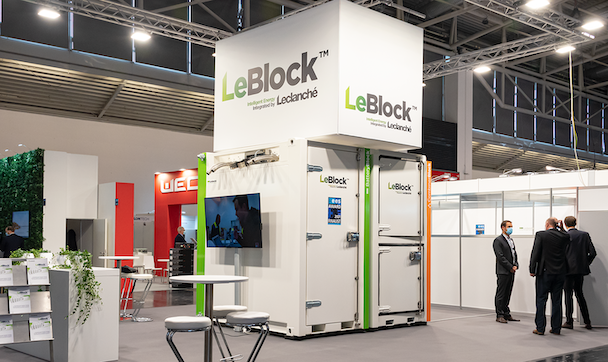
Recent battery incidents have made the news. For this reason, the topic of safety has re-emerged as a critical factor in selecting an energy storage system. Given numerous market alternatives, it is our belief that a proper search should lead buyers to the safest choices.
In designing Leclanché’s new LeBlock modular stationary solution, our engineering team spent years studying and comparing all the possible architectures and options. We’ve distilled some of that learning here to assist you in making an informed choice when planning a battery installation and ensuring you’ve considered the safest options.
Enjoy 12 months of exclusive analysis
- Regular insight and analysis of the industry’s biggest developments
- In-depth interviews with the industry’s leading figures
- Annual digital subscription to the PV Tech Power journal
- Discounts on Solar Media’s portfolio of events, in-person and virtual
1. Choose the right battery cell
In terms of safety, we differentiate primary safety (what can be done to prevent incident occurrence) from secondary safety (how to better control and manage hazards once an incident is underway). Primary safety is directly linked to the cell itself.
There are different kind of battery cells; each with its advantages. But the most important to consider is that the cell is compliant with the IEC62619. As mentioned in its title, “Secondary cells and batteries containing alkaline or other non-acid electrolytes – Safety requirements for secondary lithium cells and batteries, for use in industrial applications,” this standard is dedicated to the safety of the cells.
2. Ensure safe integration of the module, rack and containers
For modules and racks: Make sure the battery meets the UL 1973 and IEC 62619 standards.
Selecting a battery, which is UL9540A approved, means the system has been tested, simulating a thermal runaway incident, to check that the fire doesn’t propagate.
As a 110-year old battery manufacturer, Leclanché has strong experience in battery integration taking into account mechanical, thermal, electrical and safety constraints. All systems for marine, transportation or stationary applications go through an extensive testing and qualification process.
3. Invest in the right battery management system and energy management software
Using safe and standard compliant components is the mandatory first step to ensure the highest possible safety level; however, how the battery is used is key too. That’s why the battery management system (BMS) should ensure that the battery is not pushed beyond its limits. To provide this functional safety, the BMS must be certified according to IEC61508, the standard for functional safety of electrical/electronic/programmable electronic safety-related systems.
The BMS generates a huge amount of data that are read by the energy management software (EMS), saved locally and regularly backed-up to a secure cloud system. All these data can be used for analytic purposes to detect possible battery misbehaviour or deviations at an early stage as well as optimise system operation.
4. Partition to better contain incidents
Dividing the energy storage system and partitioning the battery system in solid enclosures helps to prevent a fire incident from spreading to an entire site.
LeBlock is Leclanché’s new, safe, modular, scalable, plug & play energy storage solution. It has been designed to simplify logistics and reduce total costs and carbon footprint.
With LeBlock, battery modules are placed in compact enclosures based on robust container technology. This helps to contain a potential fire within each block.
The enclosures are highly fire resistant, providing the thermal insulation needed to minimise the auxiliary energy consumption to maintain the battery at a certain temperature – typically between 20 and 23°C– independent of the outside temperature.
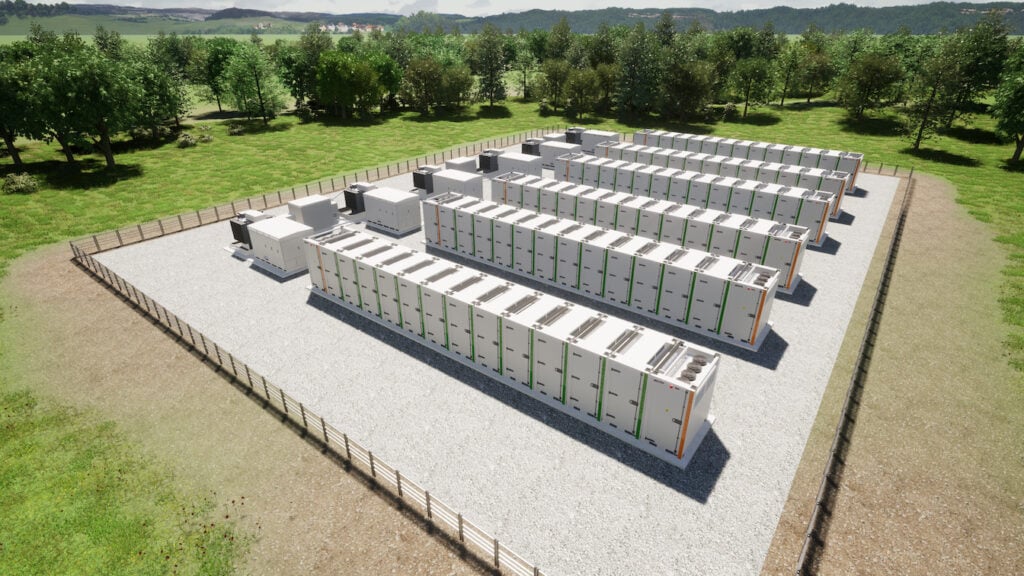
5. Selecting an adequate fire detection and suppression system
Whereas partitioning provides a passive way to improve safety, there are some active ways to fight fires. The goal of a fire suppression system is to prevent a non-battery fire from reaching other cells in the block – preventing a small incident involving a few batteries from turning into a large-scale fire whose consequence could be the replacement of the entire container – or worse, an entire site. A standard fire detection and suppression system consists of smoke and heat detection sensors integrated, with automatic activation, into an aerosol extinguishing system.
