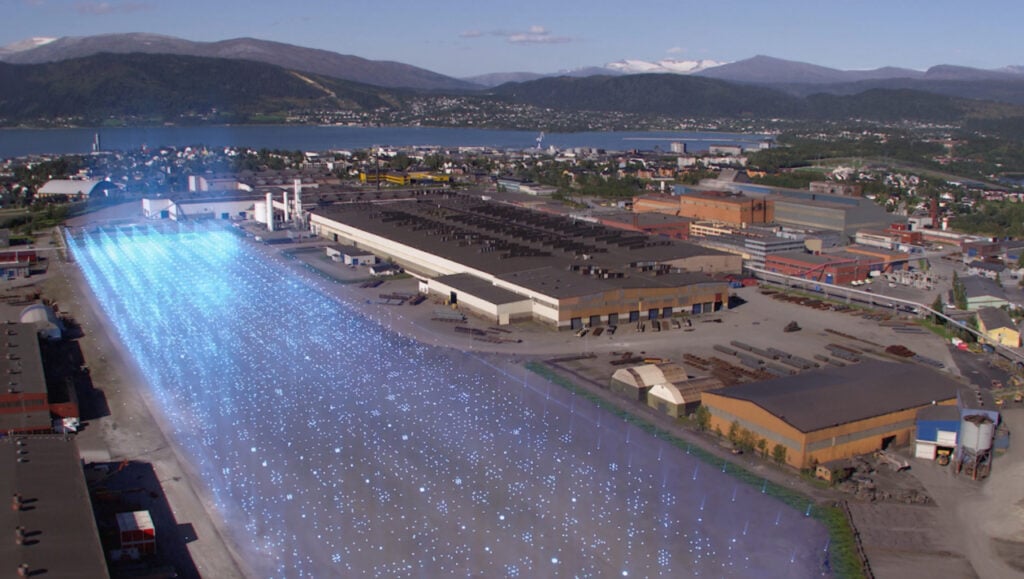
ESN Premium speaks about the upstream market landscape for Europe’s energy storage industry with Kevin Shang, analyst at Wood Mackenzie.
“This year, 2025, will be a crucial year for the whole European battery industry to re-evaluate its strategy,” Kevin Shang tells us.
Enjoy 12 months of exclusive analysis
- Regular insight and analysis of the industry’s biggest developments
- In-depth interviews with the industry’s leading figures
- Annual digital subscription to the PV Tech Power journal
- Discounts on Solar Media’s portfolio of events, in-person and virtual
“Because in the past few years, we have seen a lot of people put a lot of hope on homegrown battery startups, but they have met various challenges.”
We are speaking at the Energy Storage Summit EU 2025, which took place in London, UK, last month. Shang analyses the upstream end of the sector, focusing on manufacturing, supply chain and technologies.
He participated in our interview alongside his colleague Anna Darmani, who works on policy, regulation, and market conditions at the downstream end, for the EMEA region.
In our interview with Darmani, published last week on ESN Premium, we heard about the market conditions that make or break opportunities for developers and investors in Europe.
Meanwhile, Shang discusses the shifting sands of the supply chain and what customers in Europe are demanding from their battery storage suppliers and system integrators.
We cover topics like the challenges facing domestic battery manufacturing, how rising labour costs and transformers are the major cause of bottlenecks and why supply chain decision-making is becoming more complicated.
We avoid discussing politics directly, but the spectre of geopolitical tension between the US and China is never too far away from conversations in any global industry today. Battery storage is no exception, given its heavy reliance on Chinese production and technology development.
‘The devil is in the details for manufacturing’
Not long ago, analysts were producing maps and infographics showing Europe, peppered with planned lithium-ion gigafactory sites in development.
Then, to cut a long and complex story very short, factors including Joe Biden’s Bipartisan Infrastructure Law and Inflation Reduction Act legislation turned heads and put the US in the spotlight for battery manufacturing growth in the West.
At the same time, electric vehicle (EV) demand has not grown as quickly as the industry had hoped across Europe, further dimming investment appetite.
To give two of the most prominent examples, Sweden-headquartered Northvolt—considered a frontrunner among homegrown startups—entered bankruptcy protection proceedings.
Norway’s Freyr Battery, which was a little further behind Northvolt in its journey, exited the space altogether, rebranding as a solar PV manufacturer and moving its headquarters to the US.
Establishing the US as a hub for battery manufacturers has not exactly gone to 100% plan either, with recent high-profile setbacks such as the cancellation of startup Kore Power’s gigafactory complex in Arizona, with the acquired plot of land up for sale.
