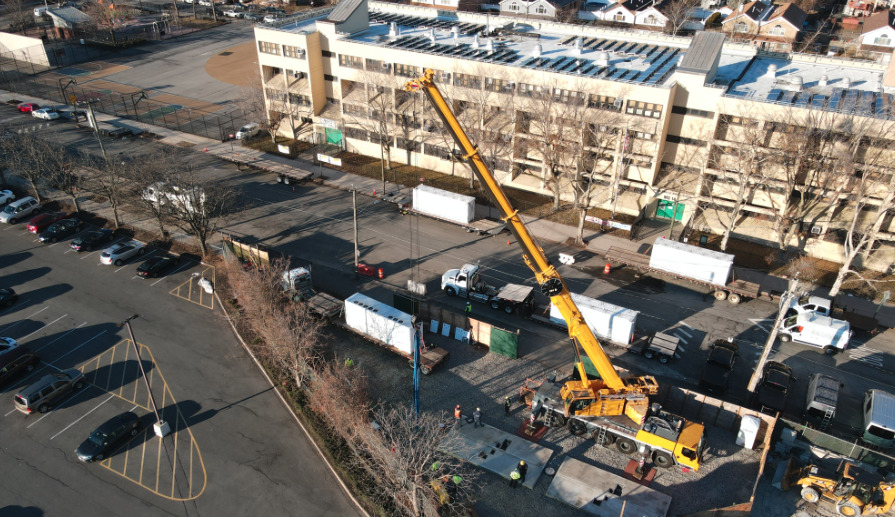
Projects are increasingly being deployed close to populations as available plots of land become more scarce, making BESS noise a bigger topic than ever before, writes noise and acoustics consultancy Acentech’s Ethan Brush.
The many benefits of battery energy storage systems (BESS) and the ability for them to be deployed in a relatively small footprint, means that we may soon be seeing them everywhere. That being the case, BESS facilities will get closer and closer to other things, the most critical of them residential properties.
Enjoy 12 months of exclusive analysis
- Regular insight and analysis of the industry’s biggest developments
- In-depth interviews with the industry’s leading figures
- Annual digital subscription to the PV Tech Power journal
- Discounts on Solar Media’s portfolio of events, in-person and virtual
In these cases, acoustical consultants worldwide will be relied upon to mitigate the noise from BESS installations so that they can be properly sited per local regulations, and to reduce the risk of community annoyance. BESS sound is of particular importance because these stations can be located within communities very close to residential properties.
Cautionary tales can be found in the haste to deploy data centre and bitcoin mining facilities, where in some jurisdictions without specific noise regulations there have been instances of intense public negativity surrounding the industrial noise produced by the facility.
Battery energy storage facilities are still an emerging piece of our electrical grid. A few of the key items of equipment in BESS installations are relatively new to the market, and information on the amount of sound they generate is not always available. Yet, the developer of a site is often still beholden to meeting noise limits for the nearby community. The equipment is not very different from that used in substation facilities or building heating ventilation and air conditioning systems.
However, the manufacturers of equipment in these more mature markets have had the time to invest in quieter products, and better documentation of their sound emissions. The manufacturers of BESS equipment will eventually need to catch up to this level of acoustical sophistication so that the risk of noise issues can be managed.
As BESS technology proliferates, it will increasingly be deployed closer to populations as more remote plots of land become increasingly less available, making the topic of noise and noise mitigation highly relevant. Noise is a particular issue in population-dense geographies in Europe but increasingly in the US, Australia and elsewhere too.
Noise sources
You might be thinking: “what makes sound at a battery energy storage facility?” The main noise sources from a BESS facility are:
Cooling systems
Like any electronic device, grid scale battery systems operate most optimally and safely at an ideal temperature and humidity. Therefore, various air or liquid cooling and heating systems are used. Sound from inlet and outlet airflow vents, as well as fans and pumps are emitted from each battery enclosure. The sounds from these systems are like rooftop heating ventilation and cooling units in residential and commercial buildings.
