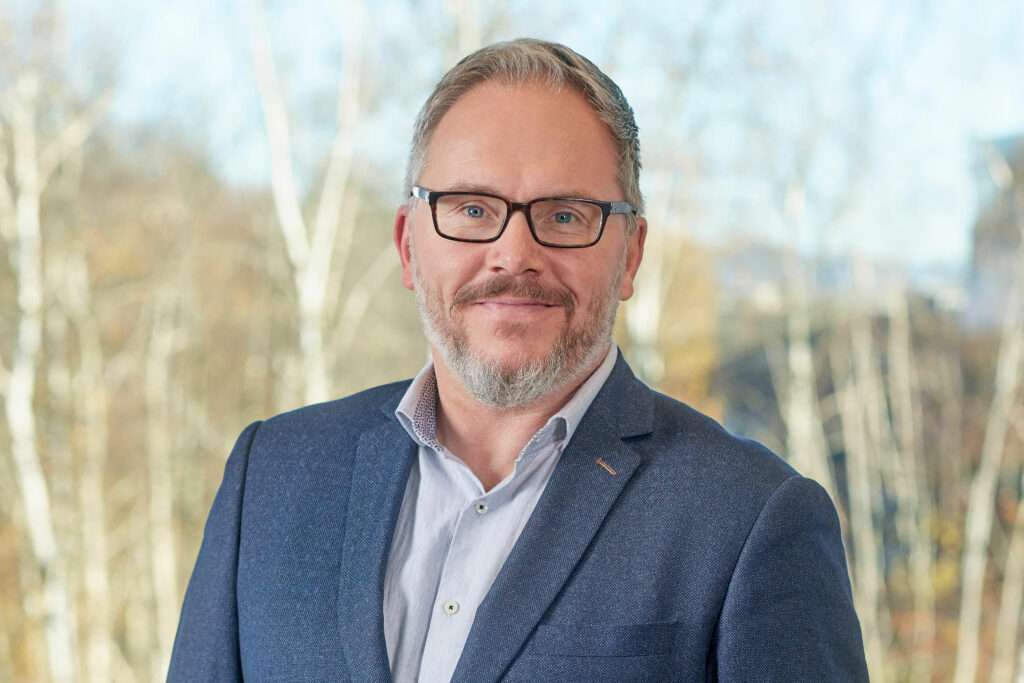
Norwegian lithium-ion gigafactory startup FREYR Battery could easily dedicate half of its 2030 production capacity target of 100GWh to energy storage and is also launching a system integrator play, CEO Tom Jensen has told Energy-Storage.news in an interview.
The company was founded in 2018 on three core tenets of speed, scale and sustainability. It has a massive lithium-ion gigafactory pipeline with the first four totalling 36GWh in Mo I Rana, Norway, going online in 2023-2025. But unlike many other players in the space, FREYR’s focus appears to lean towards energy storage as much as if not more than electric vehicles (EVs).
Enjoy 12 months of exclusive analysis
- Regular insight and analysis of the industry’s biggest developments
- In-depth interviews with the industry’s leading figures
- Annual digital subscription to the PV Tech Power journal
- Discounts on Solar Media’s portfolio of events, in-person and virtual
Energy storage focus
“We aim to have 83GWh of installed production capacity by 2028 and more than 100GWh by 2030, and I would say that based on what we see now, we believe that we might easily dedicate half of that to the energy storage system (ESS) market,” Jensen said.
He explained that the technology it has licensed from the US company 24M to build its batteries is highly suited to storage applications because it contains more energy-carrying material. (You can read an interview Energy-storage.news did with 24M’s management team about its technology here.)
FREYR is therefore targeting all segments of the ESS market and could theoretically dedicate even more than half of capacity to the sector, Jensen said: “We believe that the (storage) market is growing much faster and going to be much bigger than most people think so we could in fact dedicate all our production capacity to energy storage, if we wanted to.”
“But we’re also getting quite a lot of interest from mobility and EV players, so the exact fraction (of production capacity) is going to be a function of multiple different ongoing discussions. But the technology we have and our positioning in the ESS space makes us a leading provider of ESS solutions using decarbonised battery systems, and we will obviously try to capture as much of that market as possible.”
System integrator play
The emphasis on storage as a target market is clear from the fact its two major announced offtake agreements have both been in that space. Technology group Honeywell will buy 19GWh of batteries from FREYR between 2023-2030 while a second, unnamed partner will purchase 31GWh in the same period in a partnership that will see FREYR contribute to a system integrator play.
