Europe has an opportunity to establish the safest and most sustainable lithium-ion battery value chain in the world. Efficient reverse logistics would significantly decrease the carbon emissions in the life cycle of Li-ion batteries, however, there are major bottlenecks that first must be tackled.
Piotr Grudzień, innovation consultant at Bax & Company, proposes a 4-step plan to improve the efficiency of Li-ion battery reverse logistics in Europe.
Enjoy 12 months of exclusive analysis
- Regular insight and analysis of the industry’s biggest developments
- In-depth interviews with the industry’s leading figures
- Annual digital subscription to the PV Tech Power journal
- Discounts on Solar Media’s portfolio of events, in-person and virtual
The battery flood – a blessing and a curse
Li-ion batteries are revolutionising the world of energy, enabling the transition to renewables and electrifying transport. They help us lower carbon emissions, reduce dependency on depleting hydrocarbons, and clean the air in cities by decreasing the number of combustion cars on the streets.
Unfortunately, replacing fuel tanks with half-tonne EV battery packs and building megawatt-sized energy storage installations has not solved all issues and has instead produced new ones.
Most of these relate to the use of critical raw materials (CRM) like cobalt and lithium, which are crucial in battery manufacturing, but at the same time suffer from supply risks, such as human rights violations and contamination of the environment at mining operations.
Over 1,000GWh of new Li-ion batteries will be placed on the EU market by 2030, with roughly 10% of this capacity installed in stationary energy storage systems and the rest used for battery electric vehicles. In the face of skyrocketing demand, the scarcity of battery materials, and Europe’s high import-dependency rate, the industry has been urged to increase the recycling capacity for Li-ion batteries and therefore, provide a supply of secondary raw materials. With a lifetime of 10-15 years, batteries that are currently installed are expected to reach their end-of-life (EoL) and will have to be properly handled. In 2030 alone, there will be more than 110,000 tonnes (or 25GWh) of these batteries in Europe.
Building new recycling plants is only part of the solution though. Prior to recycling, the batteries will need to be collected, tested, transported, discharged, and dismantled. To portray the magnitude of the challenge, this means tens of thousands of heavy-duty trucks transporting EoL batteries every year.
That’s why a safe and efficient reverse supply chain is needed.
David and Goliath interplay
The reverse logistics of Li-ion batteries are characterised by an interplay between large enterprises (battery manufacturers, ESS and EV OEMs, recyclers) and SMEs (workshops, dismantlers, repurposers and traders) covering different steps, as presented in the visual below.
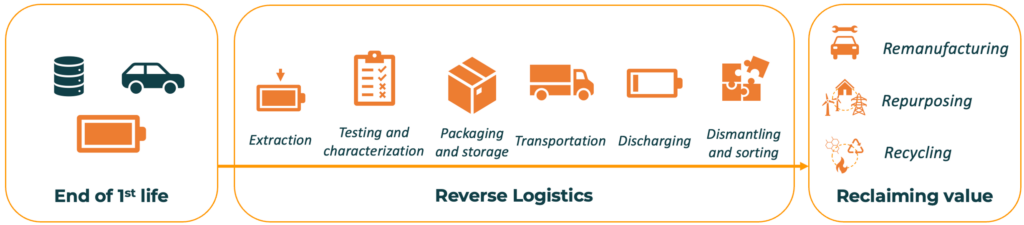
25 GWh of batteries to be treated in Europe annually is a business opportunity not to be missed. First of all, critical materials can be recovered and used in new batteries. In Europe this creates a market of over 1 billion euros in 2030, assuming all these batteries are recycled. Importantly, the batteries to be recycled come from two distinct sources: the manufacturing process (at least 5% of cells end up as production scrap) and EoL EV batteries, as presented in the chart below.
Because of this, all stakeholders mentioned above are currently scrambling to get a piece of this pie. Naturally, OEMs and recyclers have the biggest appetite. Manufacturers have the position of strength due to control over battery data, while recyclers have the highest industrial readiness to recover value from EoL batteries. On the other hand, SMEs (e.g., third-party workshops) are often indispensable, being the first point of contact for ESS/EV owners when their battery needs a repair or replacement.
Secondly, parts of EV Li-ion batteries can be repurposed and used in, for example, stationary energy storage applications (over 0.9 billion euros in 2030, assuming that roughly 40% of the batteries in Europe can be repurposed).
Some companies have taken up the reverse logistics challenge and started collaborating to combine the aforementioned strengths.
Nissan partnered with energy provider ENEL to deliver a 2nd life battery ESS to enhance grid stability in Melilla, Spain. Groupe Renault, Veolia and Solvay joined forces to recycle end-of-life EV battery metals using a hydrometallurgical process.
In South Korea, big battery players Samsung SDI, Hyundai Motor Company, SK On, and LG Energy Solution, have recently formed an alliance with seven SMEs to build the country’s first all-in-one battery reuse-remanufacturing-recycling business.
However, vertical integration efforts have also been recognised among some major OEMs. Volkswagen aims to ‘close the loop’ of the valuable battery materials with their first recycling plant in Salzgitter (Germany) and a network of 265 service stations with experts trained to handle faulty EV batteries.
Challenges to tackle and who can approach them
Despite these promising market developments, there are still some major bottlenecks to reverse logistics processes in Europe, which may be difficult to address by industry alone. First of all, the supply of EoL batteries is highly dispersed and unstandardised due to various battery types, preventing economies of scale in their treatment. This, in turn, leads to a time-consuming and labour-intensive disassembly process of batteries before they can be recycled, repaired, or repurposed.
