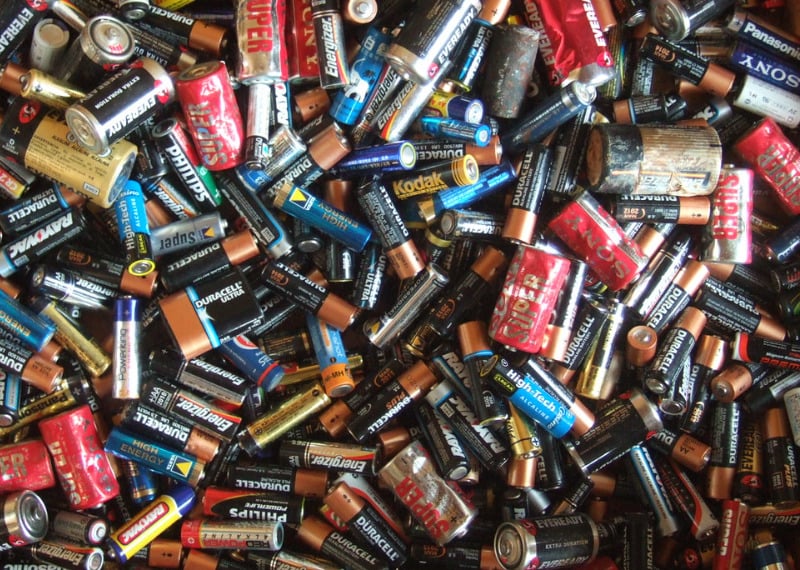
Supply chain risk platform Infyos discusses its research into forced and child labour in the battery supply chain, suppliers risk of exposure to it and what business risks that could entail for those in the ESS industry – particularly around the EU Batteries Regulation.
The company’s research into supply chains has found that companies accounting for 75% of the battery supply chain risks exposure to forced labour and child labour, as reported by Energy-Storage.news. That exposure could mean they violate existing laws in the US and upcoming regulations in the EU, and see their battery products blocked from the market.
Enjoy 12 months of exclusive analysis
- Regular insight and analysis of the industry’s biggest developments
- In-depth interviews with the industry’s leading figures
- Annual digital subscription to the PV Tech Power journal
- Discounts on Solar Media’s portfolio of events, in-person and virtual
Industry still needs to understand the risks
“The industry needs a tool to understand these risks. We work with renewable energy companies, investors, manufacturers and often they do not know much about who they are buying from,” Infyos CEO and co-founder Sarah Montgomery said.
Infyos helps companies identify who is in their supply chain and which suppliers are connected to which human rights abuses or other negative or illegal ‘impacts’. It covers 24 ‘impacts’ in total, with forced labour and child labour the two which are covered by its 75% figure. Its platform also helps customers and suppliers to log evidence of mitigating actions against those impacts.
“The mitigation aspect is the fundamental part of what we do. The upcoming regulations we’re talking about here suggest disengagement as a last resort—mitigation is crucial,” said Jeff Williamson, Infyos’ head of sustainability.
Forced labour and modern slavery is a big focus of the firm’s research and findings, specifically in the Xinjiang region of China where there is evidence the government is exploiting and violating the human rights of the local ethnic Uyghur population, including forcing them into work camps. There are indications that that some suppliers in the battery supply chain (and other industries including the automotive sector) utilise that forced labour, according to various sources including a 2022 report from the UN Special Rapporteur on contemporary slavery
Child labour is also a ‘complex issue’ in the battery supply chain, Williamson said. Energy-Storage.news has previously reported on the alleged use of child labour in cobalt mining in the Democratic Republic of the Congo (DRC). Potentially exploitative labour contracts and environmental damage from raw material extraction are other ‘impacts’ Infyos’ platform covers.
Montgomery: “The human rights abuses are connected to complicated supply chain structures. They might have a business relationship, like direct sourcing, with a company in the supply chain that has faced allegations of human rights abuses. Typically the big companies have the operational systems to identify and mitigate against human rights abuses in their own operations.”