“Once finalised, we believe that these two initial offtake agreements may take the bulk of our first gigafactory’s capacity (operational in 2023) for the first four to five years,” Jensen said.
“We expect to enter into a joint venture with the unnamed partner for developing full containerised solutions, which will basically be the final product including BMS (battery management system) and everything. That will effectively be a system integrator approach together with that partner.”
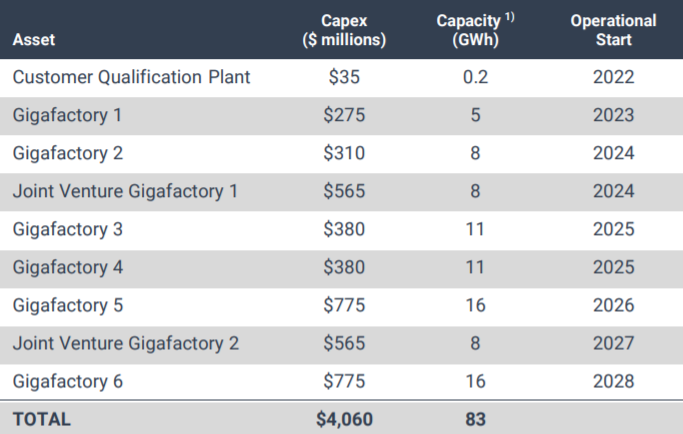
Jensen also touched on three massive topics of discussion in the BESS space but also the wider battery ecosystem: the lithium iron phosphate (LFP) versus nickel manganese cobalt (NMC) debate, current supply chain issues with lithium battery materials, and sustainability, one of FREYR’s key tenets.
LFP vs NMC
LFP cathode-based batteries are growing in adoption by the energy storage industry thanks to a lower fire risk and fewer ESG concerns around its materials’ supply chain than the NMC market standard.
“Our technology platform is chemistry flexible. In the first facility, we’ll produce LFP only because the customers demand it, and we see a lot of automotive stakeholders are increasingly interested in LFP,” he said.
“We do also have an ambition and customer interest for NMC based materials or high nickel content materials. But to the extent we use cobalt, it will be responsibly and sustainably sourced through our partnership with Glencore.”
He pointed out the lower energy density for LFP compared to NMC doesn’t really matter in an energy storage context where cycle life is king and for which the 24M technology also has benefits thanks to the ability to make larger cells.
Supply chain and new financing
The discussion then moved on to global supply chain issues which have temporarily caused LFP battery cathode prices to reach parity with NMC ones for the first time, or even surpass them according to other sources.
“What we’re seeing now are temporary bottlenecks that are challenging, of course, with the near-term pricing, but we’re in dialogue with our customers and aim to have relevant commercial arrangements that allow us to pass through some of those raw material price increases if they reach certain thresholds.”
“I think everyone who’s building anything in the world today is subjected to the same challenges. So relatively speaking, things will become more expensive but the relative cost advantages of this technology are still the same.”
He suggests that FREYR’s capital requirements might have increased since a year ago but that any necessary additional financing – it has a market cap of over US$1 billion since a SPAC merger listing in July last year – would draw on strong interest and an increasing understanding from governments and capital markets about storage’s role in the energy transition.
Sustainability
As alluded to earlier, sustainability is one three tenets upon which Jensen said FREYR was built, along with speed and scale. “We have the ambition to produce the world’s cleanest or greenest batteries,” he said.
“Our initial ambition is to have by 2025 an 80% reduction in CO2 footprint on a lifecycle basis for the batteries compared to conventional lithium-ion batteries today, and then over time we aspire to a net zero ambition. How fast we get there depends on how fast we can mitigate the harder to abate parts of the value chain.”
Norway is one of a handful of countries with 100% renewably energy thanks to an abundance of hydroelectric power. Jensen said that FREYR’s production power needs, which will be 60% lower than conventional lithium-ion production, will be serviced by “almost completely renewable hydropower but also a little bit of wind”.
“In addition, we plan to selectively partner and invest upstream, meaning input materials that go into battery cell manufacturing. A very large part of the CO2 footprint of the battery comes from the way in which the materials are produced, so if we really are serious about decarbonizing the battery itself, we need to get these materials to be produced in areas with renewable energy and we want to be a catalyst in this regard.”