As the global energy market, piece by piece, slowly but surely, moves towards a renewables-centred paradigm, dispatchable solar and uncurtailed wind, along with other forms of clean energy, are requiring longer and longer durations of storage to integrate them to the grid. While there’ll be a place for lithium-ion for many years yet, the technology really excels at applications of up to around four hours. For everything else, there’s a growing list of contenders, with diverse technologies and at different stages of commercialisation. Here’s a handy guide to some of those technologies and their providers, electrochemical and otherwise, that promise anything from five hours to even days or weeks of storage.
Enjoy 12 months of exclusive analysis
- Regular insight and analysis of the industry’s biggest developments
- In-depth interviews with the industry’s leading figures
- Annual digital subscription to the PV Tech Power journal
- Discounts on Solar Media’s portfolio of events, in-person and virtual
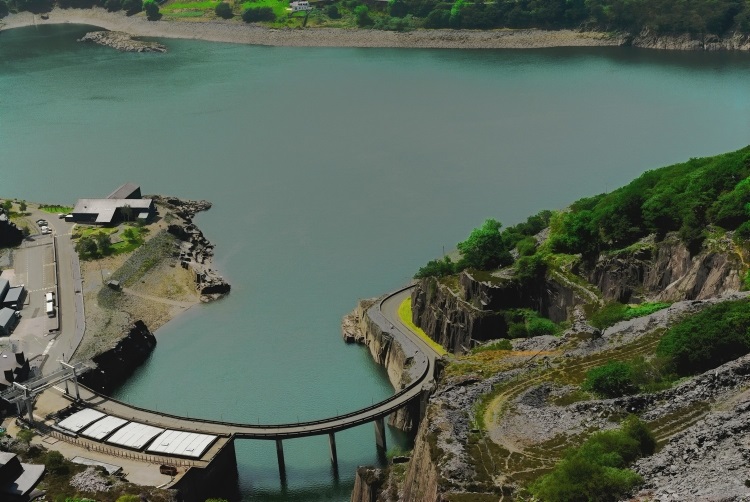
Who’s got a head start
Pumped hydro
It’s worth remembering that more than 90% of the world’s installed base of energy storage in megawatt-hours is still pumped hydro. Lithium-ion may take the plaudits and the new market share today, but historically, the legacy of pumped hydro remains huge.
Water is elevated using pumps into a retained pool behind a dam. When electricity is required, the water is unleashed and runs through turbines, which then creates electricity. While the amount of energy required to pump the water back up is far less than the amount generated as it falls, systems can also be paired with renewable generation to pump the water back to the top. However, while the system is cheap once built and can last for many years, finding appropriate sites and getting permission to build pumped hydro plants remains an obstacle to widespread further development in most parts of the world.
In June 2019, Australia-based firm Genex Power announced it was set to receive a second round of debt funding from the Northern Australia Infrastructure Facility (NAIF), for what will be the world’s first pumped hydro project to utilise an abandoned gold mine.
In Chile, a 300MW pumped hydro project is under development, having recently received an injection of US$60 million in fresh funding from the Green Climate Fund. The Espejo de Tarapacá project, which will also see a 561MW solar PV plant, is being developed by Chilean renewable developer Valhalla and construction is set to begin next year.
French energy giant Engie is also a proponent of the technology, with its First Hydro Company owning the Ffestiniog and Dinorwig pumped hydro assets in Wales. Engie lauds Dinorwig as the fastest power generation asset in the UK, with the ability to deliver 1.7GW in 16 seconds.
Sodium-sulfur (NAS) batteries
Also fairly well established today, Japanese firm NGK has been working on its NAS sodium-sulfur batteries for over three decades. R&D of the Beta Alumina electrolyte, a key component
of the system, began in 1984, with the development of the NAS itself beginning in 1989. NGK worked in collaboration with Japanese energy giant TEPCO for the development of the technology and is the only maker of large-scale sodium-sulfur batteries.
The batteries have a six-hour discharge at rated output and between 14 and 18 hours at one-third rated output. A project completed this year in Abu Dhabi, the capital of the United Arab Emirates, demonstrated the technology’s six-hour duration, with 15 systems totalling 108MW/648MWh. The battery has a relatively high upfront cost versus lithium, but the longer duration gives it an edge, as well as its potential scalability, which puts it ahead of flow batteries, the company claims.
