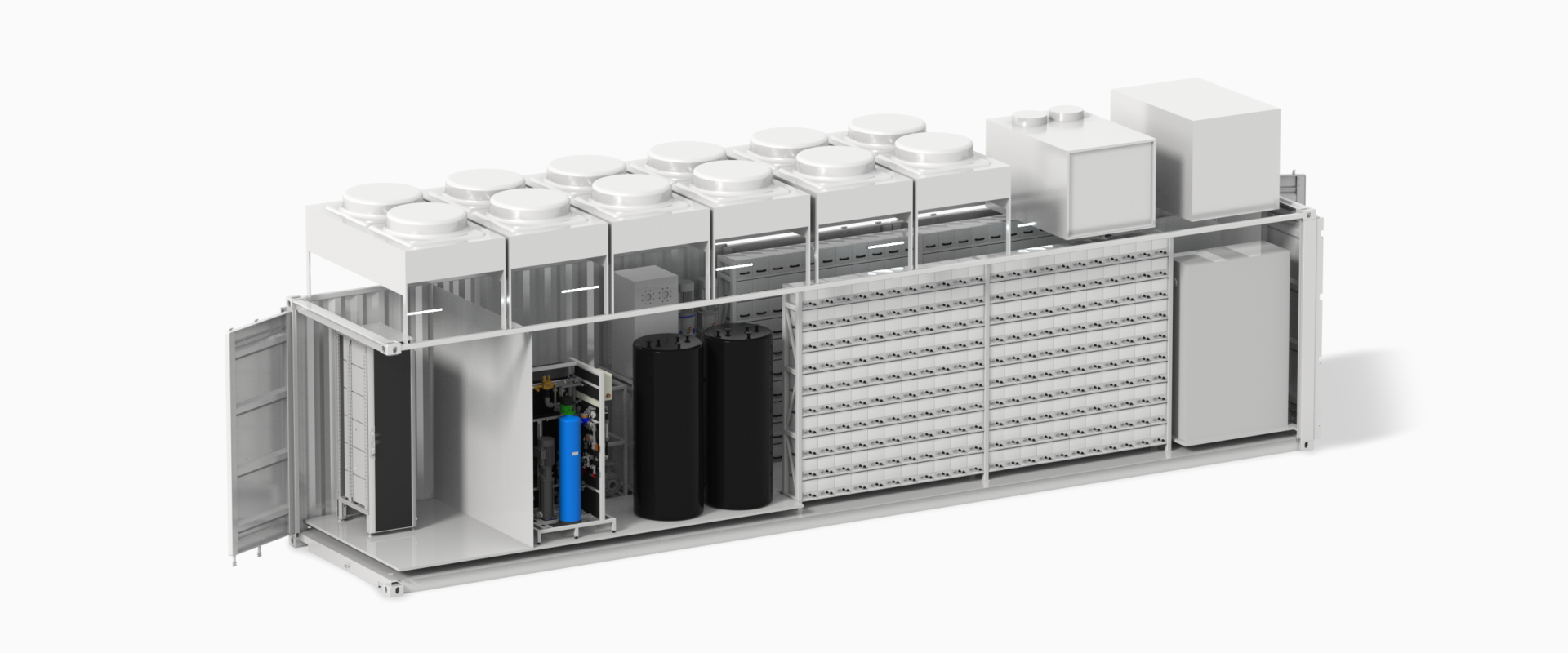
Australian flow battery energy storage company Redflow has entered a “high voltage, high capacity grid-scale future,” unveiling a new system it has created to be deployed at a 2MWh project in California.
Redflow makes redox flow batteries based on a zinc-bromine electrolyte chemistry which are intended to be durable with long lifetimes and capable of performing many cycles without degradation. With the batteries also capable of storing upwards of six hours of energy, the company has so far sold systems to a mixture of large residential customers and commercial businesses in its homeland as well as renewable off-grid microgrid projects and telecommunications operations in locations including Thailand and New Zealand.
