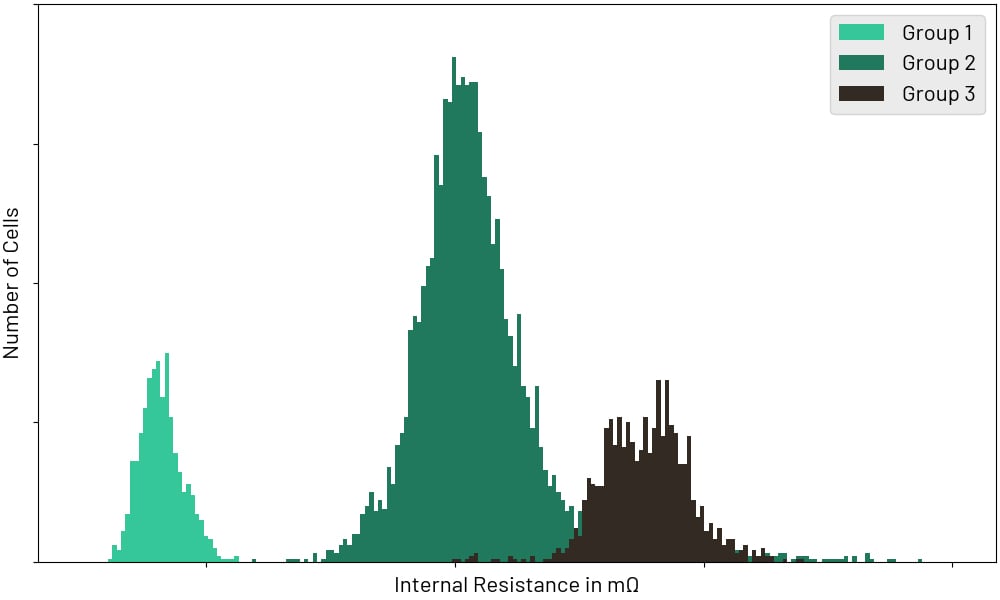
The BESS commissioning phase is the first and crucial operational step for companies to become profitable with big batteries. Dr Kai-Philipp Kairies of ACCURE provides insights into typical technical commissioning challenges and how advanced battery analytics can support owners and operators.
This is an extract of a feature which appeared in Vol.35 of PV Tech Power, Solar Media’s quarterly technical journal for the downstream solar industry. Every edition includes ‘Storage & Smart Power,’ a dedicated section contributed by the team at Energy-Storage.news.
Enjoy 12 months of exclusive analysis
- Regular insight and analysis of the industry’s biggest developments
- In-depth interviews with the industry’s leading figures
- Annual digital subscription to the PV Tech Power journal
- Discounts on Solar Media’s portfolio of events, in-person and virtual
In this article we examine four typical technical challenges BESS assets face at the beginning of their lifecycle and how battery analytics can help to overcome them. All are based on real-life BESS projects with sizes between 20MW and 200MWh. Insights are anonymised and modified to respect the confidentiality of ACCURE’s customers.
1. Battery cell quality
Battery cells are the heart of a BESS; their quality makes or breaks a system’s ability to provide value. But high battery quality is not a given. Even the best cell manufacturing lines have significant scrap rates and produce batteries of varying qualities. New cell chemistries, exponential growth, accelerating product development cycles, and the advent of new suppliers hyper-scaling into the market have not improved this situation.
Today, the industry typically uses end-of-line (EOL) testing and sorting at the factory to ensure a minimum cell quality and to deal with the inevitable spread in cell properties during battery production. One typical test is to use an AC power source providing a current pulse at 1,000 Hz to measure the internal resistance of the cells. Cells with similar properties are grouped, and outliers go straight to recycling. Internal resistance is not typically evaluated during commissioning and operation, but it should be. Today, internal resistance can be tracked by combining battery management system (BMS) readings and advanced cloud computing capabilities.
In Figure 1 above, ACCURE’s advanced cloud analytics platform depicts the distributions of internal resistances in a BESS shortly after its commissioning. The batteries fall into three distinct groups:
(a) The left-most group shows highly desirable properties: The distribution of internal resistances is centered around a low value and has a small standard deviation. The EOL testing and sorting at the factory clearly worked here.
(b) The middle and right group show the opposite: The distributions are centered around higher values, with higher standard deviations. In layman’s terms: The cells in the middle are B stock, the cells on the right are trash.