Two types of units are on offer from NGK: the plug-and-play style system consisting of four container subunits, each of which includes six NAS modules, each of those rated at 33kW/200kWh, is one such unit. The second, package type unit, has a rated output of 1,200kW/8,640kWh, made up of 40 NAS modules, each rated at 30kW/216kWh. With an expected lifetime of 15 years, the system is set to see 4,500 cycles, making that 300 per year.
As is perhaps evident from the name, the two active materials of the battery are sodium and sulfur. The positive electrode houses the sulfur, the negative electrode the sodium. A third component, Beta Alumina ceramic, is mounted between the sodium and sulfur as the electrolyte. The active materials are liquid, the electrolyte a solid. NGK, which has a background in industrial ceramics, opened a plant in Aomori, Japan in 2008 with a capacity of 34MW/245MWh, co-located with a 51MW wind farm owned by Japan Wind Development, helping to stabilise the wind output, as well as contributing to the farm meeting the server grid code of Tohoku Electric and selling the electricity to Japan Electric Power Exchange. Much more recently, it sealed a partnership deal with chemicals giant BASF for the provision of NAS batteries.
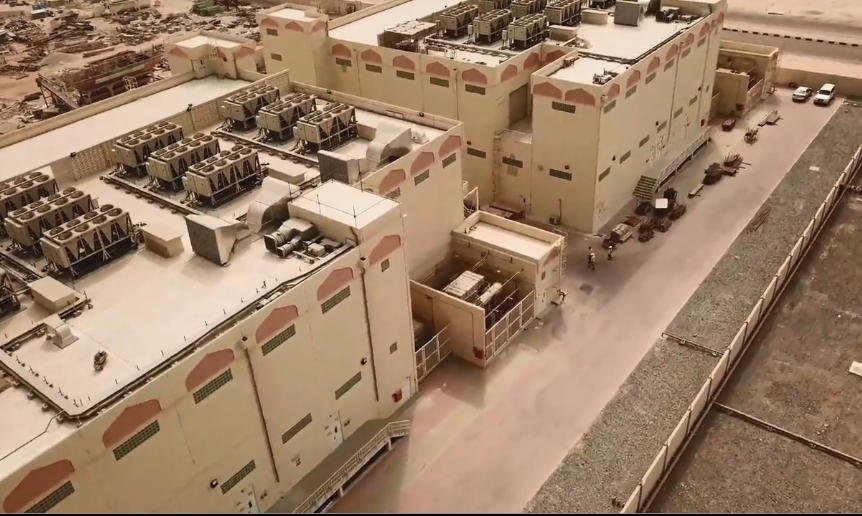
Flow batteries
Unlike some of the others in this list, flow batteries are being delivered by a number of companies. And while the industry has already seen some contenders come and go, a recent report from Navigant Research named 12 ‘leaders’ of this nascent segment. A number of providers including Japan’s Sumitomo Electric, UK-based redT and others use vanadium electrolyte pumped through tanks, while others, including US-based Primus Power and Australia’s Redflow, use zinc bromine electrolyte. ESS Inc, meanwhile is the only producer of a patented ‘all-iron’ flow battery.
During discharging, a redox reaction occurs, changing the composition of the electrolyte, which then results in an excess of electrons at the negative electrode. Electrons flow from the negative electrode to the positive, and it’s this flow that generates an electrical current. This can then be reversed by applying an electrical current to the electrodes, charging the system. Again, while more expensive than lithium-ion upfront, its durability, ability to cycle heavily without degradation and ability to scale up with the volume of electrolytes in the tank simply representing more energy for longer, mean that providers and technology enthusiasts alike are excited by flow batteries.
Flow batteries essentially offer the chance to decouple power and energy supply, with the power determining the cell size and the energy determined by the amount of the electrolyte in the tanks.
In July 2019, redT achieved pre-qualification status for a 300kWh flow machine into the UK’s dynamic firm frequency response market, thought to be the first occurrence of a flow battery providing ancillary services to the grid. It is currently nearing completion of a proposed merger with Avalon Battery, provider of flow batteries to rapidly growing US solar technology provider NEXTracker.