Enjoy 12 months of exclusive analysis
- Regular insight and analysis of the industry’s biggest developments
- In-depth interviews with the industry’s leading figures
- Annual digital subscription to the PV Tech Power journal
- Discounts on Solar Media’s portfolio of events, in-person and virtual
A few months ago it was awarded a contract to install 2MWh of its battery storage at a waste-to-energy facility in California, the company’s biggest single project to date. Redflow’s individual battery systems are 10kWh each and the Rialto Bioenergy Facility project will see around 192 of them installed as part of a microgrid setup which will help the facility’s owner, Anaergia, to reduce its dependency on grid electricity at peak times.
Redflow this week unveiled Energy Pod Z, an energy storage module which integrates 16 flow battery storage units with power electronics including bi-directional DC voltage power converters supplied by German company TRUMPF Hüttinger. With Redflow batteries operating at 48V, the power conversion system (PCS) takes that up to 800V – 900V with each pod capable of 600kW output.
Not only is the solution designed to take Redflow to its first US deployment, it is also “really the foundation for us to go into large megawatt-hour systems,” Simon Hackett, a noted Australian tech entrepreneur who is the company’s systems integration architect and its largest shareholder, said.
“We’ve got a pod that has got 16 of our batteries and a set of advanced electronics that take that system, take that battery voltage, and bring it up to the high voltage that’s needed for grid-scale applications,” Hackett said.
“We believe using power converters from TRUMPF Hüttinger will help us in the emerging long-duration energy storage market,” Redflow CEO Tim Harris said.
“The fact that a global industrial company such as TRUMPF Hüttinger has invested in a product that is designed specifically for flow batteries is a significant validation of the growing role that flow batteries are playing in the energy storage market.”
The need for long-duration energy storage is expected to increase around the world in the coming years as renewables integration needs go beyond a few minutes of power to stabilise the grid or up to about four hours of energy to mitigate evening peaks. This is perhaps most acutely being felt in California, where state policy goals for 100% renewable electricity sales by 2045 as well as its need to make up for capacity shortfalls as ageing fossil fuel and nuclear plants retire make it one of the first markets in the world to begin putting market and system value on longer durations of storage.
Hydrogen tech company Enapter also stacking modular systems to megawatt-scale
Also scaling up a modular solution to the long-duration storage question with a new grid-scale product launch this week is Enapter, a maker of Anion Exchange Membrane (AEM) electrolysers for hydrogen.
Berlin-headquartered Enapter, which also has offices and production and research facilities in Thailand and Italy has been building small-scale modular electrolyser units with its proprietary technology that it claimed could bring down the cost of green hydrogen much more rapidly than rival tech. The company was last year named as a partner on an Australian government-supported pilot project to make renewable methane powered by solar PV using its modular electrolysers.
The Enapter AEM Multicore product which the company wants to make available next year will feature 440 electrolyser core modules stacked to produce nearly half a tonne of hydrogen per day. It is intended as a cheaper alternative to large-scale megawatt-class electrolyser systems.
In early 2020, company head of operations Jan-Justus Schmidt explained in an interview with Energy-Storage.news that the AEM technology could make hydrogen “much cheaper than fossil fuels in many applications”.
“There’s two established technologies currently: traditional alkaline systems and more advanced proton exchange membrane systems. Both of them have disadvantages. The alkaline system normally can’t operate at pressure, it doesn’t produce high purity hydrogen, so it needs a complicated balance of plant for the purification and compression steps later on.
“Whereas the PEM system produces high purity hydrogen directly from the stack and it has a very fast operation and so on, so it has advantages but it operates in an acidic environment so they rely on very expensive materials like iridium and platinum, titanium, which are required to make it work. With the AEM technology, essentially the cells set up like with the PEM. We have the advantages of the PEM but with low-cost materials of the alkaline systems,” Schmidt said.