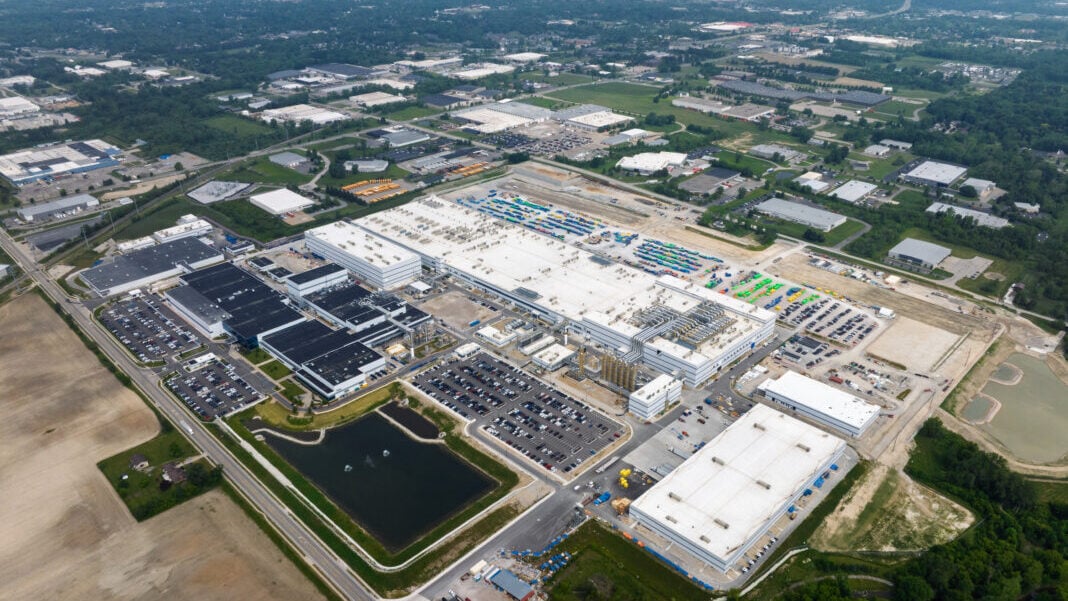
Two companies, First Phosphate and LG Energy Solution, have recently begun manufacturing lithium iron phosphate (LFP) battery cells in North America.
The announcements come as domestic manufacturing is being especially emphasised after the signing of the US budget reconciliation bill into law.
According to the Foreign Entity of Concern (FEOC) regulations, to qualify for investment tax credit (ITC) incentives, starting in 2026, at least 55% of a project’s costs must originate from non-prohibited foreign entities, rising to 75% by 2030 and onwards.
This is highly likely to include materials, equipment and financing originating in China. At the same time, the tariff dispute between the US and China, while currently ‘paused’ with import tariffs for batteries at 54% of the goods’ value until 12 August, has also thrown the industry a major curveball.
Enjoy 12 months of exclusive analysis
- Regular insight and analysis of the industry’s biggest developments
- In-depth interviews with the industry’s leading figures
- Annual digital subscription to the PV Tech Power journal
- Discounts on Solar Media’s portfolio of events, in-person and virtual
Speaking with Energy-Storage.news, Isshu Kikuma, energy storage analyst at BloombergNEF (BNEF) recently said:
“If you look at the safe harbour cost table for domestic content, battery cells account for around 52%, so because the threshold for the non-prohibited foreign entities starting from 2026 is 55%, it will be very crucial for all projects in the US that want to get their tax credits to use non-prohibited foreign entity-related cells.”
US-made batteries are far from abundant, positioning First Phosphate and LG ES in what could soon become a rapidly developing market.
First Phosphate produces LFP cells in Quebec
First Phosphate has produced commercial-grade LFP 18650 format battery cells using “North American-sourced critical minerals.”
The company is based in Canada and connects phosphate mining in Quebec with US battery supply chains.
First Phosphate says its batteries are aimed at the energy storage, data centre, robotics, mobility, and defence sectors.
A recent report from the Congressional Research Service (CRS) notes critical minerals as “nonfuel mineral(s) essential for use and facing considerable supply chain vulnerabilities.”
The table below details where First Phosphate’s critical minerals are sourced from.
Mineral | Source |
Phosphate | “High-purity phosphoric acid produced from igneous phosphate concentrate extracted from the First Phosphate Bégin-Lamarche property in Quebec, Canada and processed in the pilot installations of Prayon Technologies of Belgium, Europe.” |
Iron | “Iron powder produced using magnetite concentrate from the First Phosphate Bégin-Lamarche property in Quebec, Canada and processed by GKN Hoeganaes of Tennessee, USA.” |
Lithium | “Lithium carbonate produced by Century Lithium Corp. (TSXV: LCE) from its operations in Nevada, US.” |
Graphite | “Natural graphite-based active anode material produced by Nouveau Monde Graphite (NYSE: NMG) from its operations in Quebec, Canada.” |
Ultion Technologies, a private battery technology company based in Las Vegas, Nevada, assembled the cells for First Phosphate.
In 2023, First Phosphate signed a memorandum of understanding (MOU) with American Battery Factory (ABF), which partnered with KAN Battery in the same year, also to pilot a line of LFP battery cells, to on-shore up to 40,000 tonnes of annual LFP cathode active material production in North America.
Speaking with ESN, First Phosphate CEO John Passalacqua confirmed that the MOU with ABF is still in place and should remain until 2028.
LG ES operates LFP cell factory in Michigan
In 2024, LG Energy Solution (LG ES) started construction on an Arizona gigafactory, which was planned to have an annual 17GWh production capacity dedicated to the BESS market.
The factory would produce cylindrical 46-Series electric vehicle (EV) batteries and pouch-type LFP batteries for BESS applications.
That factory was put on ‘pause’, with LG ES head of ESS Hyung-Sik Kim and LG ES Vertech CEO Jaehong Park telling Energy-Storage.news Premium it was part of a strategy to shift capacity between EV and ESS products based on lower than expected demand for the former and growing demand for ESS.
In February this year, the company informed the Korea Stock Exchange that it had chosen to offer a debt guarantee to its affiliate, LG Energy Storage Michigan. LG ES said it would invest around US$1.4 billion in the plan.
The subsidiary runs one of LG ES’s existing factories in Holland, Michigan, US. Originally equipped with production lines for electric vehicle (EV) battery cells, the facility will be reconfigured to support mass production of energy storage system (ESS) cells.
LG ES Vertech CEO Jaehong Park spoke with ESN Premium in March about the retooling of three EV battery production lines, each of 5.5GWh annual capacity. Park noted that there were “not many major renovations required,” although the differing design of the cells, including the larger capacity and longer cycle life of cells for stationary storage applications, necessitated perhaps the most work.
The company began producing ESS batteries at the Michigan factory in early May, claiming to be the first facility in the US to produce LFP batteries at scale. An official event to celebrate the start of production was held 24 June at the site.
LG ES states that its factory has an average annual production capacity of 16.5GWh, with ESS battery modules and containers scheduled for production starting in August.
Additionally, LG ES will manufacture nickel manganese cobalt (NMC) cells for the Ford Mustang Mach-E, having recently transferred this production from the company’s facility in Wroclaw, Poland.
Other companies are working in domestic cell manufacturing as well.
Fluence has started using Tennessee-made cells supplied by AESC in roughly half of its US projects so far.
Additionally, the startup Our Next Energy (ONE) is manufacturing LFP cells in the US and can benefit from the 10% domestic content bonus.