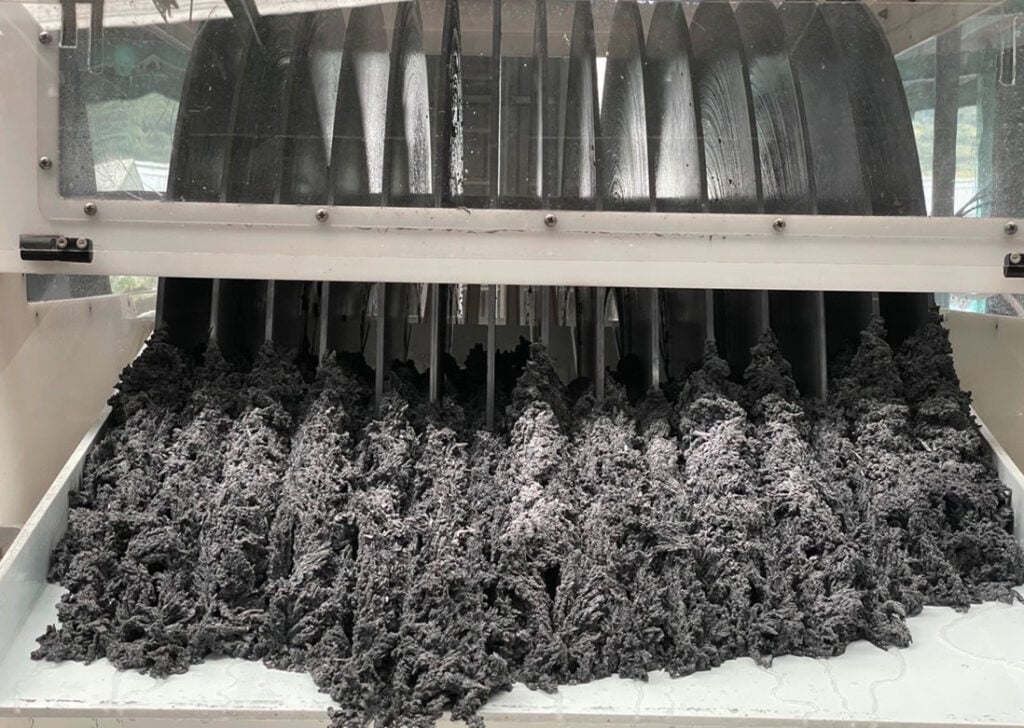
The rapid growth of the energy storage system (ESS) and electric vehicle (EV) markets is going to mean substantial quantities of end-of-life lithium-ion batteries which need to be either recycled or re-used in the coming years.
The US government is providing substantial financial support to its own nascent lithium-ion recycling sector, with government-backed loans of US$2 billion to Redwood Materials and US$375 million to Li-Cycle, US$480 million in grants to Ascend Elements and US$192 million for a range of battery recycling projects.
Enjoy 12 months of exclusive analysis
- Regular insight and analysis of the industry’s biggest developments
- In-depth interviews with the industry’s leading figures
- Annual digital subscription to the PV Tech Power journal
- Discounts on Solar Media’s portfolio of events, in-person and virtual
However, as Energy-Storage.news wrote last week in a Premium article, Li-Cycle is facing serious issues after the costs for its hydrometallurgical recycling plant in Rochester, New York, nearly doubled to up to US$1 billion.
The hydrometallurgical process, or hydromet, of separating black mass into the critical metals needed for batteries, namely lithium, cobalt and nickel, is the tech opted for by most in the industry, but other processes exist.
Aqua Metals, a US company with a novel lithium-ion battery recycling technology, claims its process is cheaper and more sustainable to commercialise than conventional methods.
In this Q&A, the company’s VP of commercial David Regan discusses this as well as its work with the ESS market and the challenge of fluctuating prices amongst the metal commodities from which it will generate its revenue. Some of these comments were included in our piece on Li-Cycle and Aqua Metals last week.
Can you briefly summarise how AquaMetals’ process has such lower carbon emissions than conventional hydrometallurgy?
The largest source of carbon dioxide equivalent or CO2e for a standard hydrometallurgical LIB recycling operation is the carbon footprint of each trainload of chemicals required for operations, particularly sulfuric acid, hydrogen peroxide, and sodium carbonate.
