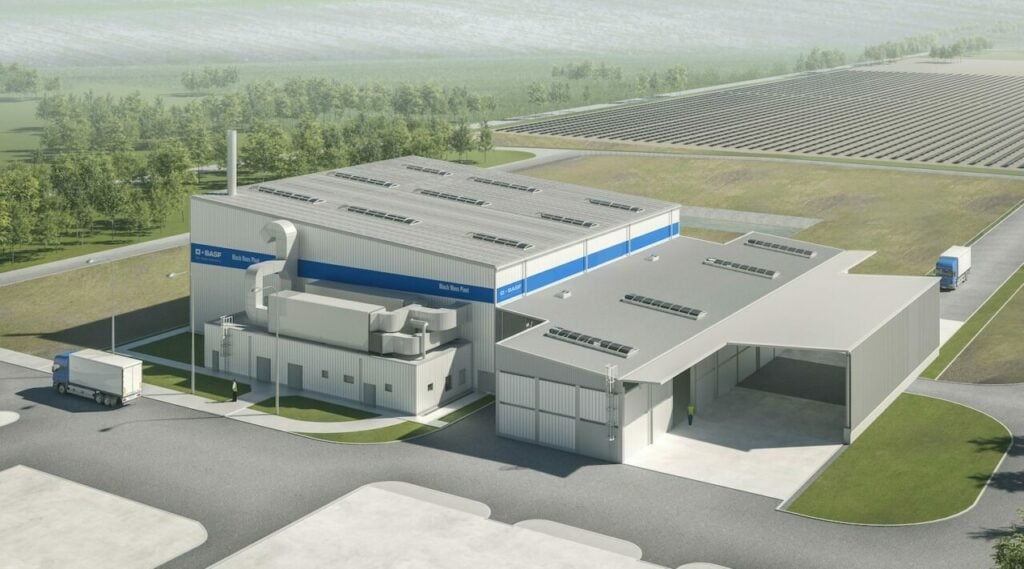
Metals group BASF has begun commissioning on what it claimed is the first combined battery cathode materials production and recycling plant, in Germany.
The facility, located in Schwarzheide, Germany, is the first production facility for lithium-ion cathode active materials in Germany and the first fully automated large-scale one in Europe, BASF said. A spokesperson told Energy-Storage.news that the production facility is now undergoing commissioning, while the recycling operations will come later.
Enjoy 12 months of exclusive analysis
- Regular insight and analysis of the industry’s biggest developments
- In-depth interviews with the industry’s leading figures
- Annual digital subscription to the PV Tech Power journal
- Discounts on Solar Media’s portfolio of events, in-person and virtual
“Phased commissioning of the cathode active materials plant in Schwarzheide is ongoing. The plant is fully sold out for the next years and will supply products tailored to the specific needs of cell manufacturers and automotive OEMs in Europe. BASF plans to fully utilise the plant within a year,” a spokesperson for the firm said.
The plant will also, starting in 2024, process end-of-life batteries and scrap from battery production into black mass, the industry term for the shredded material containing the key, high-value metals for batteries, mainly lithium, nickel, cobalt and manganese.
The output from the black mass plant in Schwarzheide will be processed by a commercial hydrometallurgical refinery for battery recycling that BASF plans to build in the coming years in Europe, they added. Until BASF´s own commercial scale refinery is in operation, BASF will sell the produced black mass to third party refiners.
Hydrometallurgical refinery is a significantly higher capex activity than black mass production and some companies entering the recycling space, like Sweden-based Stena, are only doing the latter.
The inauguration came a fortnight after the EU voted to adopt a new suite of standards and requirements around battery production, the so-called Batteries Regulation. This includes a minimum level of material to be recovered from waste batteries and minimum levels of recycled content to be used in new batteries, detailed in our coverage.
Maroš Šefčovič, European Commission vice president for inter-institutional relations and foresight, attended the inauguration event for the facility last week, along with Michael Kellner and Dr. Robert Habeck from Germany’s Federal Ministry for Economic Affairs and Climate Action (pictured below).
Commenting on the plant, Šefčovič said: “The EU battery market is rapidly growing. Demand for batteries is expected to continue to increase drastically in the coming years for both mobility and storage, and our competitors are also pursuing this market. In this context, the European Commission is committed to keep building a solid battery ecosystem in Europe.”
“This is why we have created the European Battery Alliance (EBA), which has helped to generate more than €180 billion in private investments so far. The BASF plant benefited from this work. With its focus on advanced cathode active material and on recycling, it demonstrates that we can boost the EU’s competitiveness and reduce its dependencies in a strategic sector, and accelerate the green transition.”
The EBA recently called for more action to prevent an outflow of investment from Europe’s battery ecosystem, with companies increasingly making plans in the US to capitalise on generous tax credit incentives for battery production (which Šefčovič appeared to allude to).
The battery area manager for Stena, which opened a black mass production plant earlier this year, recently told Energy-Storage.news that battery production scrap accounts for the bulk of recycling content today. This would only increase as the continent ramps up its cell production capacity, and that end-of-life EV batteries would only become the majority towards the end of the 2030s.
In related recent news, the recycling JV arm of European lithium-ion gigafactory company Northvolt recently secured a small grant totalling around US$1.5 million from the Norwegian government to develop a discharge and dismantling technology for batteries. The funding from state agency Enova builds an earlier, roughly US$4 million grant it received from the agency for its plant in Fredrikstad last year.
BASF also has downstream energy storage activities through a partnership with Japan-based NGK Insulators around a sodium-sulfur (NAS) battery product, most recently deployed in Australia.
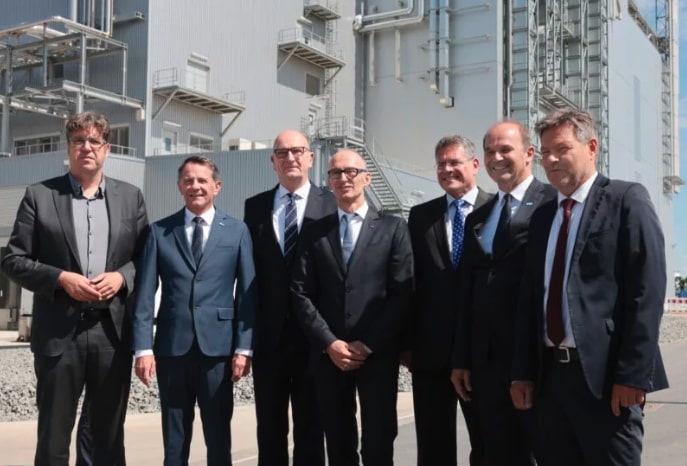