A deeper look into the electric and electrochemical properties suggests that the cells came from different production batches and probably used different components (e.g., a different electrolyte or separator). It was also clear that the right group did not fulfill the quality criteria promised to the client. These battery cells were liabilities.
2. Battery management system (BMS) failures
The BMS is the brain of a battery. It ensures the battery is not operated outside of its specifications and provides abstract values like state of charge (SOC) to the overlying energy management system. To operate, it continuously tracks the voltage, current, and temperature of all battery modules. If a sensor fails or the BMS logic is corrupted, potentially dangerous situations can arise:
- Unexpected shutdown of a battery rack because the BMS (falsely) believes a battery has reached its operational limits
- Erroneous SOC calculation, leading to an underutilization of the asset and increasing system imbalance
- Deep discharging, leading to the dissolution of copper from the anode tab and the risk of internal short circuits
- Overcharging, leading to a thermal runaway event
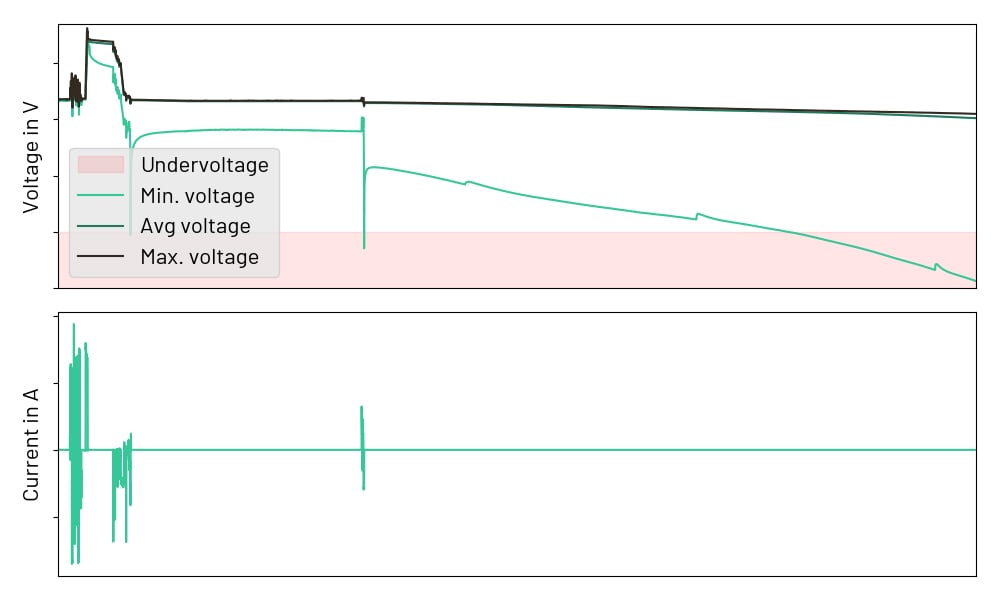
Figure 2 shows a case of deep discharging that happened during commissioning. During commissioning, deep discharges can easily occur by accident – through parasitic loads or faulty active balancing. If a battery is deep discharged beyond a certain depth and duration, its warranty can be voided, and it can no longer be considered safe. The dissolution of copper can lead to internal short circuits weeks for months later. Such a battery needs to be taken out of operation. Digital monitoring can inform these discussions.
3. SOC errors and imbalanced racks
Since 2020, most new BESS use lithium-ion LFP batteries rather than NMC. These batteries generally have a higher raw material availability, lower costs per kWh, and a lower energy density. This lends itself well to stationary applications. However, one major challenge when working with LFP batteries is SOC estimation.
Figure 3 shows the SOC of a BESS during a late part of the commissioning phase. The greater than 30pp SOC difference between the racks is striking – and in this case incorrect. Using cloud-based algorithms, it was shown that the actual spread at the time was significantly smaller and that some of the initiated balancing activities actually increased the problem. In the given example, the error was pinpointed using ACCURE’s cloud-based analytics, and the issue was quickly addressed through recalibration.