Furthermore, the transportation of EoL batteries across Europe has a high procedural burden and is very costly (roughly 40% of the recycling cost), due to the strict safety requirements for packaging connected with dangerous goods regulations (ADR) and the low number of Li-ion battery treatment plants in Europe. Last but not least, the characterisation of ESS/EV batteries cannot yet be performed on an industrial scale due to the lack of common diagnostics protocols and limited access to BMS data by third parties.
These technical, regulatory, and market bottlenecks can be resolved with the help of research and technology organisations (RTOs), policy makers (e.g., the European Commission), industrial associations, and innovation actors.
The role of RTOs will be to advance the state-of-the-art of reverse logistics processes and related technologies, policy makers should ensure that enabling regulations and incentives are in place, industrial associations are best suited to foster collaboration between companies, and innovation actors will combine the strengths and contributions of all stakeholders into ambitious projects, pertinent to the industrial challenges and EU objectives.
Dire consequences of inaction
If reverse logistics do not become more efficient (= cheaper), there will be no incentive to achieve high reuse and recycling rates. Although recycling rates are expected to be increased by the New Battery Directive (from 50% of battery weight currently to 65% in 2025 and 70% in 2030), without technological advancements, the costs of battery treatment will surge.
This, in turn, can force OEMs (which are responsible for the treatment of the batteries) to increase the prices of their goods, slowing down the electrification of transport and indirectly the energy transition.
In such a scenario, we may need to shift from commonly used NMC batteries to other chemistries (e.g., cobalt-free) or technologies (e.g., hydrogen fuel cells). Although these new developments are highly anticipated, Europe has already invested a huge sum of money into the Li-ion battery industry, so it would be a strategic mistake not to ensure the long-term profitability of the value chain.
Another negative impact of inaction may be an uncontrolled capture of the EoL battery market by inexperienced third parties. Insufficient knowledge or lack of standardised tools and safety protocols may lead to the wrong treatment of Li-ion batteries and, consequently, to accidents (e.g., thermal runaway).
This is already happening – Li-ion batteries from damaged EVs have started popping up in online marketplaces and their buyers have no means to verify the state of health, nor the safety of the offered products. These buyers are often DIY enthusiasts (especially common in the UK and Norway), who build 2nd life residential energy storage systems and may unknowingly risk their own life or even their neighbours’.
Green opportunities at hand
Europe has an opportunity to establish the safest and most sustainable value chain for Li-ion batteries in the world. The development of efficient reverse logistics and recycling would significantly decrease the carbon emissions in the life cycle of Li-ion batteries.
Battery recycling can reduce the GHG emissions in the life cycle by 20 kg CO2 eq./kWh, which translates into a significant reduction of 10 million tonnes of CO2 equivalent – if all EV and ESS batteries produced in 2030 are recycled. This means an overall drop in EU emissions by 0.5%.
Customers and EV OEMs are increasingly aware of the social and environmental impacts of battery production, generating higher demand for more sustainable products. European companies delivering the greenest EV batteries can tap into this business opportunity and increase their competitiveness, especially in comparison to well-established Asian manufacturers. Moreover, the new 2nd life business models unlocked by developments in reverse logistics could lead to the creation of new jobs in the EU. Several start-ups are already arising in the fields of battery passport and trading (Cling, Circunomics), repurposing and stationary storage (Bee Planet Factory, Watt 4 Ever, Evyon). Currently, the operations of such start-ups are limited in Europe due to the lack of standardisation in regard to EoL battery testing, and no framework for battery repurposing.
A 4-step plan for reverse logistics in Europe
At Bax & Company, we have identified 4 areas which require the most attention to unlock the potential of Li-ion battery reverse logistics in Europe.
- New techniques for collection, transportation, sorting and second use should be developed. Increased safety, automatisation and standardisation are among the key objectives of these developments. They can be achieved through, for example, R&D&I projects under the EU HE framework (e.g., HORIZON-CL5-2022-D2-01-10), or private investments.
- Battery OEMs and ESS/EV manufacturers should break the silos and start sharing data from battery management systems with other stakeholders in the value chain. This would increase the efficiency of reverse logistics steps and enable new business models, including 2nd life applications. In a conservative and more likely scenario, OEMs could develop a network of authorised workshops with access to BMS data. The progressive solution would involve the open sharing of this data with any interested third party.
- The EU must provide a proper set of regulations and incentives for faster adoption of improved recycling and repurposing concepts. The New Battery Directive sets out increased recycling targets, novel tracking methods (battery passport) and a repurposing framework. Yet, the final shape of the directive is still under negotiations which are expected to finish either later this year, or in 2023. Hopefully, member states will not try to diminish the ambitiousness of the proposed directive and will be open to its fast implementation.
- Increased customer awareness and demand for repurposed or recycled batteries would encourage industrial players to invest in reverse logistics and offer more sustainable products. This can be achieved by raising the issue of battery circularity at events, through social media communication, and by introducing a clear labelling system that allows for the identification of a battery’s social and environmental impact. This is especially important for the growth of 2nd life ESS companies, which use the circularity of their products as a fundamental part of their value proposition.
Future-proofing the energy transition
The sustainable future of Li-ion batteries in Europe depends on the development of novel treatment techniques, the openness of key industry stakeholders, apt policy making at the EU level, and innovative business models. Now is the time to take action and get ready for the upcoming mass returns of batteries.
If we manage to solve the challenges of reverse logistics in Europe, the electrification of transport and the energy transition will truly become future proof.
Cover image: Lithium-ion battery pack designed for easy dismantling, reuse and recycling by UK startup Aceleron. Image: Aceleron.
About the Author
Piotr Grudzień, is an innovation consultant at Bax & Company, a European innovation consultancy working with corporate directors, entrepreneurs and policymakers to create, execute and manage cutting-edge science and technology-enabled initiatives that deliver substantial societal, environmental and economic impact.