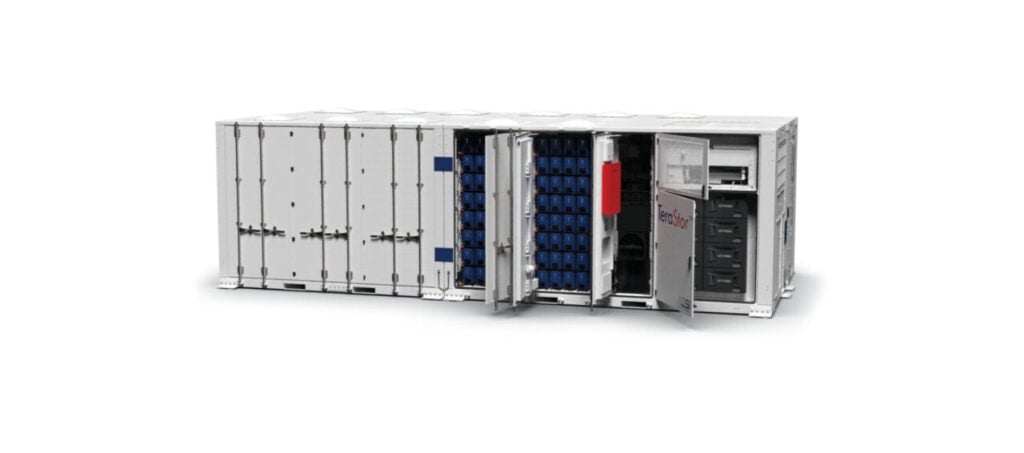
Energy-Storage.news Premium hears from Bud Collins, CEO of American Energy Storage Innovations (AESI), about its BESS technology, battery cell strategy, manufacturing in East Asia and the “shocking” price of manufacturing in the US and buying US-made cells.
Collins has an impressive energy storage CV, having been VP engineering at A123 Systems when it designed what may have been the world’s first grid-scale BESS project for AES, deployed at several substations in Southern California in 2008. Later, he was CEO of NEC Energy Solutions from 2014-2017, during which time it became the largest system integrator in the burgeoning energy storage industry.
Enjoy 12 months of exclusive analysis
- Regular insight and analysis of the industry’s biggest developments
- In-depth interviews with the industry’s leading figures
- Annual digital subscription to the PV Tech Power journal
- Discounts on Solar Media’s portfolio of events, in-person and virtual
Fast forward nearly a decade and AESI was officially spun out of American Battery Solutions (ABS) last year to commercialise the company’s TeraStor battery energy storage system (BESS) product, launched in 2022. TeraStor is an AC block solution, coming with power conversion systems (PCS) integrated with its batteries.
In this interview, Collins discusses the main industry challenges that drove his firm’s product design, its pipeline and strategy to scale, and its manufacturing which, despite the name, will not be in the US anytime soon.
‘Accept you are not an EPC firm’
“To make money you have to accept you are not an EPC (engineering, procurement and construction) firm or a system integrator, you have to be an an equipment OEM,” Collins says.
It’s an interesting point considering that many leading system integrators have, or still do, provide both, and not always successfully.
He says that AESI and TeraStor were launched to solve four major energy storage industry challenges, namely fire safety, the need to minimise the role of EPC firms (which Collins says is a major bottleneck), reliability/availability and BESS architecture’s limitations in harmonising discharge across cells.
“The first thing we needed to address was fire safety. As an industry, we need zero cell-to-cell propagation. If you can achieve that, when you get thermal runaway—and you will—you can keep it to one cell, and it won’t be more than a 30-45 minute event with some smoke coming out of a box. We achieve that with our system,” he claims.
“We also have to minimise the EPC’s role in deploying energy storage. We need to make it so easy to put in that it takes a very small crew, very little time, and so when it is installed it runs. It shouldn’t be months of commissioning and making all the systems talk to each other. That was the genesis of TeraStor, which can be installed in six hours and is built and tested in the factory as a system.”
That ease of installation is cited as a major driver of a potential shift to more companies offering AC block solutions, explored by Energy-Storage.news in an article a fortnight ago. However, some industry sources say AC blocks have limitations vis-a-vis flexibility for deployment and augmentation that mean they won’t become the industry standard.
Reliability, availability and logistics
Another potential driver for AC block adoption is better reliability and the ability to average out battery cells’ discharge to prevent one bad-performing cell dragging all others down, using string inverters.
“The third thing we focused on was reliability. These are pieces of critical infrastructure and need to be at the level of data centres. Through third-party analysis we have five nines (99.999%) reliability,” he claims.