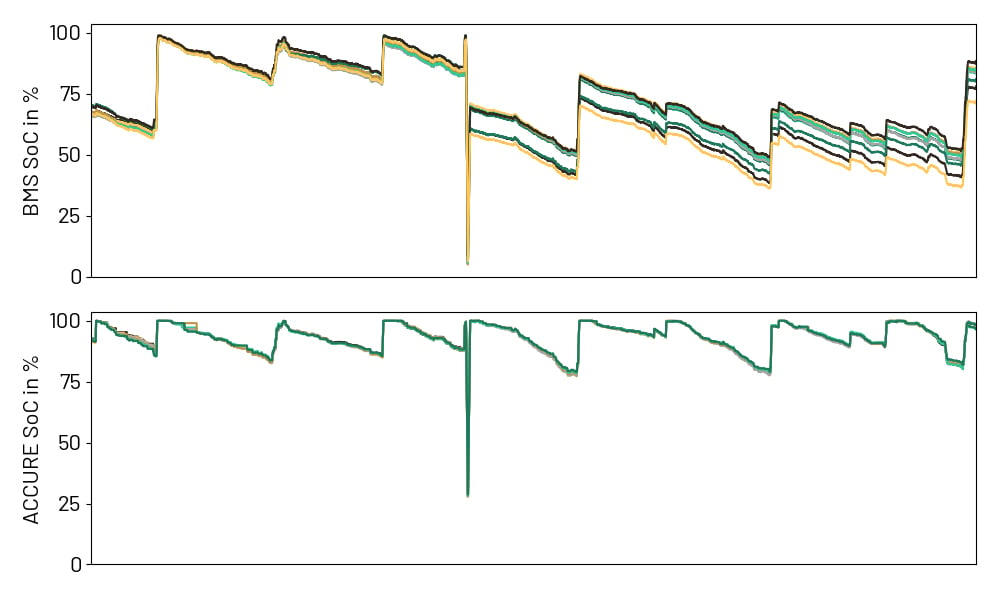
4. Water leak and heat damage
Problems with water have been a repeated source of worry for BESS. Failures of the cooling or fire suppression system started several high-profile fires over the past few years. But not every water issue automatically leads to a fire. And if the water did no apparent damage, a contractor might be incentivised to find pragmatic ways to deal with seemingly minor incidents.
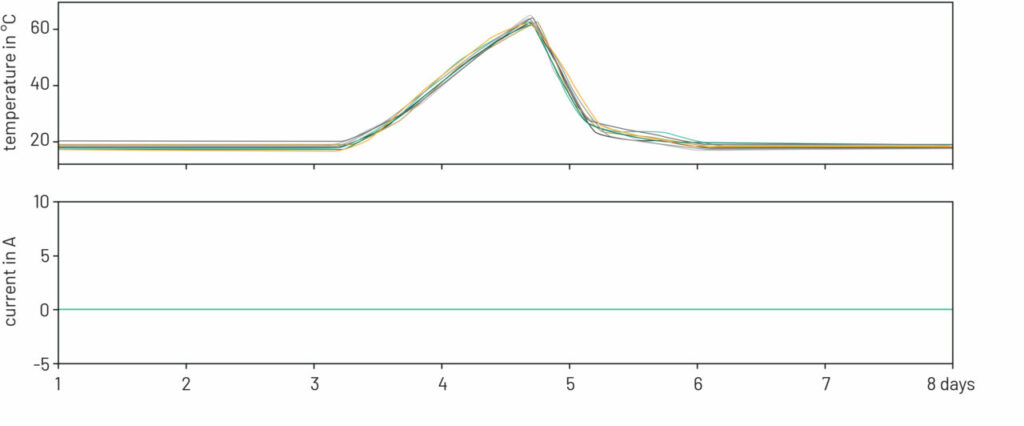
a BESS.
One example of such a pragmatic solution was found by ACCURE when analysing the temperatures of battery containers during the commissioning phases. One plausible solution to this riddle is using a dehumidifier after water damage. It was probably well-intended. However, it had violated the battery’s warranty conditions.
This is an extract of a feature which appeared in Vol.35 of PV Tech Power, Solar Media’s quarterly technical journal for the downstream solar industry. Every edition includes ‘Storage & Smart Power,’ a dedicated section contributed by the team at Energy-Storage.news. Access to PV Tech Power, including more than five years of back issues, is part of the Energy-Storage.news Premium subscription package.
About the Author
Dr. Kai-Philipp Kairies is a scientist and entrepreneur focusing on innovative battery energy storage solutions. He worked as a battery researcher and consultant in Germany, Singapore, and California.
Since 2020, he is CEO of ACCURE Battery Intelligence, a battery analytics solution provider that supports companies in understanding and improving their batteries’ safety and longevity to reduce risk and increase value and sustainability.