Flow batteries have seen increasing deployment in a number of applications including for remote communities and telecoms sectors, while there are now also a few megawatts of hybrid systems using flow alongside lithium-ion in action. Read this edition of PV Tech Power’s in-depth look at flow batteries by authors from CENELEST, a joint research venture between the Fraunhofer Institute for Chemical Technology and the University of New South Wales (free download here).
Think zinc
A number of players are working with zinc as a primary material including several start-ups deep into stealth mode. One company already deploying zinc in the form of a zinc hybrid cathode battery is Eos Energy Storage. Founded in 2008, its ‘Aurora’-branded zinc cathode battery has a 3-6-hour continuous discharge capability. Mechanically, the technology resembles a flooded lead acid battery, Eos VP for business development Philippe Bouchard says, but “we’re plating and re-plating zinc as we charge and discharge the system”. Eos also claims the chemistry uses widely available materials, meaning there are no supply chain constraints.
“Because it’s an aqueous chemistry and because there’s no material degradation of the electrode, this battery can charge and discharge at 100% DOD [depth of discharge] for up to 20 years,” Bouchard says, which gives the technology a “big competitive advantage”.
Back in October of 2016, Eos raised proceeds of US$23 million through the initial closing of a private placement transaction, at the time saying it planned on using the money to increase deployment of its battery storage product. A year later, the developer had bagged several deployments in various corners of the world, including a 1MWh Aurora system at a wastewater treatment plant in New Jersey, its home state. Also in 2017, utility Engie announced it would install a 1MW/4MWh Eos system in Brazil.
