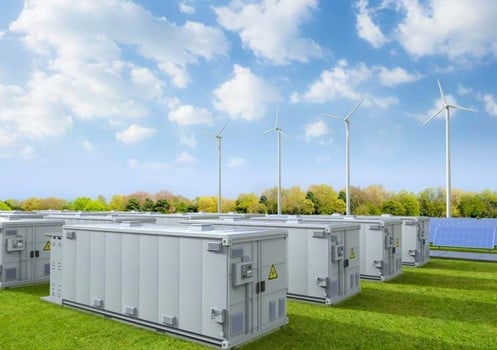
Quality control in the supply chain for battery energy storage systems is becoming increasingly critical. Vicente Parra and Carlos Sandoval of Enertis Applus+ look at some of the key steps to ensuring robust risk management in the selection, procurement and manufacturing of BESS equipment.
This is an extract of a feature article that originally appeared in Vol.42 of PV Tech Power, Solar Media’s quarterly journal covering the solar and storage industries.
Every edition includes ‘Storage & Smart Power’, a dedicated section contributed by the Energy-Storage.news team, and full access to upcoming issues as well as the 10-year back catalogue is included as part of a subscription to Energy-Storage.news Premium.
The global market for BESS is experiencing substantial growth worldwide, driven predominantly by the increasing demand for grid-scale energy storage solutions [1]. However, the development and deployment of BESS projects are not without significant challenges, bringing technical complexities, evolving regulatory landscapes and inherent safety concerns.
Enjoy 12 months of exclusive analysis
- Regular insight and analysis of the industry’s biggest developments
- In-depth interviews with the industry’s leading figures
- Annual digital subscription to the PV Tech Power journal
- Discounts on Solar Media’s portfolio of events, in-person and virtual
A key phase in mitigating these risks lies in the selection, procurement and manufacturing of BESS equipment.
Implementing robust Quality Assurance and Quality Control (QAQC) measures, along with well-structured supply chain risk mitigation strategies, from the early stages of a project is essential. A proactive and rigorous approach ensures the protection of substantial investments, enhances project profitability, and safeguards the long-term performance and safety of BESS installations.
By identifying potential risks early and applying effective mitigation strategies, stakeholders can minimise costly delays, prevent underperformance and significantly reduce safety hazards during operation.
This article provides an analysis and strategic guidelines on QAQC practices and supply chain risk management for BESS projects, with a particular focus on factory and manufacturing processes. Drawing from Enertis Applus+ expertise in factory audits, manufacturing oversight, and Factory Acceptance Tests (FAT) conducted throughout 2024, the insights presented here are based on assessments of 11 BESS manufacturers in China—both fully and partially vertically integrated—supplying lithium iron phosphate (LFP) BESS products to key markets such as the USA, UK, Australia and Italy.
Towards a zero-risk supply chain
The BESS supply chain is a complex network encompassing raw material extraction, component manufacturing and system integration, all of which present significant challenges. These include a highly concentrated manufacturing base, rapid technological advancements requiring stringent QAQC measures and the increasing demand for sustainability and traceability. Addressing these challenges is essential to ensure long-term resilience and risk mitigation.
Risk category | Specific supply chain risk | Mitigation strategy |
Raw material availability | Shortages of lithium, cobalt, nickel, graphite | Project stakeholders should diversify with BESS suppliers who are able to provide transparent information about the sourcing locations. Suppliers should seriously demonstrate their commitment and progress in utilising alternative materials and implementing robust recycling technology practices. |
Geopolitical instability | Trade restrictions, political conflicts, export controls | Select BESS suppliers with manufacturing bases across multiple regions and extensive supply networks to mitigate tariff impacts. Define contingency plans for supply disruptions. |
Reliance on single suppliers | Dependence on a single manufacturer for critical components | Secure long-term contracts with multiple BESS suppliers [2]. Identify and qualify BESS suppliers preferably with full vertical integration* and/or strong relationships for other key components. |
Quality and traceability | Difficulty in verifying the origin and quality of raw materials and components | Implement robust supplier qualification processes, conduct comprehensive factory audits, establish clear traceability requirements in supply contracts. |
Ethical sourcing | Concerns about human rights abuse and environmental degradation in mining and manufacturing regions | Implement rigorous due diligence processes for supplier selection, conduct ESG audits, prioritise suppliers with strong ethical and sustainability practices that can provide real evidence about transparency of their supply chain and compliance with different local regulations such as the EU Battery Regulation, UK Modern Slavery Act, Uyghur Forced Labor Prevention Act (UFLPA) [3]. Define a robust combination method for traceability verification. |
Implementing QAQC plans for BESS projects
This process requires careful planning and commitment to reach the best practices required for secure supply chain control.
