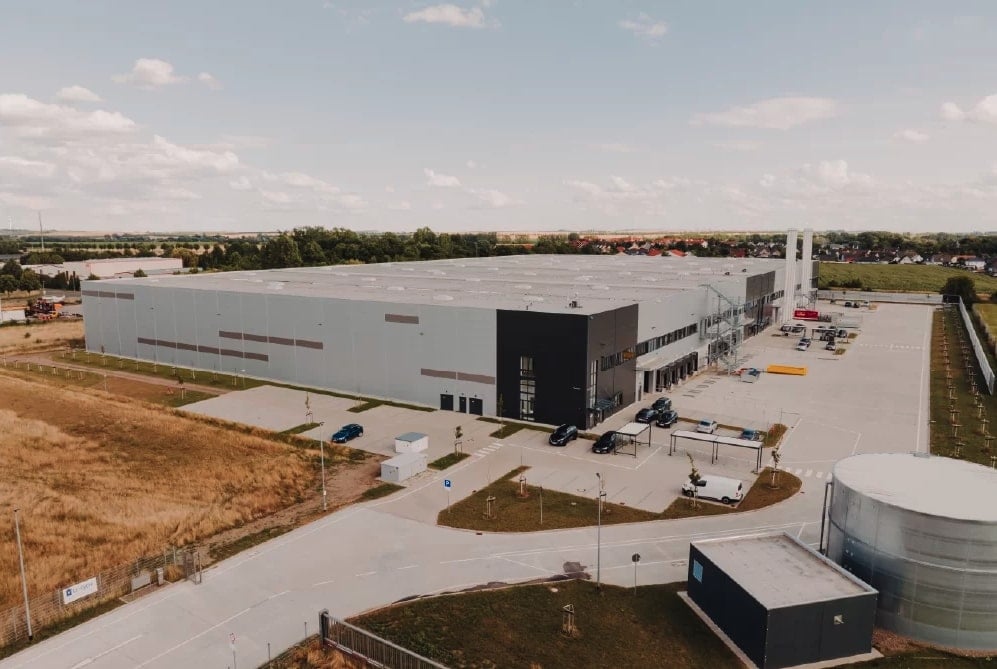
Li-Cycle, a North America-based company focused on lithium-ion battery recycling, has opened a black mass production facility in Germany.
The Canada-headquartered, NYSE-listed company announced the commercial operation of the Magdeburg facility yesterday (1 August), its first in Europe.
Enjoy 12 months of exclusive analysis
- Regular insight and analysis of the industry’s biggest developments
- In-depth interviews with the industry’s leading figures
- Annual digital subscription to the PV Tech Power journal
- Discounts on Solar Media’s portfolio of events, in-person and virtual
The facility will process an initial 10,000 tonnes of lithium-ion battery material a year, rising to 30,000 in future, to produce black mass, the resulting mixture of valuable battery metals including lithium, manganese, cobalt and nickel.
These would then be sent to a ‘hub’ sight which would use metallurgical processes to separate out the mixture into each metal, which can then be sold back into the battery supply chain for production of cells. The company is working with mining giant Glencore to repurpose an existing site in Portovesme, Italy, into its European ‘hub’ facility.
The firm’s North America hub and spoke model is closer to going live with operational spoke facilities in Ontario (Canada), New York, Arizona and Alabama and a ‘hub’ also in New York set to start commissioning later this year. Across the five spoke facilities now operational, the firm’s processing capacity is up to 81,000 tonnes annually. The company is planning additional spokes in France and Norway.
Facilities are typically separate because black mass processing is a significantly higher capital-intensive process than black mass production. Black mass production on the other hand requires a big focus on logistical networks, to retrieve battery material from the market.
The lithium-ion battery recycling market in Europe looks set to get a boost from new regulations approved by the European Union which will see minimum levels of materials to be recovered from waste batteries, and minimum levels of recycling content in new ones. Li-Cycle’s former CCO Kunal Phalpher has in the past said the regulations would be important for the market going forwards.
Although the majority of the battery material going into these spoke facilities will come from the EV sector, material from the stationary energy storage system (ESS) sector is starting to be seen too as the technology proliferates and projects age.
The battery manager for Sweden-based recycling firm Stena recently told Energy-Storage.news it was starting to see ESS volumes from the earliest pilot projects as well as after thunderstorms.
Companies in the recycling space may also increasingly become involved in the ESS sector through second life solutions due to the potential higher value that can be extracted by repurposing EV batteries rather than recycling them. Stena has a second life arm, BatteryLoop, while a partnership between Glencore, utility Ibedrola and waste management firm FCC will look at both recycling and second life.