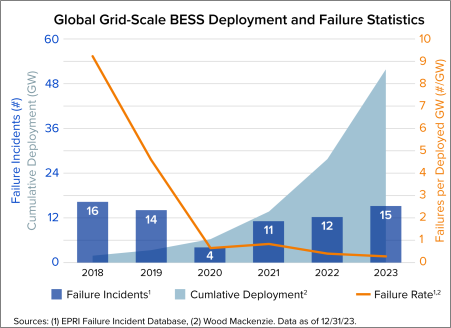
Fire safety should always be the BESS industry’s top priority and there are effective steps to achieve it, writes Angus Moodie, engineering manager at consultancy Enertis Applus+.
Fire incidents involving battery energy storage systems (BESS), although they are of relatively very low occurrence, easily capture the attention of the public and authorities as this is a relatively new technology and because the failure produces dramatic images and potential lasting effects to neighbours, first responders, and the local environment.
Enjoy 12 months of exclusive analysis
- Regular insight and analysis of the industry’s biggest developments
- In-depth interviews with the industry’s leading figures
- Annual digital subscription to the PV Tech Power journal
- Discounts on Solar Media’s portfolio of events, in-person and virtual
Although failure incidents are decreasing (as shown in Figure 1 above), each incident gives an opportunity for investigations to be carried out and for the industry and authorities to learn a little more about how to improve the safety of these systems.
However, relying mostly on the learning gathered after incidents occur is a lagging method and inherently standards have been behind the deployment of the technology, which evolves at a much rapid pace. While it is true that standards and legislation should be taken as baseline for the design, construction, operation, and dismantling of BESS systems, we should not stop there.
Implementing a comprehensive risk management hierarchy that takes into consideration all relevant variables is a best practice that is essential to ensure the safety of BESS installations. An analysis of what happened at the Moss Landing Energy Storage Facility in California in January, together with a comparison of current standards and methods, can illustrate this point.
Elimination strategy
Elimination means removing potential fire hazards from the design and operation of BESS installations. Project developers and owners should ask themselves a crucial question: is it absolutely necessary to introduce a storage technology that will present a fire hazard?
In some cases, BESS project may only be viable with the properties of lithium-ion storage systems, and it must be recognised that this decision introduces the fire hazard to your project. If another technology was selected, the steps discussed below would require to be adjusted according to the technology selected, to the point of even being avoided entirely or, at least, reduced significantly.
Substitution strategy
Substitution involves using safer materials and technologies when designing battery cell composition to minimise fire risks. Lithium iron phosphate (LFP) has a lower risk of thermal runway compared to nickel manganese cobalt (NMC). Even if the cells used in a given project are tested to the established standards, compliance with those standards does not fully eliminate the possibility of fire incidents.
Engineering controls
Engineering controls involve the implementation of systems to control fire hazards, such as physical barriers and fire suppression. This is where most of the effort to minimise the likelihood and severity of any fire incident is placed, once the two areas described above have been defined.
Battery manufacturers are responsible for implementing the battery management system (BMS) to manage the state of the cells to keep them healthy, protect them and detect abnormal situations. The cooling systems will keep the cells in their safe operating conditions.
If a thermal runaway occurs, then their cell and module design, as well as fire detection and suppression systems, will reduce the impact of the fire, and gas detection and ventilation systems can act to prevent explosion events.
Nowadays, BESS cabinets and containers limit the spread of fire for at least one hour. The containers for the BESS modules allow for the containment and build up of concentrations of gases or smoke particles so that a fire detection and suppression system can function correctly.
These features are mandated in standards internationally and the level of fire and gas detection, suppression or ventilation, as well as the control decisions around operation of the site in these conditions, are key considerations in any design.
The next level of engineering controls is protecting the BESS from outside influence introducing faults that result in thermal runaway. In particular, the electrical protection of the system is key to avoid electrical system faults influencing the BESS. Appropriate care when selecting the right protection scheme and devices is pivotal to reducing the risk to the project.
The next area of review is the site layout, which plays a key role in managing the severity of fire consequences. While standards provide prescriptive guidelines for site layout implementation, the risks that are being addressed are not always explicitly stated in the documentation.
Main risk areas associated with this type of projects are:
- Constrained access to BESS equipment and areas of the site blocked by fire or other objects;
- Access to BESS equipment through the smoke path of the fire;
- Fire spreading from one unit to another, and/or the wider environment.
Some suggested solutions in standards and guidelines include:
- Provide multiple access points to the site;
- All roads should be suitable for fire-service vehicles and their turning circles;
- Access paths should be wide enough and with turning circles for multiple fire-service vehicles to be operating around the site at the same time;
- Passing places on access paths for fire-service vehicles;
- Orientate the access points away from prevailing wind direction;
- Inclusion of break points between rows of batteries to allow vehicles or personnel to pass through and limit the spread of fire;
- Minimum distances to other BESS/buildings/vegetation or other flammable materials or sources of fire, and the use of fire rated barriers when these distances cannot be met.
Manufacturers are now conducting large-scale fire testing (LSFT) as outlined in standards such as CSA TS-800. These tests help assess the likelihood and severity of fire events and they can be presented to authorities when discussing fire safety measures and site layout decisions. This testing evidence is crucial for fire risk assessment and management strategy, informing both the engineering controls and the administrative controls.
Administrative controls
Administrative controls are the policies and procedures established to manage fire risks effectively. This level of risk management is there to manage the residual risk once all the above measures have been implemented. These controls should be informed by the design and the residual risk left for the future user of the BESS installation.
It is often best to complete these administrative controls in consultation with your local fire authorities as well as the operations and maintenance services provider at the earliest possible stage of the project. They will provide feedback on these controls and the design that would further reduce the risk to their personnel and make the response actions more robust.
If the steps above are followed diligently to address the fire safety risks beyond the baseline given in standards and legislation, these potential cases will be even rarer than they are today. It may seem like an extra cost or effort that is not worth it, but it could just keep a fire incident small, preventing it from becoming a severe incident.
About the Author
Angus Moodie, is engineering manager for the UK & Northern Europe at Enertis Applus+, a provider of technical consulting, engineering and quality control services in the renewable energy and energy storage sector. Moodie has experience in product and system design, including energy storage systems and power systems and is a chartered member of the Institution of Engineering and Technology (IET).