Along with a recently brokered UK distribution deal, a 10MW/40MWh project in California – originally announced in 2015 – is still set to go ahead for developer Convergent Energy + Power, although having been awarded by troubled utility PG&E, there may be question marks in the immediate term over that project’s timeline. Perhaps most significantly, Eos now has a North America manufacturing joint venture (JV) with nuclear decommissioning equipment maker Holtec, called HI-POWER.
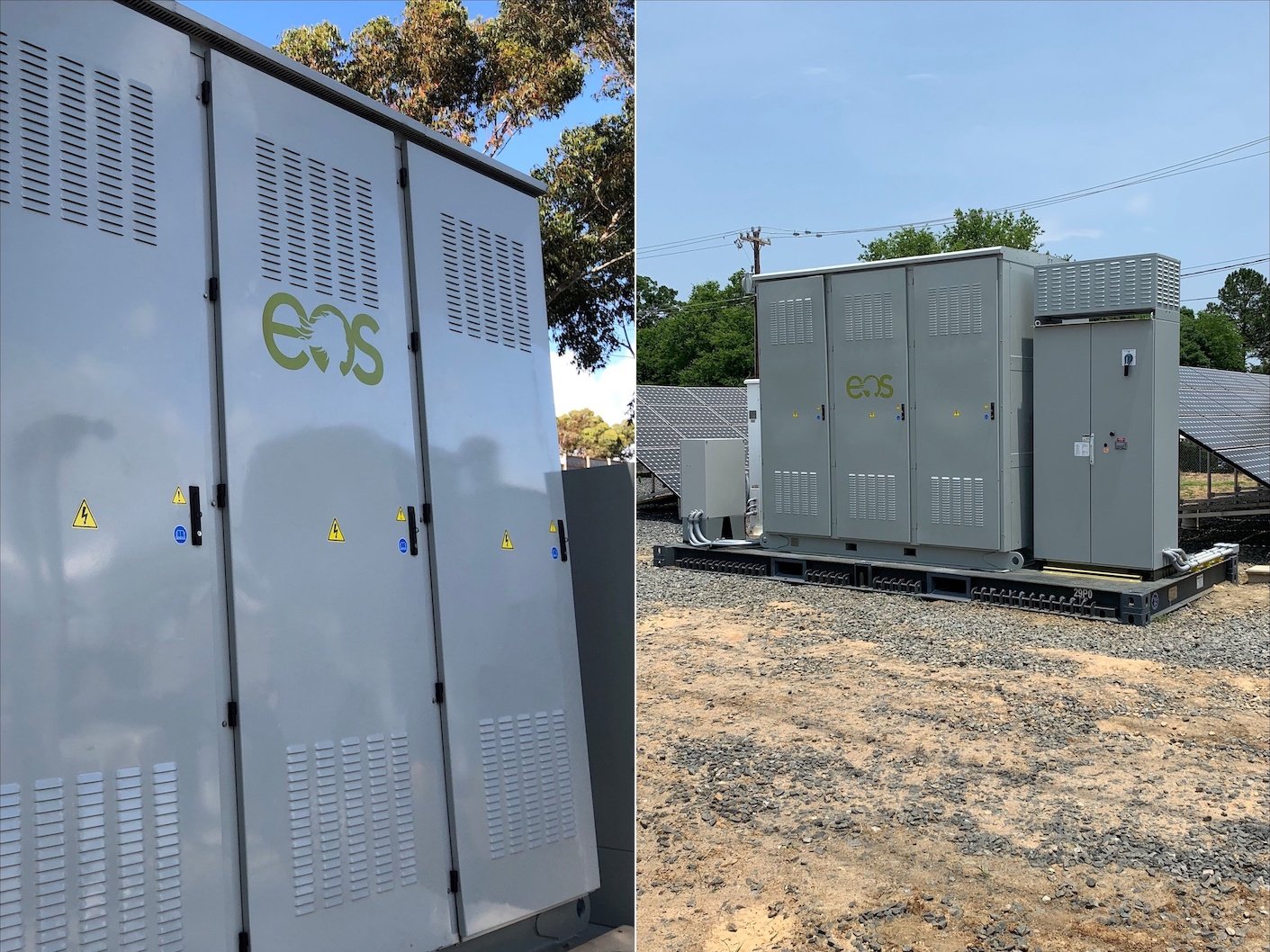
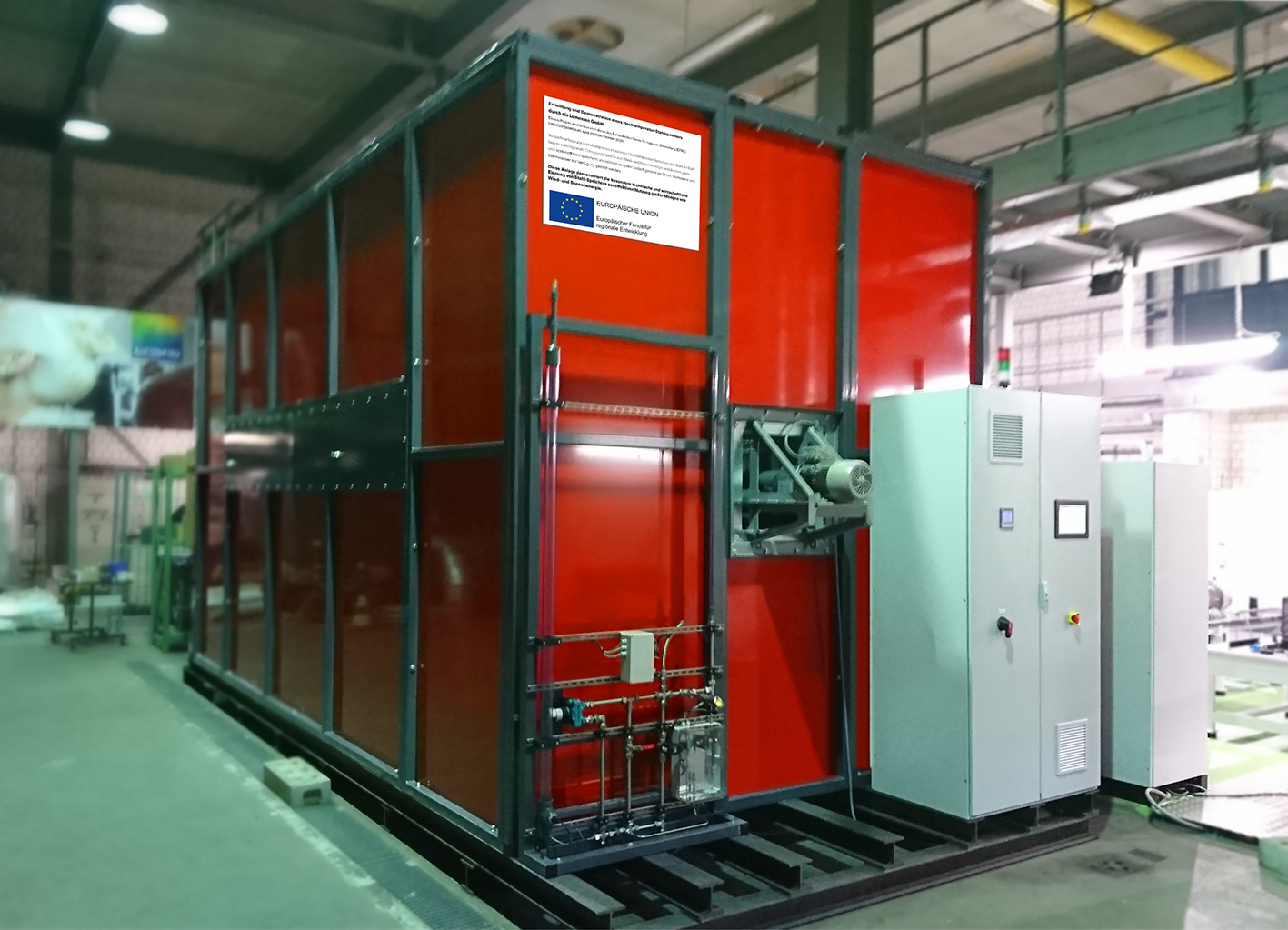
At the starting line
Copper-zinc rechargeable battery
When Alessandro Volta dreamt up the first battery in 1799, copper and zinc were the electrodes. Fast-forward to 2014, when Cumulus Energy Storage developed a patented system for making copper/zinc rechargeable using an ionically permeable separator.
As the battery is charged, the copper electrode releases copper ions into the electrolyte, and zinc ions electro-win onto the zinc electrode. When it’s discharged, the reverse then occurs. As long as the zinc and copper ions are prevented from migrating to the opposite electrode the battery can be electrically charged and discharged for thousands of cycles, Cumulus claims. Potential benefits include a lifecycle of 30 years and scalability, as its bipolar design means individual cells can be added in series to meet the desired voltage. It is also 98% recyclable at the end of life.
Copper and zinc are the 25th and 26th most abundant materials in the earth’s crust, while the battery technology has an anticipated round trip efficiency of over 80%.
Cumulus’ batteries can participate both in the high-energy, long-duration market, as well as ancillary services, due to the chemistry of the battery being aqueous, meaning the response time is “very, very quick”, Cumulus CEO Nick Kitchin says.