Inverters
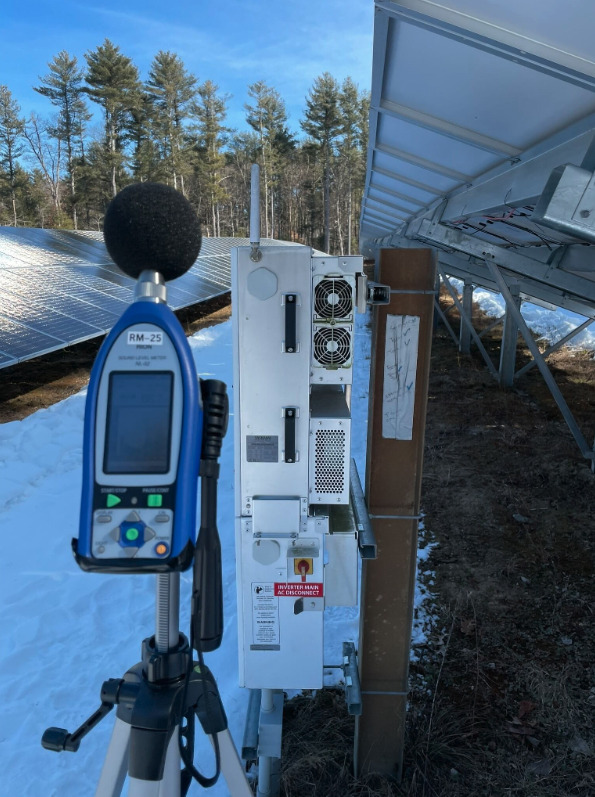
Inverters convert electricity from direct current (DC) in the batteries to alternating current (AC) that we use in our homes. The process also happens in reverse when AC electricity is used to charge the batteries. A small amount of energy is lost in the form of heat with this conversion, so cooling is needed to prevent overheating. This is usually accomplished with air-cooled fans that produce some noise.
The process of converting DC into AC power requires very fast switches which change the polarity (or direction of electrical flow). In the United States AC power cycles 60 times per second (or 60 hertz), so the switches must activate twice per electrical cycle. This process produces tonal sound at twice the electrical line frequency (120 hertz), as well as its harmonics (240, 360, 480 hertz and higher).
In many parts of the world the AC power cycles 50 times per second (50 hertz), so the harmonics are slightly different (100, 200, 300, 400, hertz). The nature of this sound is typically heard as a buzz. Tonal noise is often much more noticeable in the presence of other background sounds, which can be particularly annoying to the people hearing it.
Transformers
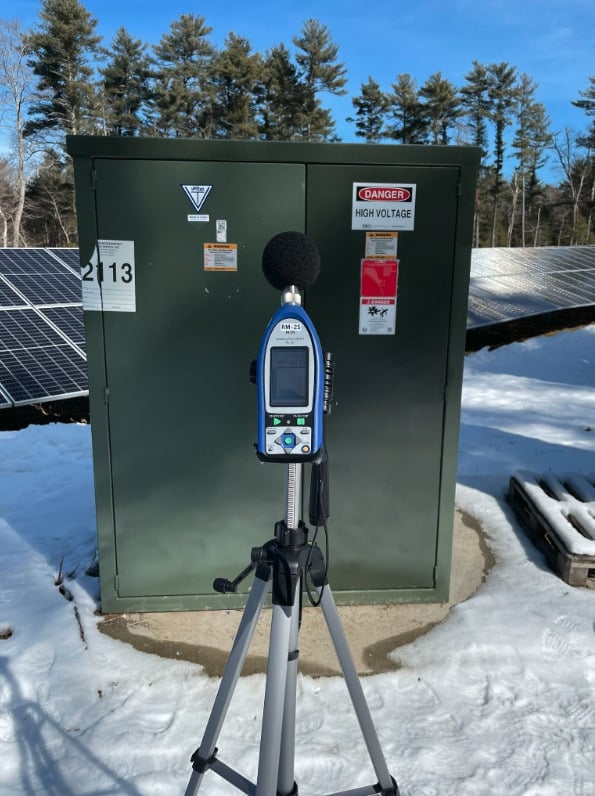
The sound that most people think of from transformers is a distinctive “hum”. If you’ve ever been around an outdoor substation or a building’s transformer vault, you may be familiar with this sound. Transformers are used to change AC voltages to step up or step down in the level. Everyone should be familiar with the cylindrical transformers on telephone poles that lower the voltage from the high voltage transmission lines to a level that is safe for use in homes and businesses.