Standard hydromet is a chemical intensive process, leveraging a series of chemical reactions and pH adjustments to separate valuable metals, typically as battery metal salts. Each of these steps consumes chemicals and produces a byproduct that must be treated, stored, and ultimately shipped to landfill. This solid waste management adds an additional cost and carbon footprint as well as the potential for acidification and ecotoxicity.
Aqua Metals’ AquaRefining process receives the same shredded, recycled battery waste (called “black mass” in the industry) as a standard hydrometallurgy process, but instead of introducing one-time-use chemicals, we use electrons as sustainable reagents via electroplating to extract the valuable metals using electricity. This means eliminating the reactions that require a constant supply of chemicals and produce landfill waste as a byproduct.
The scope of the carbon footprint for AquaRefining is primarily driven by the electricity we are able to source ourselves or from the electric grid. The ability to use low-carbon and carbon-free electricity sources means we have a clear pathway to net-zero lithium battery recycling. The decarbonisation of one building’s electricity supply is far simpler than the combined chemical and transportation sectors.
Do you foresee receiving many volumes from the ESS market?
Yes, stationary energy storage systems will play a not-insignificant role in lithium battery recycling, but they will be exceeded by the flood of EV batteries for two reasons. First, there are vastly more EVs expected than stationary ESS by weight, and the typical EV battery is three to four times larger than a comparable home battery. Second, EV batteries will wear out much faster than stationary systems, due to higher power loads and more aggressive charging of EV batteries.
However, manufacturing scrap will be a primary source of recyclable materials for the foreseeable future, and that includes sourcing stationary ESS materials. Cell manufacturers produce a large amount of scrap material – whether EV batteries or stationary ESS – and that material will be first to enter the circular recycling supply chain.
Are ESS project owners organising recycling deals significantly in advance of the batteries actually reaching the end of their life?
We have spoken to many system owners and large operators looking to establish long-term offtake agreements. For example, a global data center operator that has been using lithium batteries for years is now looking to recoup some value and get the battery system removed when it reaches its end of life.
Those types of large system operators are looking for a solution, often with a mix of some in-hand and soon-to-be-retired batteries available for recycling.
How do you hedge against fluctuating prices for the metal commodities that you will be generating revenue from?
Battery recycling has a fascinating aspect that’s often overlooked: the potential for price arbitrage due to the rapid fluctuations in the value of critical minerals. We base our payment terms on a range of factors, notably including current spot prices from sources like the London Metals Exchange (LME) or FastMarkets.
Our approach to acquiring black mass hinges on the metal content. When we buy the black mass to recycle, it costs a percentage of the LME value of its composite metals. So, both our feedstock and product pricing will fluctuate with the values of the metals we receive and deliver.
How much will your commercial-scale facility cost and will additional project-level financing be needed for it?
Our Sierra ARC recycling campus is projected to cost roughly US$100 million in total CAPEX to build 10,000 tonnes of annual black mass recycling capacity (around 100,000 EV battery packs).
Aqua Metals has raised funding to advance the first phase of this project (3,000 tonnes per year) and will be seeking additional funds to complete the campus by 2026. This could include a combination of government loans or grants, traditional debt financing, and other financial instruments.
How does the cost compare to conventional hydrometallurgy?
Based on recently-updated projections from hydromet recycler Li-Cycle, it costs upwards of $1 billion to build a 35,000 tonnes-per-year facility (US$28,000 per tonne of capacity). Aqua Metals is currently on schedule and on budget with the first phase of our 10,000 tonnes-per-year campus outside Reno, Nevada, with a projected cost of US$100 million (US$10,000 per tonne of capacity), 60% less in upfront capital expenditures.
It is difficult to compare apples-to-apples for operating costs, as only a couple of recyclers are operational at meaningful scale in North America. There are no commercial hydrometallurgical facilities producing battery grade products in the Western hemisphere today.
The operating costs of AquaRefining are projected to be much lower because chemical supply and storage costs are minimised and replaced with stable and predictable utility electricity pricing. These cost savings translate directly into margin for each tonne of material recycled using AquaRefining.