“The final thing – everyone has copied that original design of a rack, BMS, shared bus. You don’t get that 5MWh of charge if you have a weak cell in conventional BESS which have series over parallel architecture. Our is parallel over series architecture, which averages the cells, strong or weak, for repeatable capacity. We can also get really accurate state of charge (SOC) and state of health (SOH), better than 98%.”
TeraStor uses lithium iron phosphate (LFP) cells, as most BESS do, which are harder to estimate SOH and SOC for than nickel manganese cobalt (NMC) cells.
Collins also claims that the TeraStor is stackable thanks to its system design, though it does require special equipment to service. Double-stacking BESS is rarely done because of weight and fire safety considerations. “It will require specialised spacing and equipment, so won’t make sense for everyone, but in some cases to get to a footprint, it will,” Collins says.
He also says that its AC block is substantially different to others out there in the market in terms of its internal configuration: “If you look at ours you won’t see any wires or DC-DC connections: it’s all busbars and our communication systems are wireless. It’s a 30-minute time to replace a cell.”
He also repeated what others have said about the drive of ever more energy-dense DC blocks which now go well beyond 5MWh and the potential weight issues that might create for logistics, both in terms of port-to-site travel and installation once on site. AESI is aiming to keep its product under 45,000 pounds for this reason, as the doesn’t require special road permits or specialised cranes.
First projects
The firm’s big project will most likely be in the UK in the second quarter of 2025, Collins says. It signed a letter of intent (LOI) for 1.5GW of BESS for three projects from Ireland-headquartered utility and power generation firm ESB’s Scotland division for three projects in September.
“I have about 20 projects that will be completed in 2025, from California to Massachusetts, to Texas, Chile Cuba and Scotland. We haven’t branched out to Asia, Africa or the Middle East yet, as we’re just trying to get a foothold in the market.”
Battery cell strategy
Collins says a lot of his team are also ex-A123, which was the first company to commercialise LFP batteries, meaning the firm is well-placed for cell vetting and qualification. “Our process is very rigorous as no one has tested cells to the number of cycles that some are claiming.”
China-based OEM EVE Energy is the first supplier that AESI has qualified though it has others in qualification. It has designed its system around a 280-314Ah cell size, though Collins says there is a move by manufacturers to differing, larger cell form factors which presents a potential risk for system integrators and BESS manufacturers.
“Cell designers want to drive you to a design around their cell size, and that is a move away from the past. I don’t see switching form factors for your BESS as a viable strategy, as the cost and time of developing and qualifying a product and cell is huge,” he says, adding that designing a BESS around one company’s form factor leaves you locked in to that supplier.
The diversification of cell form factors, and the implications on the BESS landscape, were also explored in our piece on AC blocks.
Manufacturing
Collins also walks us through the manufacturing process and network that AESI is using, at a level of detail rarely given by system integrators and BESS manufacturers. He concedes the firm’s solution is more expensive than a typical DC block supplier, but it does save 5% on EPC costs to offset this. “We are very competitive,” he says.
It has a contract manufacturer in Suzhou, China, with 10GWh of contracted annual capacity today, and will have another contracted manufacturing facility in Malaysia from September 2025, also 10GWh of capacity.
“The contract manufacturer in Suzhou is one I used at A123 so I have a 25-year relationship with that person. We are very confident in their abilities. They do build products for our competitors, and are known to be high quality and reasonable cost.”
AESI designs the product and specs everything. It manufactures its EMS and BMS electronics for the super cell in the US, which are sent to the contract manufacturer. It contracts directly with the cell manufacturer, contract manufacturer and the metal sheet manufacturer separately, while the contract manufacturer procures select components on behalf of AESI but the firm is ‘very specific’ about these.
Its Malaysia site will assemble the product using Southeast Asia, non-China made cells: “We will supply our US requirements out of the Malaysia factory, and the rest of the world with the China factory.”
US domestic content
Perhaps surprisingly given its name, AESI has no near-term plans to manufacture its BESS in the US even with the tax credit incentives that exist for domestic manufacturing.
“Even with the investment tax credit (ITC) domestic content adder and the 45x manufacturing tax credit, its more than double the cost to do this in the US versus China or Malaysia,” Collins says.
“If you look at US-made cells, the cost quotations from the viable suppliers with plants that are making LFP batteries are double those from China. When you take the cost and the credit they get back, a buyer is still paying more than if they just bought from us.”
“We don’t know what Trump will do on Tariffs. Right now for Malaysia, it’s only a 3.5% duty. If he increases that to 10%? I pay around 11% now from China anyway.”
“We’ve investigated building a factory in Texas and manufacturing sheet metal. I was astounded by the costs given by large suppliers in those areas, and the cell cost was also shocking.”