Cumulus was inspired by the mining industry, from electrorefining – the process of extracting zinc and copper from electrolyte – using plants often operating in the range of hundreds of megawatts.
“What we’ve done is we’ve made those processes smaller, we’ve reduced our development costs and run-time as a consequence of that and we’ve de-risked the whole process. We’ve gone in the opposite direction to lithium, which is taking something small and making it big. We’re taking something big and making it smaller,” Kitchin says.
Cumulus has R&D facilities in California and is developing battery manufacturing in the UK. The company has a Series A funding round currently underway and Series B planned for October 2020. “No one else can do this,” Kitchin says, adding that demonstrator systems are currently being put in place, with the company also hoping to announce a large project in Ireland soon.
Liquid metal batteries
Understood to still be at an early stage of commercialisation, start-up Ambri’s liquid metal batteries spawned out of the GroupSadoway lab at the Massachusetts Institute of Technology. They comprise a liquid calcium alloy anode, a molten salt electrolyte and a cathode made of solid particles of antimony. This enables the use of low-cost materials and a low number of steps in the cell assembly process, Ambri says.
The active materials in the cells reversibly alloy and de-alloy while charging and discharging. Ambri batteries boast no degradation and are expected to have a 20-year lifetime, with a nominal capacity of 800Ah and nominal continuous power of 160W. The response time comes in at <500 milliseconds, while the cost of the systems comes in at half the cost of lithium-ion when comparing 20-year, eight- hour-duration systems. This is due to the manufacturing of the cells being simpler and the systems not requiring cooling, fire suppression or module- and rack-based BMS equipment unlike lithium ion-systems.