“Battery manufacturing is not that easy because it consists of so many processes, and the devil is always in the details,” Shang says.
“Another thing is the volume. Customers ask for a huge amount of batteries. How are you able to ensure that the quality and performance of the battery products is consistent? At the same time, you have to control the cost structure, because currently, battery prices from Chinese companies are so competitive.”
Indeed, recent research from Wood Mackenzie’s rival BloombergNEF noted that turnkey battery energy storage system (BESS) costs are less than half in China of what they are in the US or Europe. That’s even considering that BESS supplied in the US and Europe is made in China and exported to those end markets.
The US and Europe are also putting more emphasis on the ESG performance of batteries and their manufacturers.
“How are you able to deal with so many things at the same time? It’s not easy,” Shang says.
It is “sad to see so many setbacks for startups,” the analyst says, and 2025 will therefore likely be pivotal for the future of the industry, but he reminds us that currently, in Europe, battery manufacturing construction is still more focused on EV demand than battery storage.
Amid the debate in Europe about what its position should be on manufacturing, Shang says some Chinese companies are reluctant to put factories in Europe because they are unsure of the long-term demand dynamics. The energy storage system (ESS) market continues to grow but is still dwarfed by electric vehicles in size.
Europe’s long-term industrial policy needs
Since our interview was recorded in February, the European Union (EU) has launched its Clean Industrial Deal and Affordable Energy Action Plan package, pledging more than €100 billion (US$105 billion) to support the renewable energy and storage ecosystem. It remains to be seen how impactful that can be in moving the needle.
Shang says European Commission (EC) industrial policy announcements are highly anticipated, especially as supply chain decision-making has become “more and more complicated,” further impacted by US-China trade frictions.
One big change Shang has observed since our last interview at the EU Summit a year prior is that similar concerns are emerging in Europe around issues that have affected the US industry.
“European companies still rely on the batteries or the hardware part of the energy storage products from China, but I see more and more concerns about the non-hardware parts, such as software, from Chinese companies,” Shang says.
The US has been going much further in that already, and the analyst says he has heard of US companies importing battery storage products from China and then throwing away everything except the batteries.
“They get rid of everything else, such as software, and because of various concerns, nowadays, I do see an increase in similar concerns starting to appear in Europe.”
In the US, the primary motivation is that projects that utilise domestic content get higher tax credit incentives on a sliding scale once over a percentage threshold. Cybersecurity concerns and increasing protectionism since Donald Trump took office also look to have a bearing on US procurement strategies.
Biden had already committed to raising tariffs on Chinese battery imports from 2026 to 25% from 7.5% during his term, although obviously, Trump’s actions since taking office have been far more aggressive. Wood Mackenzie’s data shows a significant uptick in imports during 2024, and Shang says he visited China last year and saw the situation first-hand.
“People [in China] knew that the election was on the way and knew that no matter who would be on the stage, it would be more unfriendly to Chinese companies. They told me that: ‘For this year, our target is to just produce as much as we can and export to the US as much as we can before anyone went to the White House,” Shang says.
Tech trends: AC integrated solutions vs the ‘conventional integration method’
Shang says Europe does have a couple of cards up its sleeve in terms of its own manufacturing and technology development ambitions.
Perhaps most notable among those is the expertise some European companies have built up in power electronics via the solar PV inverter space, which is now translating into expertise in power conversion system (PCS) and power plant controller (PPC) equipment for BESS.
Examples include Germany’s SMA Solar, which has recently delivered advanced grid-forming inverter technology to Europe’s biggest completed BESS project to date, Zenobē Energy’s Blackhillock project in Scotland, UK. The first 200MW/400MWh phase of the 300MW/600MWh asset went into commercial operation in the past couple of weeks, featuring BESS technology from Wärtsilä.
Others include Spain’s Eks Energy, which was acquired by system integrator Powin in 2022 and then, in turn, by Hitachi Energy just over a year later. Eks, which built up a track record working on complex microgrid and grid-connected solar and hybrid projects, delivered the PCS and PPC hardware for Waratah Super Battery, Australia’s biggest BESS project.
Another trend to watch out for, Shang says, is the growing popularity of AC-integrated BESS solutions from system integrators and technology providers.
This was demonstrated in real-time at the Energy Storage Summit EU, where Fluence debuted its new AC solution, SmartStack.