Developing a QAQC plan specifically tailored to address the unique risks associated with the project’s requirements is a crucial first step. This plan should consider all stages of the BESS lifecycle, from the initial procurement of components through the final commissioning and ongoing operation phase, ensuring that quality is maintained throughout the system’s lifespan.
Early detection and proactive mitigation of potential defects in BESS components, even before the commencement of manufacturing processes, significantly enhance the safety and long-term durability of the overall system, reducing potential hazardous incidents and ensuring strict adherence to established quality standards.
Challenges in inline production monitoring and FAT witnessing
Based on Enertis Applus+’s experience in technical support negotiations with leading BESS suppliers, conducting inline production monitoring and Factory Acceptance Test (FAT) witnessing is significantly more complex at the battery cell level compared to system-level integration. Several key factors contribute to these challenges:
i. Restricted access due to proprietary technology. The highly confidential nature of battery cell chemistry and manufacturing processes often limits auditor access to critical information, as suppliers seek to protect their intellectual property.
ii. Complex and fragmented supply chains. Battery cells rely on intricate supply networks involving multiple suppliers, making comprehensive traceability assessments resource-intensive and time-consuming.
iii. Stringent quality control and disclosure reluctance. While strict quality control is essential for safety and performance, some manufacturers are hesitant to disclose detailed inspection data, fearing potential misinterpretation or reputational risks.
As seen in the PV module industry, these limitations are likely to diminish over time as the BESS market matures and third-party inspections at the point of origin become a standard practice worldwide.
Despite this, negotiating access to inline production monitoring during supply agreement discussions remains particularly difficult at the cell level. Even fully vertically integrated BESS suppliers, which oversee the entire process from cell manufacturing to system assembly, often impose access restrictions. While vertical integration theoretically enhances transparency, factors such as technological confidentiality, operational scale and supply chain complexity continue to pose significant barriers to comprehensive factory inspections.
The role of BESS integrators in ensuring quality and compliance
BESS integrators serve as the primary point of contact for project stakeholders, overseeing the assembly and integration of complete energy storage solutions.
They are responsible for sourcing and integrating key components—such as power conversion systems (PCSs), medium-voltage stations and battery cells—either internally or through external partnerships. Given their contractual obligations, integrators must ensure the overall performance and safety of the entire system by collecting and verifying all necessary documentation from their own supply chain or direct suppliers to meet project requirements.
Key insights from BESS factory audits and inspections
Recent factory audits and inline production monitoring conducted by Enertis Applus+ have revealed critical insights into the quality and potential risks in BESS manufacturing, highlighting the following key findings:
The evaluated battery cell and BESS system-level suppliers exhibit a tiered structure with both globally recognised premium players and rapidly emerging second tiers, predominantly concentrated in China [4]. The remaining suppliers are partially vertically integrated and operate primarily through strategic partnerships to different extents.
Factory inspections revealed that nearly half of all quality issues originated at the battery cell level, 44% of which were linked to defects at the BESS system level and 7% were associated with battery module defects, as shown in Figure 1.