The transformers at a BESS facility are much larger than those you see on telephone poles.
There are three sources of noise from within the transformer: (1) core noise, (2) coil noise, and (3) fan noise. The core and coil noise are caused by electromagnetic forces which occur two times for every cycle of AC power. Like the inverters, this results in a 120-hertz or 100-hertz primary sound source, along with its harmonics. The third source of sound is from cooling fans mounted outside the transformer, but some transformers do not have fans and instead have passive radiant cooling fins. This is a quieter option.
Mitigation
While BESS facilities are relatively new developments, each of these noise sources are common among many other industries that have been around for a very long time. Therefore, we have the tools necessary to design a BESS facility with the right noise control treatments so that it can be a good noise neighbor, just like any other industrial facility. To do that, we generally follow these steps:
Understand the noise criteria for the site
Thousands of cities, towns, and jurisdictions around the world have documented noise ordinances that are aimed at limiting industrial noise emissions to residential areas. Their level of complexity and clarity can vary a lot, with some giving very specific details on the exact noise metrics and conditions that must be met, to just a single decibel number limit or even simply a qualitative description pertaining to “peaceful enjoyment” of one’s property. In some locations there may not even be a noise ordinance pertaining to a BESS facility. Even if that is the case, it could be appropriate for BESS developers to at least consider their impact on neighbors and their potential negative response to the project, even if there is no legal mandate to abate noise.
Many noise criteria impose a penalty for the presence of tonal noise, which is a sound character generated by many pieces of BESS equipment like inverters and transformers. A tonal sound is one composed of a single frequency component, like a whistle or hum, and can be particularly challenging to fully mitigate.
Model the sound from the BESS facility to the community
During the design process for a BESS facility, an acoustical consultant will identify all the significant sound sources from the various equipment. Vendors provide information regarding their product’s noise emissions, and sometimes this information is obtained from field measurements at existing installations. This data will be used to generate a model of the total facility’s sound emitted at the property line and at sensitive receptors such as homes. The acoustical model includes these equipment sound sources along with topographical features of the surrounding area. The results of this modeling evaluation will be compared to relevant noise limits for the project. The results of an example BESS sound modeling analysis are shown in the figure below.
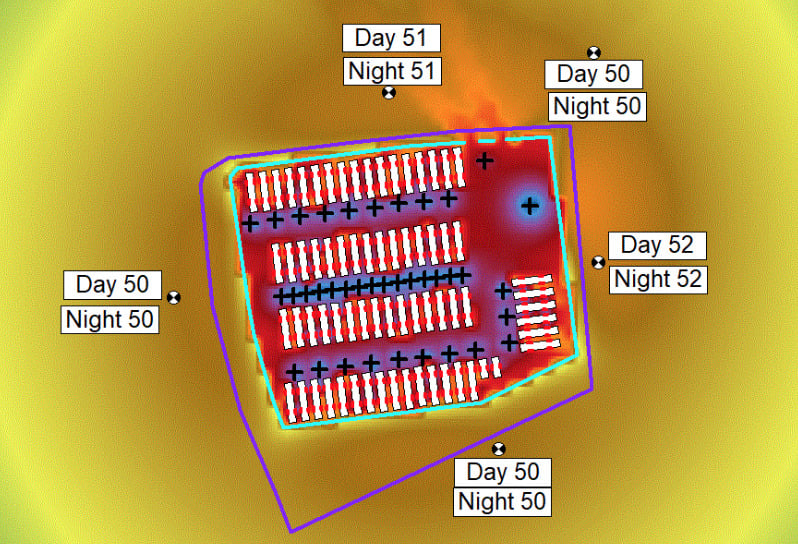
As mentioned earlier, not all BESS equipment manufacturers have data on the amount of sound their products make. A single BESS project could have many different suppliers, which can make accurate modeling of the total facility noise levels challenging if there is missing information. There are American and international standards for measuring the sound emissions of products used in BESS facilities. The National Electrical Manufacturers Association (NEMA) standard publishes limits for average audible sound levels from electrical equipment to achieve a NEMA rating.