However, the company is yet to put cells into systems. A deal struck this year with NEC makes a commitment to doing that. NEC’s Energy Solutions division is expected to make a minimum purchase of 200MWh of cells for systems delivering applications that go to five hours of storage – or more. NEC’s Roger Lin also suggested that in addition to good degradation character- istics, the cost of the technology would be “competitive to or just a little bit less expensive than lithium”, but that this stage it’s “hard to say how it will all [really] end up”. However, whilst the cell characteristics and performance of the cells is under- stood, there are still two years of development ahead for the technology. One of the challenges is Ambri’s low voltage in comparison to lithium-ion, with the cells at one volt compared to around four, meaning four times as many Ambri cells are needed compared to lithium-ion to get the same high voltage stack.
Hot, hot heat: Thermal steel at 650°C
Lumenion’s thermal energy storage has been deployed as a multi-megawatt demonstration, storing electricity as high-temperature, 650°C heat in steel.
It can then either be used as heat or converted back to electricity through the use of a steam turbine. The storage can continuously supply thermal energy with temperatures of 80-550°C for around 48 hours, with a charging pattern of eight hours out of 48. The charging to discharging ratio can be 1-5 or 3-5 depending on the application of the storage, and Lumenion claims it has an efficiency of 95% using the principle of combined heat and power (CHP).
In October 2018, the company announced it was partnering Swedish utility Vattenfall and municipal housing company Gewobag for a 2.4MWh thermal energy storage system in Berlin, Germany. It’s recommended by Lumenion as the answer to large-scale, bulk storage and as a complement to faster-responding assets such as batteries.
The system will absorb power generated by local renewables plants, wind and solar, stored at a claimed cost of less than €0.02 per kWh. The technology relies on no rare earth minerals and as company CEO Alexander Voigt points out, there are already plenty of ‘gigafactories’ producing steel around the world. One to watch.
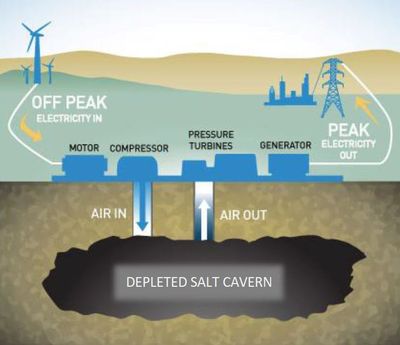
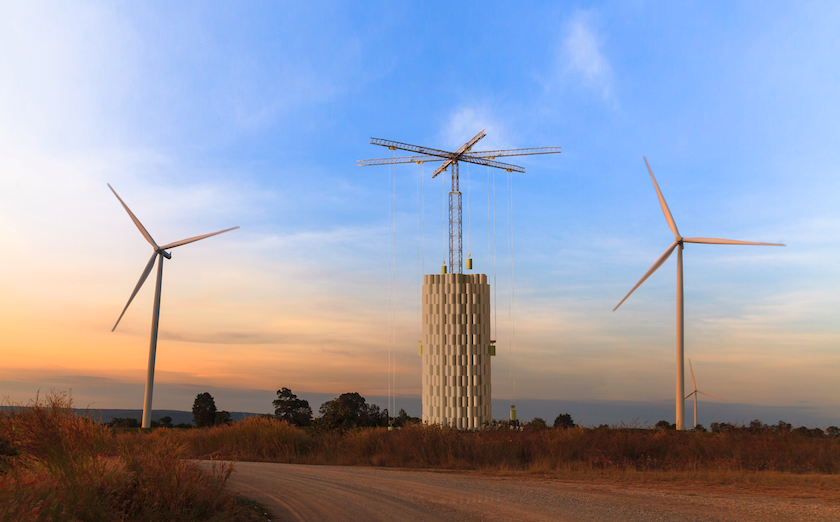
Liquid air & advanced compressed air (LAES, A-CAES)
UK-headquartered Highview Power announced a 50MW/250MWh ‘cryobattery’ project in October 2019, a technology kicked off in 2005 by researchers at the University of Leeds in England. The company’s first pilot plant was operational between 2011 and 2014. Cryobatteries cool ambient air to below -270°F (-170°C), causing a 700-fold contraction in its volume from gas to liquid. This liquid air is then stored in conventional insulated tanks at low pressure and when energy is required, the air is warmed again and pumped to pressure.