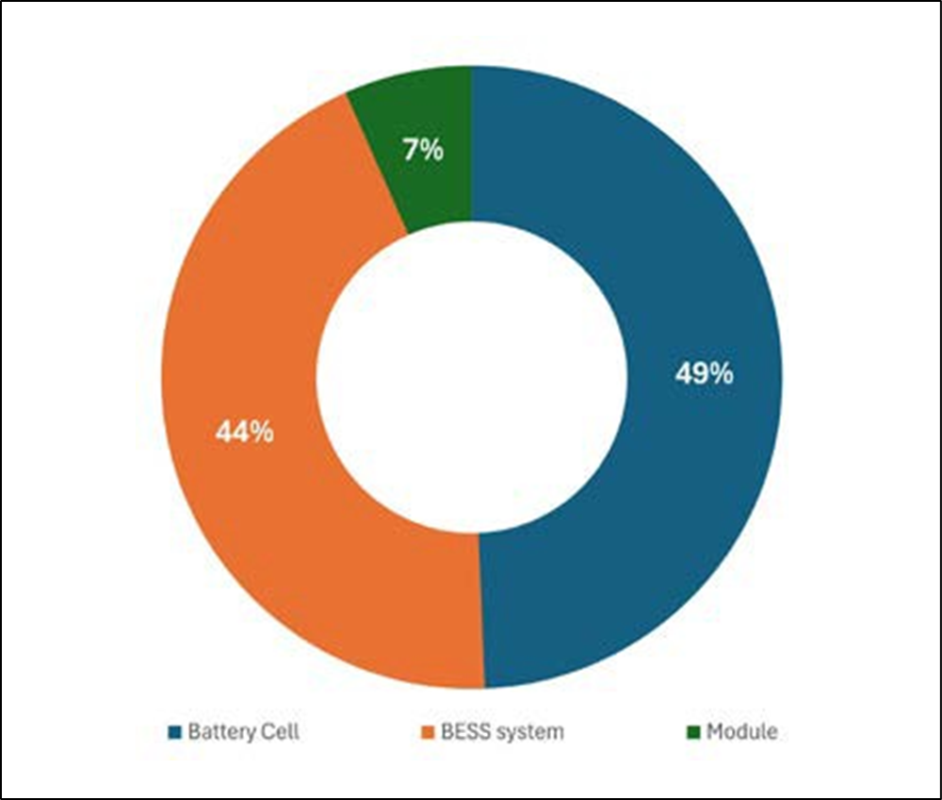
Despite the certain maturity of battery cell production, the rapid scaling and evolving demands of the grid-scale BESS market present challenges analogous to those faced by the early PV module industry. Factory inspections at the battery cell level revealed that 70% of issues stemmed from the manufacturing process.
Key contributing factors included inadequate warehouse management and storage conditions (38%), non-compliance with the SOP during production (14%), and deficiencies in incoming quality controls, such as poor environmental parameter control or improper material qualification practices (8%).
Furthermore, documentation issues accounted for 16% of total cell- level findings, primarily related to missing or non-compliant IEC/ISO standards and certifications for product manufacturing and testing.
These findings highlight the growing pains of scaling production and adapting to the increasing demands of grid-scale BESS applications.
Most of the findings that occurred at the BESS system level were identified during the inspection of the enclosure (73%), often related to appearance inspection issues (26%) during the assembly process and in the workshop environment (15%). Both findings suggest potential weaknesses in the container integration process due to a lack of operator training, deviations while following working instructions, testing setup deficiencies, inconsistencies with specific contractual requirements and the inherent risks associated with manual assembly.
Other relevant findings include fire suppression system operation (13%) related to failures with exhaust fans, air bleed valves and inadequate warehouse management practices (9%) due to poor main workshop conditions and debris.
Notably, rain test failures accounted for 6% of the previous findings, posing a critical risk of water ingress into BESS containers (Figure 2). The severity of such failures was underscored by real-world incidents such as that of the Elkhorn battery facility in Moss Landing, California, in September 2022 [5].
A public investigation report identified that rainwater intrusion through the container led to electrical arcing, ultimately triggering thermal runaway and a major fire within a BESS unit. The report attributed the water ingress point to the improper installation of a vent shield, dislodging a valve and allowing water to enter.