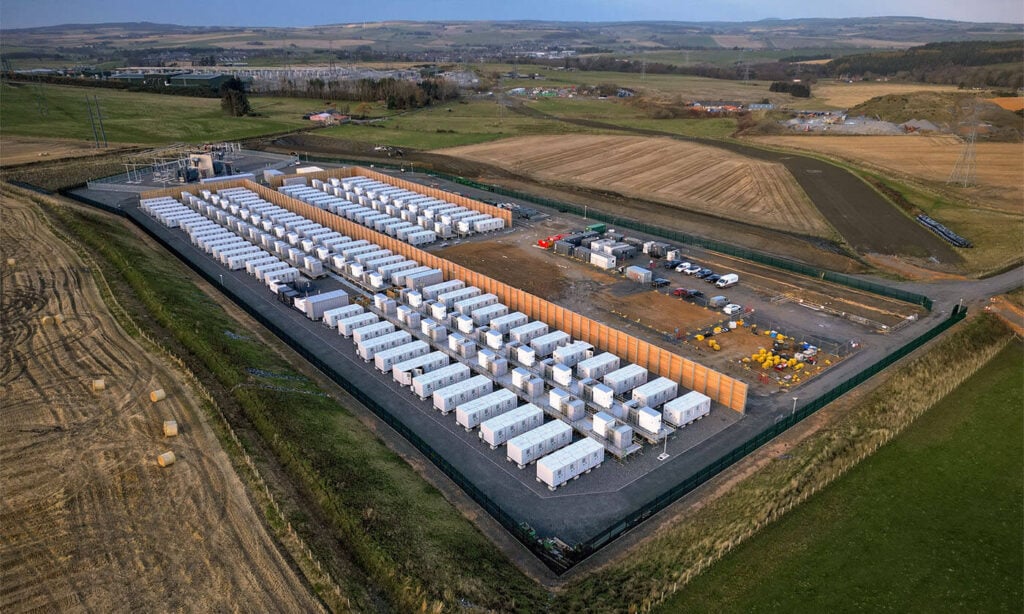
While Shang still believes the ‘conventional system integration method’—where manufacturers’ DC blocks are integrated along with PCS and other balance of plant (BOP) often from third-party suppliers—will remain popular, AC-integrated systems offer benefits to end customers.
“Basically, [for AC solutions], whenever people have any questions or problems, they always know who to talk with, but for the conventional system integration method, and because so many parties are involved along the supply chain, in a way, it creates complexity for the operation of the energy storage systems,” Shang says.
“We’ll see which will be the winner, but in Europe, we do see that the supply chain is complicated for the whole energy storage system. I would say this AC-integrated solution and the conventional way will go hand-in-hand.”
Workforce recruiting and long lead times for transformers are among this year’s challenges
In a panel discussion on supply chains for large-scale BESS projects at the Energy Storage Summit EU 2025, Lucie Kanius-Dujardin, global managing director at system integrator New HOrizons Ahead (NHOA), said that the biggest holdups in procurement today are coming from long lead items, particularly transformers.
Echoing sentiments heard from sources Energy-Storage.news has spoken to in the US over the last couple of years, Kanius-Dujardin said that battery cell supply bottlenecks have eased while power grid transformer supply has become constrained.
BESS companies competed with EV counterparts for cell supply in the big squeeze during the COVID-19 pandemic. As Kevin Shang pointed out earlier, the two industries still have closely connected supply chains, but EV demand growth has slowed.
Conversely, all grid-connected electric power infrastructure projects, from solar PV and wind to batteries and thermal generation, depend on transformers.
Shang agrees that transformers are the equipment procurement bottleneck. He adds that battery cell and balance of plant (BOP) costs continue to come down and “bottom out” soon, with the cost reduction trajectory likely to plateau in the coming years.
However, labour costs are going up, he says.
“Labour cost is going to continue to put upward pressure [on prices]. With that, there is a bit of a limitation of how cheap it is going to get because, at some point, the labour cost is going to get more sophisticated,” Shang says.
“You need more skilled people to handle those batteries and install them, do the operations, maintenance, and because of that, upward pressure is going to continue to be there from the labour side.”
So, many different dynamics are at play in the upstream end of Europe’s energy storage value chain. Our conversation with Kevin Shang merely scratches the surface of what is, as he says, a complex topic.
For those interested in the European market’s current status, it is worth taking a look at the new European Energy Storage Inventory interactive database created by JRC Smart Electricity Systems, a branch of the European Commission’s ‘in-house science service,’ using Wood Mackenzie data.
The inventory displays project data for energy storage projects across Europe, featuring 1,771 different projects at the time of writing spanning different technologies in 33 different categories and subsets. Projects at different stages of development, permitting, construction and lifecycle are included, from 46 European countries.