It is then expanded back to gas, this time increasing in volume 700 times over, through a standard expansion turbine connected to a generator. The system’s expected lifespan of 30+ years is one of its key benefits, with the system also having no geographical constraints on where it can be deployed. Highview claims it as the lowest-cost locatable technology at utility scale. The technology can be built from 10MW to 200MW+ power output, with a storage capacity of 40MWh to over 20000MWh+, the company claims.
Highview has signed a deal with EPC partner TSK for marketing its systems into Spain, the Middle East and South Africa. Currently, only two of the systems have been deployed, although there are plans for five 250MWh systems at as-yet unrevealed locations in the UK.
Another company to be utilising air – though in a different fashion – is Hydrostor. Hydrostor claims its A-CAES plants are the lowest installed cost per kWh for large-scale, long duration energy storage. It has a 30+ system life, with unlimited cycling and no replacement required, according to the company.
The technology uses off-peak or surplus electricity from the grid, or from a renewable source, to run a compressor, which produces heated compressed air. Heat is then extracted from the air stream and stored inside a proprietary thermal store.
Air is stored inside a purpose-built underground cavity, where hydrostatic compensation keeps the system at a constant pressure. Hydrostatic pressure forces the air to the surface, where it is re-heated by the thermal store and expanded through a turbine, which generates electricity. Hydrostor says that this re-use of thermal energy is what makes so-called adiabatic advanced compressed air energy storage (A-CAES) so efficient. It is ideally situated for use in behind-the-meter or remote applications for mines and large industrial operations, Hydrostor says, with a duration of between four and 24+ hours.
In July, Hydrostor secured approval to build the first grid scale application of the technology in Australia. The system comes in at 5MW/10MWh, with the location a former zinc mine near Strathalbyn, South Australia. Hydrostor also completed work on a multi-megawatt, commercial system in Canada in November. The project had been under joint development with NRStor since 2017 and is 1.75MW peak power output rating. It has a 2.2MW charge rating, with a 10MWh+ of storage capacity.
It’s all in the gravity
Using gravity to store energy boils down to releasing a weight and converting the kinetic energy of the fall into electricity. There are a handful of providers in this area. However, the technology proposed by one start-up implies a surprising level of complexity.
Swiss start-up Energy Vault was inspired by pumped hydro power stations to create its gravity-based energy storage solution.
Concrete blocks weighing 35 metric tonnes are lowered up and down an energy storage tower, storing and releasing energy as they go. As the bricks are lifted, energy is stored in the elevation gain. As they are returned to the ground, the kinetic energy generation from the falling brick is converted into electricity. The system uses control software to make sure the bricks are placed in the right location through which Energy Vault touts “very fast response times”.
It claims a lifespan of 30+ years with zero degradation and 90% round trip efficiency. The storage can deploy 4-8MW of continuous power for 8-16 hours. Energy Vault received a US$100 million boost in the form of an investment from SoftBank Vision Fund in August 2019. It is deploying its first 35MWh tower in northern Italy and has an agreement to build another for India’s Tata Power Company.
The verdict
Speaking on a panel at this year’s Solar & Storage Live event in the UK, NGK’s business development head Gauthier Dupont said that NAS batteries and other promising – or even proven – long duration technologies may not currently get the headlines, but if they are to compete, they certainly need to start getting the investment that lithium-ion, the ‘sexier’ technology, attracts. For many technologies it will be a question of access to manufacturing facilities of appropriate size that will drive scale and therefore cost reductions.
For others, it’s a question of getting proven through successful deployment beyond the pilot phase and for others still, it remains a matter of technology development. And while they can’t all be the ‘cheapest’ as they claim, there’s probably room for diverse long duration technologies in tomorrow’s world. One thing is for sure, the race is on, and the window to deliver is getting shorter, even if the hours of energy stored and discharged are going to get longer.
Cover image: Highview Power’s original multi-megawatt demonstrator, now to be joined by vast projects in the UK and US. Credit: Highview Power.
This article originally appeared in “Storage & Smart Power’, Energy-Storage.news’ contributed section of the quarterly journal PV Tech Power (Vol.21), available as a free PDF download, here.