ULFPA and EU Batteries Regulation
Human rights abuses and environmental catastrophes in the supply chain are a growing discussion on moral grounds as they become more clear and obvious. But, they also represent significant business risks which companies need to be aware of.
The US’ Uyghur Forced Labor Prevention Act (ULFPA) is the country’s strategy to ‘prevent the importation of goods mined, produced, or manufactured with forced labor in the People’s Republic of China’, the government says. It has a list of entities with known links to forced labour, and products have been blocked at entry. Republican lawmakers recently called for lithium-ion battery manufacturers CATL and Gotion to be added to that list – the companies adamantly deny having forced labour in their supply chains.
Meanwhile in Europe, the EU’s Batteries Regulation will include criteria around nine key ‘impacts’ (using Infyos’ terminology), including environmental impacts like air, water and soil pollution or degradation, biodiversity impact, energy use, human rights, child labour and forced labour.
Companies will need to have a supply chain risk management system in place in order to identify those risks in their supply chain and demonstrate they have taken due diligence steps to reduce that risk, Williamson said. It will be a combination of traceability – data and information showing exactly what products and materials, from where, have gone into your product – and evidence you’ve taken the steps to reduce the likelihood that your supply chain violates any of those nine criteria.
The penalty for not following this could be having your products blocked from the market, Montgomery said. The responsibility to provide the information falls on the suppliers selling their products into the market.
The regulations around the nine impacts in the supply chain are effective in August 2025, and will apply to batteries and battery energy storage systems (BESS) procured from then onwards. The EU devolves enforcement of rules like these to member states, so some countries might be stricter than others on enforcement.
Industry response to mitigate those risks
Although the responsibility falls on suppliers, compliance will also be driven by the developers and independent power producers (IPPs) procuring the technology and the banks providing project financing for the projects, since they will want to avoid the reputational (and potentially financial) risk associated with the rules, Montgomery said.
“Developers are now saying, show me the evidence that you meet these regulatory requirements, and they are verifying those responses,” Montgomery said. “They also don’t want to risk using a non-compliant product on their sites, as that could negate warranties and contractual clauses.”
“The lenders are also now requiring very detailed data to mitigate their own risk,” Williamson added. “So there will be other pressures driving developers to ask these types of questions to suppliers, even if actual enforcement of the rules might potentially be hap-hazard.”
More broadly, developers and those procuring battery products like BESS are in general taking steps to mitigate against those risks in three ways, Montgomery explained.
The first is pre-contractual discussions where a developer would ask a supplier to take a specific action against a very high-risk non-compliance before signing anything, Montgomery said.
The second is increasingly contractual mitigations where companies put in clauses to ensure continued compliance with current and new regulations, ESG performance more broadly and data sharing.
The last is more ‘medium-term’ mitigations where you work with a supplier to tackle the more complex problems which cannot be solved overnight, or keeping suppliers aware of regulations which might be coming down the line to ensure they can buy from them again in 6-12 months’ time.
Williamson said the approach could be similarly characterised for battery manufacturers and their sub-suppliers.
Is the industry ready for the Batteries Regulation supply chain rules?
It’s an obvious question to be answering in light of the firm’s research note last week, but Montgomery said that, no, the industry is not ready to be compliant ‘and there is a lot of work to do’ to get there. Futhermore, there is huge variation between companies in how quickly they are moving to get there.
“You have some manufacturers that we’re working with that are have recognised this is both a huge challenge, but also this is a big opportunity, if they can prove that they are one of the first, say, Chinese manufacturers that has understood this regulation and has got themselves ahead of it. And then you have at the other end of the spectrum, manufacturers that have possibly never even heard of the regulation and therefore definitely are not doing anything to get ready for it. And you have a big scale in between.”
In an interview with ESN Premium published in June, Tilmann Vahle, director for sustainable mobility and batteries at systems change consultancy Systemiq, said that the industry might see the forthcoming EU regulations as “overwhelming,” at first.
However, meeting the various requirements, including the creation of digital ‘product passports’ for batteries and their components, will likely be less complex than many anticipate, and the clear timelines and trajectory for their introduction allow for good faith intepretations of rules to be acceptable, Vahle said.