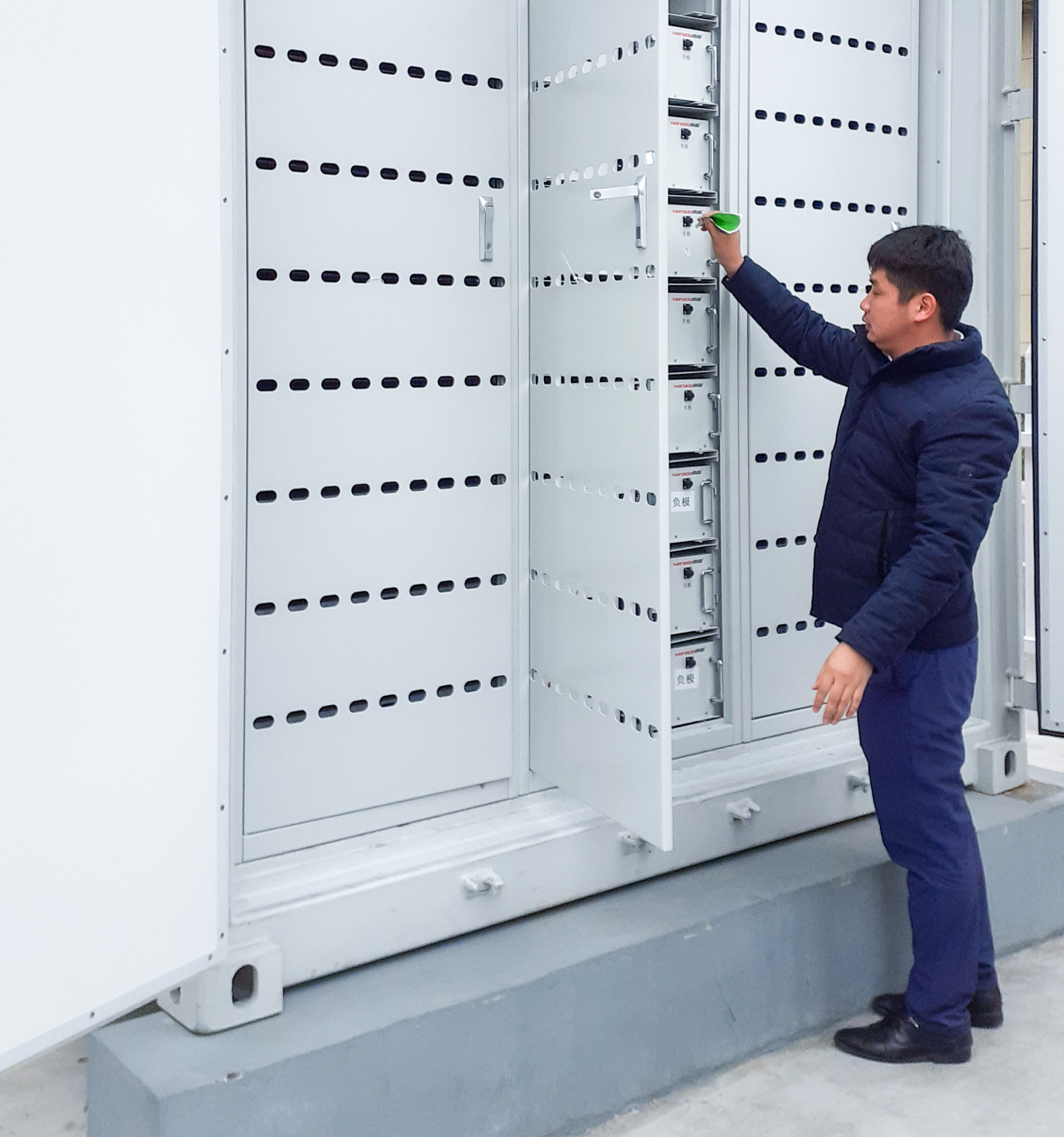
The specific cell chemistry chosen by rechargeable lithium-ion battery manufacturers and suppliers may be the “most visible” characteristic of their devices, but is only one of five primary factors influencing battery performance.
According to a new technical paper contributed by Photovoltaik Institute Berlin (PI Berlin) to the quarterly journal PV Tech Power, the other four factors: cell geometry, manufacturing quality, the matching of technology to the right application and system integration are also critical factors behind battery performance.
PI Berlin, well known in the solar PV industry for work that includes auditing and assessment of solar module manufacturing quality, has broadened the scope of its offered services to include manufacturing quality assessment of lithium-ion batteries used in the renewable energy sector.
Among those critical factors, cell chemistry is considered the “tip of the iceberg,” PI Berlin authors Ian Gregory, Benjamin Sternkopf and David Prince write in the article, ‘What you should know about manufacturing lithium-ion batteries’.
Enjoy 12 months of exclusive analysis
- Regular insight and analysis of the industry’s biggest developments
- In-depth interviews with the industry’s leading figures
- Annual digital subscription to the PV Tech Power journal
- Discounts on Solar Media’s portfolio of events, in-person and virtual
In other words, cell chemistry is the “most visible” characteristic of a battery, the trio wrote, but what is often missed is that “the actual performance of battery systems in real-world applications seldom depends to a large degree on the cell chemistry”.
“More often it is one of the other five factors,” the PI Berlin team said.
Conversely, the importance of assuring manufacturing quality is often overlooked, and among the “least discussed” of those primary factors, despite it being one of the most significant. Even if two makers use broadly or exactly the same cell chemistry, the techniques and conditions at their production lines can make a huge difference to quality of the finished product.
There is a large amount of information already in the public domain about cell chemistry or cell geometry, while matching battery technologies to the right applications can be modelled with available computing tools. Yet manufacturing and quality of manufacture largely remains an “in-house” secret guarded by each maker of batteries, with “little incentive” for any of them to have details of their processes published.
Making the ‘perfect’ battery, or ‘finding the sweet spot’
In their comprehensive article, PI Berlin’s Sternkopf, Gregory and Prince talk the reader through the exactly how lithium-ion batteries are made and many of the various factors that need to be taken into account during production that can affect the quality of the battery that comes out the other end of the line.
“Battery manufacturing is a complex production process featuring over 170 individual steps between quality control and production. Some of the most critical quality parameters include residual humidity and surface homogeneity. The impact of poor manufacturing can cause the cell to degrade very quickly. Cell capacity can be reduced after only a few cycles, or if cells remain inactive, they will be more prone to self-discharge.
“If the production process is managed poorly safety hazards can also be produced. For example, poor surface homogeneity can generate small spikes that can punch through the separator and generate a short circuit inside the cell.”
There are a combination of practical and financial questions that need to be asked governing quality management in manufacturing, according to the paper. For example, the authors wrote, while it is possible to make batteries that last 15,000 cycles and 20 years, in reality, 3,500 to 4,000 cycles and 10 years of operation are sufficient for most applications.
“The recipe for making such a battery is not about making a ‘perfect’ battery, but about finding the sweet spot between cost, performance and lifetime.”
Read more about the contents of the latest edition of PV Tech Power (Vol.24) – including ‘Storage & Smart Power,’ the section contributed by the E-S.n team – while you can download the full issue from the PV Tech Store, here. All previous editions of the journal, as well as our upstream journal Photovoltaics International and many more technical papers are also available to download.