The International Electrotechnical Commission (IEC), and The Institute of Electrical and Electronics Engineers Standards Association (IEEE) also have standards for quantifying the sound output of various electrical equipment. For the cooling systems there are standards published by the Air-Conditioning Heating and Refrigeration Institute (AHRI), American Society of Heating, Refrigerating and Air-Conditioning Engineers (ASHRAE), American National Standards Institute (ANSI), and the International Standards Organization (ISO). These standards can also be supplemented with field measured sound data at existing BESS facilities.
Measure the site ambient sound levels
Many noise ordinances, such as the Massachusetts Department of Environmental Protection’s noise policy, stipulate that the facility sound levels must not exceed a threshold above ambient conditions. Those ambient sound levels need to be established before the project is installed, or during a time when the facility is completely shut down. It is common to measure ambient sound conditions for a week or more during relatively calm weather to obtain a full characterisation of the sound environment at a site. Because the noise limits are relative to the ambient site conditions, a quiet area will require a lower limit than an already noisy area.
Noise ordinances in other places often prescribe a fixed limit for noise that may be produced by a facility. This may not necessarily need a site study for demonstrating compliance, but ambient noise measurements are usually recommended to help put the results of modeling efforts into context of the existing environment.
Add noise control measures
Designing noise control measures for a BESS facility is an iterative process. If the initial design and layout of the noise producing equipment is expected to exceed the relevant noise limits for the project, then an acoustical consultant will need to devise solutions to lower the predicted sound emissions from the total facility. Solutions to noise problems can be found by considering a source/path/receiver model.
Source
The first action should be to consider how the noise levels can be lowered at their source. Lowering sound at the source of the equipment is often the most preferable way to mitigate noise issues for a given receiver. This can be achieved by selecting quieter products. There is certainly an opportunity for BESS equipment manufacturers to differentiate themselves from their competitors by offering lower noise alternatives. Other source mitigations can include surrounding the equipment in an acoustical enclosure or wrap when possible, or quieting fans and air ducts with silencers or louvers. Orientation of the BESS equipment within the grid of systems can also be considered so that the loudest equipment faces away from a sensitive receptor.
Path
The second action should be to consider the path sound makes when traveling between its source and a sensitive receiver. Sometimes the easiest mitigation is to simply move the loudest noise sources farther away from the nearest property line or sensitive receptor. This would change the length of the path from source to receiver and result in lower sound levels at the receiver. However, BESS facilities often place multiple large battery systems in a grid to fit as many of them in an area as possible. The most common form of noise control is a noise barrier (or wall) of appropriate height. This is path mitigation because it places a barrier between the source and receiver to block the direct path of sound.
Receiver
Finally, one should consider how to reduce noise levels at sensitive receivers. An example of mitigating noise at the receiver would be providing upgraded windows to affected homeowners. This is a strategy often applied near airports. While this may provide some goodwill to neighbors of BESS projects, it isn’t practical, because the noise regulations specify sound limits at the receiver regardless of whether there is a building present.
These various mitigations are then added to the acoustical model of the facility and surrounding area. The process is complete when the predicted sound levels are compliant with the relevant noise limits for the project.