6. Keep staff safe with deflagration panels
The safety of personnel is key. Even if a site is secured, employees will be working nearby for maintenance and routine system checks. They could be standing next to a battery block when a fire or explosion takes place. In order to protect their safety, a deflagration panel enables the force of any internal pressure to be directed upwards. It ensures that people who are working in the area are protected from sidewards explosions.
LeBlock is equipped with deflagration panels compliant with NFPA 68.
7. Provide first responders’ action plan
The correct behaviour of first responders in the event of an incident is not always clear and may vary by system and local conditions. Therefore, it is important to develop a site-specific emergency action plan and provide training in cooperation with local first responders.
During an incident, the LeBlock enclosure should remain unopened until its temperature reaches a non-critical range, while the immediate environment should be monitored and cooled if necessary.
8. Implement an ’emergency stop’ function
Battery systems must shut down immediately for a controlled shutdown if a safety issue or battery anomaly is detected by the EMS, the BMS or any other safety device. It is also important to have a manual ‘emergency stop’ that can be performed by operators or first responders.
9. Detect electrical isolation failure
Most batteries are “floating” meaning that each polarity is isolated from the ground. An advanced insulation monitoring device compliant with IEC 615557 must ensure that there is no degradation of the insulation or short circuit to the ground. The granularity of the isolation measurement should be small enough to ensure good measurement accuracy and limited to a small number of batteries that will be disconnected via the emergency stop function.
In the LeBlock architecture, each Combi Block has its own isolation monitoring and can automatically detect an isolation failure and disconnect the batteries before a serious problem can occur.
10. Make sure your system complies with critical safety standards such as IEC and UL
In the USA, energy storage systems need to comply with NFPA 855 to mitigate potential hazards.
In the IEC world, the system must be designed according to IEC 62933, part 2, safety requirements for grid-integrated energy enhancement systems.
LeBlock’s design and construction has been validated by DEKRA to comply with UL9540, NFPA 855 and IEC62933.
11. Ensure the system has disconnections units
In order to be safe, a system must be equipped with all the necessary disconnection units, such as a load break switch, to ensure safe isolation for maintenance operations.
12. Make sure the system complies with electrical safety standards such as IEC 60364 or article 706 of the NEC in North America
Check to see whether all relevant IEC and UL electrical safety installation standards are adhered to – especially those protecting the installation against short circuit between polarities – with an advanced fusing system.
13. Transport the system safely
Lithium batteries are identified as a Class 9 dangerous good for transportation. The battery system must be tested according to the UN38.3 standard to be transported by air, sea, rail or roadways.
The LeBlock system is UN38.3 certified to be transported fully populated to its operational location. At the end of system life, the certification is still valid to transport the battery blocks directly to the appropriate recycling point without any additional packaging.
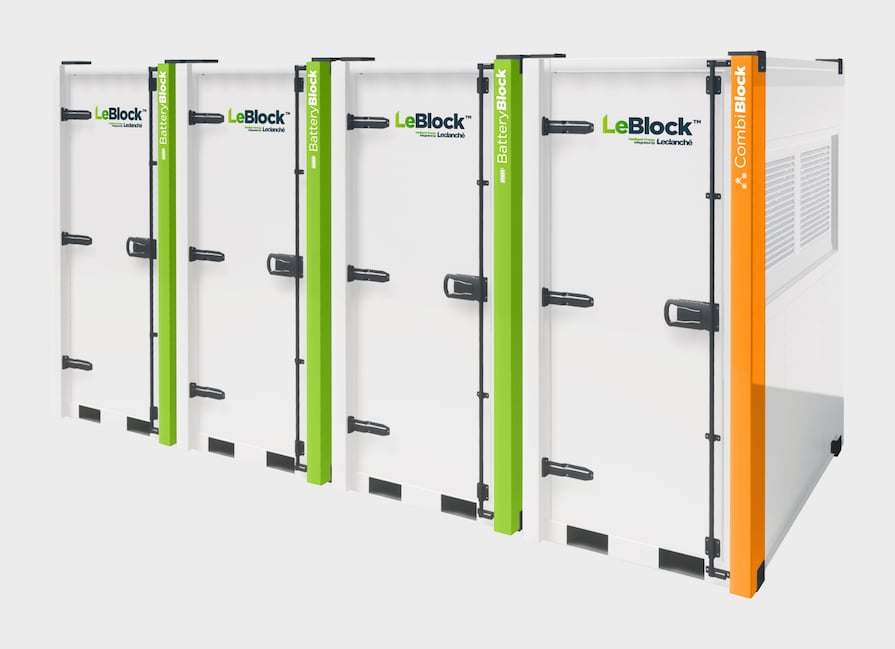