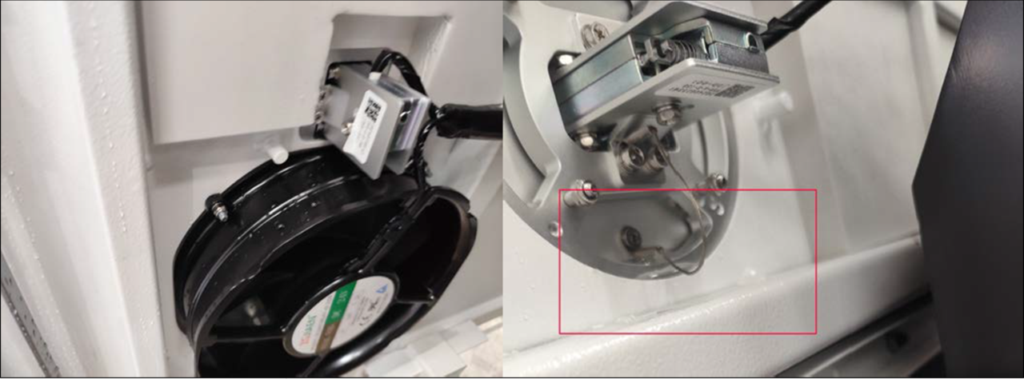
Key to driving market confidence
A sustainable and reliable supply chain for BESS requires early QAQC strategies and dedicated audits. PV module inspections by third parties are now well-established and standardised, given their role in mitigating performance and safety risks.
Now with BESS, this need is even greater due to the added complexity of chemical processes ruling the device, alongside physical ones, especially, among others, in terms of fire safety issues [6]. Therefore, ensuring a strict supply chain and in-factory quality control from the outset is key to driving market confidence, deployment and long-term adoption.
Notes:
[1] A. Petropoulos, B. Wanner, et al., Batteries and Secure Energy Transitions, International Energy Agency, Apr. 2024. https://www.iea.org/reports/batteries-and-secure-energy-transitions
[2] C. Murray, “Europe’s BESS industry moves from EPC ‘wrap’ to multi-contracting, closer ties with suppliers”, Energy-Storage.News, Feb. 26, 2025. https://www.energy-storage.news/europes-bess-industry-moves-from-epc-wrap-to-multi-contracting-closer-ties-with-suppliers/
[3] J. Spence, “Reducing risk in battery procurement for large energy storage projects in the US,” Energy-Storage.News, Oct. 9, 2024. https://www.energy-storage.news/reducing-risk-in-battery-procurement-for-large-energy-storage-projects-in-the-us/
[4] Battery StorageTech Bankability Ratings Report Q4- 2024. https://marketresearch.solarmedia.co.uk/reports/battery-storagetech-bankability-ratings-report/
[5] EPRI, Insights from EPRI’s Battery Energy Storage Systems (BESS) Failure Incident Database: Analysis of Failure Root Cause. May. 2024. https://www.epri.com/research/products/000000003002030360
[6] Effective battery storage fire safety involves going beyond standards. Feb 18, 2025. https://www.energy-storage.news/effective-battery-storage-fire-safety-involves-going-beyond-standards/
About the Authors
Dr. Vicente Parra has 17 years of experience in the photovoltaic industry. He currently leads the QAQC and Vendor Inspection services of the Renewable Energy Services Unit at Applus+, following the acquisition of Enertis Solar, a company he joined in 2014 as head of quality, innovation and testing services. He is a globally recognised technical consultant with extensive knowledge of the manufacturing, performance and quality of PV, BOS, and BESS equipment.
Carlos Sandoval has over 12 years of experience in the oil and gas industry, consultancy and PV field. He currently works at Enertis as senior manager, leading QAQC and BESS initiatives globally. He supports technical advisory services for EPC, owners and financial entities on topics related to supply agreements, testing plans, technology trends, supplier qualification, PV and BESS supply chain. His experience in QAQC and project management covers 15GWp+ on large utility-scale projects worldwide.