Post-construction sound measurements
Sometimes it is appropriate to measure the sound levels at sensitive receptors after a facility is fully completed to demonstrate compliance with the noise criteria for the site. This is typically done at night when the ambient sound is at a minimum and may include turning all BESS equipment on and off for periods of time to fully characterise the total facility sound emissions.
The equipment used for measuring environmental sound is required to have accuracy standards as defined by relevant international standards for measurement equipment. Sound level meters are classified by standards that define a wide range of accuracy, performance, and calibration specifications that the microphones in our cellphones do not meet. Failure to use the appropriate sound measurement equipment could discredit reported values in a regulatory or litigious situation.
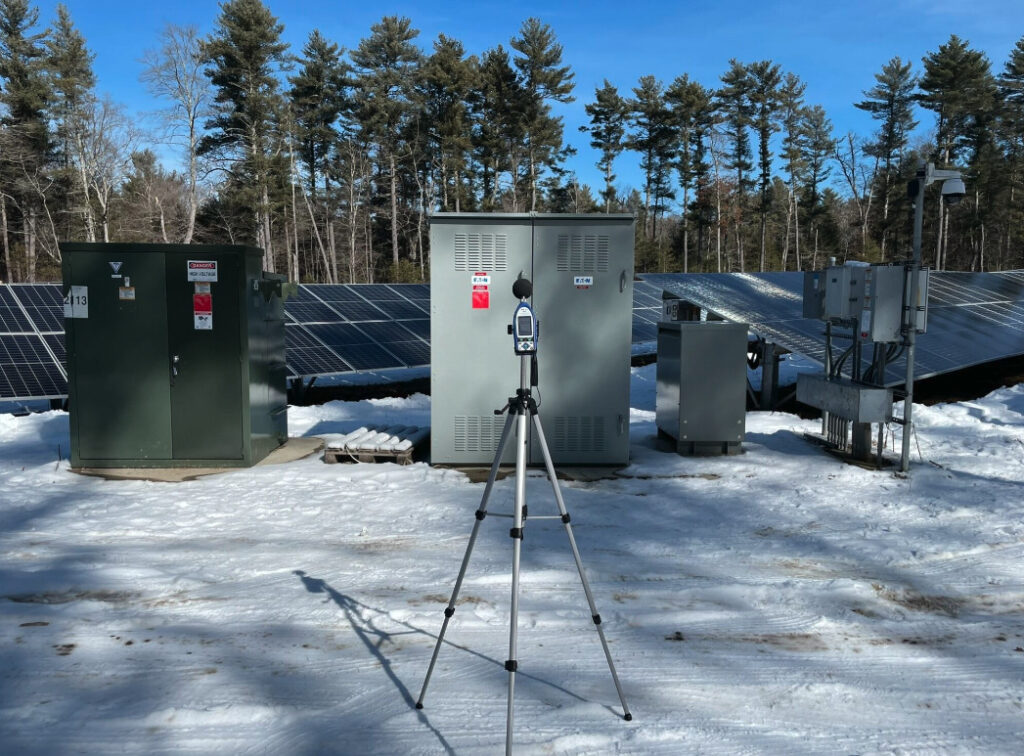
Don’t take noise for granted
When planning for a battery energy storage site, it is important to enlist the help of acoustical consultants to navigate the regulatory process surrounding noise and ensure the right controls are implemented. When this is done in the initial design and planning of a BESS facility it can help avoid future problems with permitting and with public relations. With a thoughtful approach and effective noise control treatments, BESS facilities can continue to be added to our electrical grids without causing undue noise for anyone living close by.
About the author
Ethan Brush is a Principal at Acentech, an acoustics, noise, vibration, and technology consulting firm. With over 18 years of engineering and project management experience in structural dynamics and acoustics, he directs teams of engineers and technical specialists in the areas of environmental noise and vibration testing, analysis and design of mitigation systems, and real-time remote noise and vibration monitoring for numerous industries. He serves as the Energy, Environmental and Transportation Co-Market Leader at Acentech responsible for marketing strategy, client development, and industry thought leadership.
This article is an expanded version of one originally posted by Acentech.